ГОСТ Р 70939-2023. Национальный стандарт Российской Федерации. Потолки подвесные. Общие технические условия
Приложение А
(рекомендуемое)
МЕТОДИКА ПРОВЕДЕНИЯ ИСПЫТАНИЙ ПОДВЕСНОЙ СИСТЕМЫ "Т-ПРОФИЛЬ"
НА НЕСУЩУЮ СПОСОБНОСТЬ
А.1 Общие положения
А.1.1 Контрольные испытания нагружением выполняют с целью определения несущей способности подвесной системы "Т-профиль".
А.1.2 В результате испытаний подвесной системы определяют значения допустимой нагрузки до достижения предельного прогиба. Оценку несущей способности подвесной системы проводят изготовители по результатам испытаний при допустимом эксплуатационном прогибе не более L/300 (L - расстояние между точками подвесов вдоль основного несущего профиля или длина вспомогательного несущего профиля) и указывают в технической документации на продукцию.
А.1.3 Рекомендуется использовать для нагружения подвесной системы металлические потолочные панели, на каждую из которых сверху укладывают равномерно распределенные по площади грузы одинакового веса, последовательно увеличивая вес на каждом шаге испытаний по 500 г на м2. Допускается использовать другие значения шага нагружения, кратные 100 г.
При использовании для нагружения штучных грузов (металлических чушек, гирь, пластин, мешков с сыпучими материалами) эти грузы предварительно взвешивают и маркируют. Погрешность взвешивания не должна превышать +/- 0,01 кг.
А.1.4 Для испытаний необходимо применять жесткие регулируемые подвесы или металлические шпильки с жестким креплением к подвесной системе.
Угол наклона смонтированного подвеса по отношению к подвесной системе не должен превышать 5°.
А.1.5 Для измерения прогибов и перемещений следует применять измерительные приборы и инструменты с ценой деления не более 0,1 мм. Рекомендуется использовать:
- индикаторы часового типа по ГОСТ 577;
- штангенциркули по ГОСТ 166;
- стойки и штативы по ГОСТ 10197.
Допускается проводить измерения с использованием других средств, обеспечивающих не меньшую точность оценки.
А.1.6 Испытания подвесной системы следует проводить при температуре воздуха (20 +/- 5) °C. Изделия, хранившиеся при отрицательной температуре, должны предварительно выдерживать не менее 1 ч в помещении при рабочей температуре. Испытанию следует подвергать чистый сухой образец подвесной системы. До начала испытаний проводят контроль геометрической точности профилей на соответствие требованиям 5.3 и на соответствие аналогичным требованиям, приведенным в технических условиях (ТУ). Изделия, не отвечающие требованиям по геометрической точности, к испытаниям не допускаются.
А.1.7 Испытания следует проводить на специально отведенном участке, куда запрещается доступ посторонним лицам.
А.1.8 При испытании необходимо принять меры по предотвращению обрушения испытываемой конструкции.
А.1.9 Для испытания подвесной системы на несущую способность рекомендуется использовать схему монтажа, приведенную на рисунке А.1. Допускается использовать другую схему монтажа, соблюдая следующие требования:
а) стенд для проведения испытаний необходимо изготавливать из металлических труб сечением не менее 40 x 80, основание должно быть жестко закреплено;
б) расстояние между подвесами - 1200 мм;
в) расположение подвесов - на несущем профиле, максимально близко к пересечению несущего и поперечного профилей;
г) измеряют прогиб по центру основного несущего профиля (в равном удалении от всех подвесов);
д) измеряют не менее трех прогибов:
1) один прогиб в месте соединения основного несущего и поперечного профилей, расположенный в равном удалении хотя бы от двух подвесов,
2) два прогиба в местах замкового соединения вспомогательных несущих профилей, расположенных в равном удалении от несущего профиля.
Рисунок А.1 - Схема монтажа подвесной системы
для проведения испытаний на несущую способность
А.2 Порядок проведения испытаний
А.2.1 При испытаниях подвесной системы нагружать потолочные панели следует до эксплуатационного прогиба не более L/300.
А.2.2 Значения нагрузок в процессе испытаний регистрируют по массе штучных грузов, используемых для нагружения.
А.2.3 Последовательность загружения подвесной системы указывают в программе испытаний с учетом следующих требований:
- определяют прямым взвешиванием нагрузку от собственной массы смонтированных лицевых потолочных элементов;
- нагрузку следует прикладывать поэтапно ступенями (долями), каждая из которых не должна превышать 10% проектной (расчетной) нагрузки на подвесную систему;
- следует не допускать неравномерного загружения подвесной системы при испытании штучными грузами;
- перед проведением испытаний определяют значения допустимого прогиба в контрольных точках.
А.2.4 После приложения каждой доли нагрузки испытываемую подвесную систему выдерживают под нагрузкой не менее 2 мин.
А.2.5 Во время выдержки под нагрузкой следует производить тщательный осмотр поверхности подвесной системы и фиксировать:
- величину нагрузки каждого этапа нагружения и соответствующие результаты измерения прогиба;
- величину контрольного прогиба при достижении контрольной нагрузки.
А.2.6 После достижения контрольного прогиба испытания останавливают и фиксируют значение предельной нагрузки как суммарную массу потолочных панелей и груза на единицу площади (на квадратный метр).
А.2.7 Во время проведения испытания необходимо принимать меры к обеспечению безопасности работ.
А.3 Результаты испытаний
А.3.1 Результаты испытаний, проведенных в соответствии с настоящим стандартом, заносят в протокол и оформляют акт.
А.3.2 В зависимости от организации, которая проводила испытания, протокол хранят в лаборатории или в отделе технического контроля (ОТК) предприятия-изготовителя либо в испытательной лаборатории органа по сертификации.
А.3.3 Протокол испытаний должен содержать следующие сведения по испытаниям подвесной системы:
- номер протокола испытаний;
- дату проведения испытаний;
- наименование предприятия, основание и цель проведения испытаний;
- наименование испытываемой подвесной системы;
- описание и чертеж схемы монтажа с указанием мест расположения подвесов и средств измерения прогиба;
- описание основания, к которому прикреплены подвесы;
- описание использованных подвесов с указанием их несущей способности, а также способа их закрепления к основанию;
- массу загрузочных устройств;
- результаты испытаний;
- предельную нагрузку до достижения контрольного прогиба.
Необходимо, чтобы протокол испытания был заверен ответственными лицами.
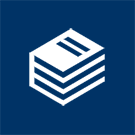