ГОСТ Р 59851-2021. Национальный стандарт Российской Федерации. Арматура трубопроводная. Требования к материалам арматуры, применяемой для сероводородосодержащих сред
4.2 Требования к материалам
4.2.1 Для изготовления деталей арматуры используют материалы, обеспечивающие их надежную работу в течение срока службы с учетом заданных условий эксплуатации.
4.2.2 Перечень материалов, допускаемых для изготовления арматуры, эксплуатирующейся в средах, содержащих сероводород с парциальным давлением 0,3 кПа и более в газовой фазе или свыше 6% (об), а также объем контроля материала основных деталей арматуры приведены в таблице 3.
Таблица 3
Марки материалов и объем контроля основных деталей арматуры
Вид заготовок | Наименование деталей | Марка материала | Разрушающие методы контроля | Неразрушающие методы контроля | |||||||||||
Контроль химического состава | Испытание на растяжение при температуре 20 °C | Испытание на ударный изгиб при температуре 20 °C | Испытание на ударный изгиб при отрицательной температуре | Контроль содержания неметаллических включений | Контроль макроструктуры | Контроль твердости | Контроль стойкости к СКР | Контроль HIC | Визуальный контроль | Радиографический контроль | УЗК | Капиллярный контроль | |||
Номер контрольной операции | |||||||||||||||
101 | 201 | 211 | 212 | 229 | 231 | 232 | 242 | 243 | 301 | 314 | 326 | 341 | |||
Отливки | Корпус, крышка | 20ГМЛ, 30ХМЛ, 25Л, LCB, LCC | +С | + | + | + | - | - | + | + | - | + | + | - | + |
Корпус, крышка, детали уплотнения затвора | 12Х18Н9ТЛ, 12Х18Н12М3ТЛ <*> | +С | + | - | - | - | - | + | - | - | + | + | - | + | |
Втулка направляющая | ЧН19Х3Ш, ЧН17Д3Х2 | +С | - | - | - | - | - | + | - | - | + | - | - | - | |
Поковки, штамповки, заготовки из проката | Корпус, крышка, фланец | 20КА | +С | + | + | + | +С | +С | + | + | - | + | - | + | + |
20ЮЧ, 09ГСНБЦ | +С | + | + | + | +С | +С | + | + | + <**> | + | - | + | + | ||
09Г2С, 09Г2СА-А, 30ХМА, A350LF2 (селект), ASTM A516 Gr70 (аналог 16ГС) | + | ||||||||||||||
Корпус, крышка, шток, шпиндель, детали уплотнения затвора, концевые детали сильфона | 08Х18Н10Т, 12Х18Н10Т, 10Х17Н13М2Т <*>, 10Х17Н13М3Т <*>, 08Х17Н15М3Т <*> ASTM A182 GrF316 (аналог 08Х17Н13М2Т) | +С | + | - | - | +С | +С | + | - | - | + | - | + | + | |
06ХН28МДТ <*> | +С | + | - | - | +С | +С | + | - | - | + | - | + | + | ||
ХН43БМТЮ-ВД | +С | + | + | - | +С | +С | + | - | - | + | - | + | + | ||
ХН55МБЮ-ВД | +С | + | - | - | +С | +С | + | - | - | + | - | + | + | ||
Хастеллой - ХН65МВУ-ВИ <*> | +С | + | - | - | +С | +С | + | - | - | + | - | + | + | ||
Втулка сальника | 08Х21Н6М2Т | +с | + | + | + | +С | +С | + | + | - | + | - | + | + | |
12Х18Н10Т, 08Х18Н10Т, 08Х18Н13М3Т <*> 10Х17Н13М2Т <*>, 10Х17Н13М3Т <*> | - | - | - | ||||||||||||
ХН55МБЮ-ВД <*> | +С | + | - | - | +С | +С | + | - | - | + | - | + | + | ||
Поковки, штамповки, заготовки из проката | Шток, шпиндель, ось | 07Х16Н6, 03Х12Н10МТР-ВД | +С | + | + | + | +С | +С | + | + | - | + | - | + | + |
07Х21Г7АН5, 07Х21Г7АН5-ВД | +С | + | + | - | +С | +С | + | + | - | + | - | + | + | ||
12ХН35ВТ, 12ХН35ВТ-ВД | +С | + | + | + | +С | +С | + | - | - | + | - | + | + | ||
ХН55МБЮ-ВД <*> | +С | + | - | - | +С | +С | + | - | - | + | - | + | + | ||
Детали с коррозионно-стойкой наплавкой | Корпус, уплотнительные поверхности фланцев, запорные элементы и др. | Inconel 718, Inconel 625, Autrod 309, ПР-НХ | + | - | - | - | - | - | + | - | - | + | - | - | + |
Детали с твердой износостойкой наплавкой | Корпус, золотник, диск и др. | Э-13Х16Н8М5С5Г4Б (ЦН-12М); Э-08Х17Н8С6Г (ЦН-6Л); Э-09Х31Н8АМ2 (УОНИ-13/Н1-БК, ЭЛ3-НВ1); Э-190КБ62Х29В5С2 (ЦН-2) | + | - | - | - | - | - | + | - | - | + | - | - | + |
<*> Марки материалов, применяемых в средах, содержащих ионы хлора. <**> Контроль HIC "+" - только для заготовок из проката.
Примечания 1 "+" - контроль проводится. 2 "-" - контроль не проводится. 3 "+С" - результаты испытаний допускается засчитывать по сертификатным данным. 4 Ответные фланцы должны быть изготовлены из материала, аналогичного материалу трубопровода или из стали того же класса. 5 При отсутствии в документах на поставку материала результатов контроля по макроструктуре, неметаллическим включениям контроль по этим операциям проводит изготовитель арматуры. 6 Для уровня УТТ 4 сварка не допускается. Допускается наплавка уплотнительных поверхностей твердыми и антикоррозионными материалами. 7 Наплавка ЦН-6Л применима при pH среды > 4. |
Допускается применение других материалов (в том числе импортных), не указанных в настоящем стандарте, при соблюдении требований настоящего стандарта и при согласовании со специализированной материаловедческой организацией.
Допускается применение других наплавочных материалов (порошковые, ленты и др.) отечественных и импортных, удовлетворяющих по химическому составу и твердости требованиям ГОСТ 10051, ГОСТ 33258.
4.2.3 Материалы должны удовлетворять требованиям стандартов или ТУ.
4.2.4 Верификацию (входной контроль) материалов и полуфабрикатов проводят по ГОСТ 24297, КД.
4.2.5 Использование материала, поступившего без сертификата, для изготовления основных деталей арматуры не допускается. При неполноте сертификатных данных применение материала допускается только после проведения изготовителем арматуры дополнительных испытаний и исследований, подтверждающих полное соответствие материалов требованиям стандартов или ТУ.
Номера сертификатов на материалы основных деталей указывают в паспорте на изделие.
4.2.6 Материалы и заготовки на складе и в цехах следует хранить раздельно по маркам и плавкам.
4.2.7 На материалах, заготовках и деталях в процессе обработки должна быть сохранена маркировка, обеспечивающая их прослеживаемость.
4.2.8 Легированные и коррозионно-стойкие стали и сплавы перед запуском в производство должны проходить 100%-ный стилоскопический контроль.
4.2.9 Виды контроля материалов деталей арматуры, сварных соединений и наплавок указывают в КД. Результаты контроля заносят в паспорт на изделие.
4.2.10 Химический состав заготовок контролируют по сертификату на материалы. В углеродистых и низколегированных сталях содержание никеля должно быть менее 1%.
4.2.11 Минимальную температуру испытания на ударный изгиб устанавливает заказчик в соответствии с ГОСТ 15150, при этом на образцах типа 11 по ГОСТ 9454 величина работы удара (KV) должна быть не менее 20 Дж (ударная вязкость KCV >= 25 Дж/см2).
Ударную вязкость коррозионно-стойких сталей аустенитного класса, железо-хромо-никелевых, хромо-никелевых, хромо-никель-молибденовых сплавов при отрицательной температуре не определяют.
4.2.12 Твердость углеродистых, низколегированных сталей должна быть не более 220 HB, стали 03Х12Н10МТР-ВД - не более 23 HRC, стали 07Х16Н6 - не более 31 HRC, сплавов 12ХН35ВТ, 12ХН35ВТ-ВД, ХН43БМТЮ-ВД, ХН55МБЮ-ВД, ХН65МВУ-ВИ - не более 35 HRC.
Твердость является сдаточной характеристикой, ее заносят в паспорт на изделие.
4.2.13 Испытание на стойкость против МКК - по ГОСТ 6032. Методы испытания указывают в КД.
4.2.14 Визуальный контроль заготовок проводят по требованиям и методике, указанным в КД и НД.
4.2.15 Испытание на стойкость к СКР - по НД (рекомендуемые НД - [2], [3]). При наличии в сертификате на поставку стали указания о проведении испытания на СКР повторное испытание изготовителем арматуры не проводят. Повторные испытания на СКР могут быть проведены по требованию заказчика арматуры исходя из условий ее эксплуатации.
4.2.16 Стойкость материалов против сероводородного разрушения по усмотрению заказчика может быть подтверждена:
- гарантией поставщика материалов, имеющего аттестованный технологический (производственный) процесс. При этом поставщик должен провести испытание на СКР не менее чем на пяти образцах от трех плавок каждого вида продукции (поковки, лист и др.);
- результатами лабораторных испытаний по оценке стойкости материалов против сероводородного разрушения, проведенных специализированной лабораторией, используемых для работы в средах с ;
- актами проведения обследования арматуры после эксплуатации в средах с .
4.2.17 Поковки и штамповки с уровнем содержания серы и фосфора менее 0,025% соответственно, а также отливки на HIC не испытывают. Испытание на HIC листов, труб и проката из углеродистых и низколегированных сталей - по НД (рекомендуемая НД - [4]).
4.2.18 Детали из проката, поковки и штамповки необходимо подвергать контролю капиллярной дефектоскопией в соответствии с НД и КД.
Отливки следует подвергать контролю капиллярным или магнитопорошковым методами в местах, указанных в КД. Контроль выполняют по ГОСТ 18442 или ГОСТ Р 56512 соответственно.
Контролю подвергают отливки после их окончательной обработки (термической, механической).
Контроль поверхности отливок из сталей перлитного класса и высокохромистых сталей после дробеструйной обработки выполняют только капиллярным методом контроля.
Обязательному контролю в отливках подлежат:
- радиусные переходы;
- концы под приварку к трубопроводу;
- поверхности, при визуальном контроле которых оценка результатов представляется неоднозначной.
Наличие несплошностей на поверхности отливок, контролируемых капиллярным или магнитопорошковым методами, определяют по индикаторным следам. Под индикаторным следом при капиллярном контроле следует понимать след, образованный индикаторным пенетрантом на слое проявителя, а магнитопорошковым методом - видимую длину валика осаждения магнитного порошка над несплошностью.
При оценке поверхностных несплошностей в отливках фиксации подлежат индикаторные следы размером более 1 мм.
Не допускаются:
- трещины;
- любые линейные индикаторные следы размером более 10% толщины стенки отливки плюс 1 мм для стенки толщиной не более 20 мм;
- любые линейные индикаторные следы размером более 3 мм для стенки толщиной от 20 до 60 мм и более 5 мм для стенки толщиной свыше 60 мм;
- любые округлые индикаторные следы размером более 30% толщины стенки отливки для стенки толщиной до 15 мм включительно и 5 мм для толщины стенки свыше 15 мм;
- более трех индикаторных следов, расположенных на одной линии на расстоянии менее 2 мм друг от друга (расстояние измеряется по ближайшим кромкам индикаторных следов);
- более девяти индикаторных следов в любом прямоугольнике площадью 40 см2, наибольший размер которого не превышает 150 мм.
При этом линейными считают индикаторные следы, длина которых в 3 раза и более превышает ширину, а под длиной и шириной понимают размеры прямоугольника с наибольшим отношением длины к ширине, в который может быть вписан данный индикаторный след.
На окончательно обработанных уплотнительных поверхностях несплошности, индикаторные следы которых имеют размер более 1 мм, не допускаются (если иное не указано в КД).
Отливки, которые имеют газовую (ситовидную) пористость, не допускают к исправлению и бракуют.
Исправлению подлежат все дефекты, наличие которых в отливках и кромках под сварку и на их поверхностях не допускается нормами, установленными настоящим стандартом и КД.
4.2.19 Литые детали должны быть подвергнуты контролю радиографическим методом по ГОСТ 7512 согласно КД. На каждый тип изделий составляют технологические карты радиографического контроля. При оценке качества отливки по результатам радиографического контроля учитывают дефекты размером более:
- 2 мм - для отливок с толщинами стенок не более 50 мм;
- 0,04S - для отливок с толщинами стенок свыше 50 мм, где S - толщина стенки, мм.
Величины допустимых дефектов приведены в таблице 4. Дефекты с большей величиной не допустимы.
Таблица 4
Допустимые дефекты для отливок при радиографическом контроле
Толщина стенки отливки, мм | Тип несплошности | Размер участка отливки, мм | Наибольший размер несплошностей на снимке, мм | Количество несплошностей, не более | Минимальное расстояние на снимке между несплошностями, мм |
До 25 включ. | Газовая раковина (Рг). Песчаное и шлаковое включения (Вп.ш) | 130 x 180 | 6 | 6 | 10 |
Усадочная рыхлота (Ру) | 0,3S + 5 | 1 | |||
Свыше 25 до 50 включ. | Рг Вп.ш | 6 | 8 | ||
Ру | 0,3S + 5 | 1 | |||
Свыше 50 до 100 включ. | Рг Вп.ш | 6 | 10 | 15 | |
Ру | 0,3S + 5 | 1 | |||
Свыше 100 до 300 включ. | Рг Вп.ш | 130 x 280 | 6 | 12 | |
Ру | 0,1S + 25 | 1 | |||
Свыше 100 до 300 включ. | Рг Вп.ш | 180 x 280 | 0,035S | 12 | |
Ру | 0,1S + 25, но не более 65 | 1 | |||
Примечания 1 Допускается скопление дефектов типа Рг или Вп.ш, имеющих размеры меньше, чем приведены в данной таблице. 2 Допускается принимать за единичный дефект при условии, что линейный размер скопления не превышает величин, указанных в данной таблице. 3 Если на одной рентгеновской пленке зафиксированы дефекты Рг, Вп.ш, Ру, то дефекты Ру допускают без исправления при условии соответствия их параметров норме, при этом количество дефектов Рг и Вп.ш должно быть вдвое меньше, чем указано в данной таблице. 4 В случае наличия дефектов, превышающих величины, указанные в таблице, решение о возможности их допуска принимают в каждом конкретном случае с учетом месторасположения, допустимости для ремонта и потенциальной опасности дефекта с оформлением карточки разрешения отступления в установленном порядке. 5 Если размеры отливки менее 130 x 180 мм или 180 x 280 мм, то количество несплошностей, допускаемых без исправления, должно быть уменьшено по отношению к установленному в данной таблице пропорционально отношению площади этой отливки и участка с размерами, указанными в таблице для соответствующей толщины отливки. |
4.2.20 Поковки, штамповки и заготовки из проката контролируют УЗК в объеме 100%.
Методика контроля - по ГОСТ 24507, ГОСТ 21120, ГОСТ 22727.
Нормы оценки для заготовок из углеродистых и низколегированных сталей:
- поковки - по группе качества 4n (ГОСТ 24507);
- листы - по классу сплошности 0 (ГОСТ 22727);
- прутки - по группе качества 1 (ГОСТ 21120).
Нормы оценки заготовок из коррозионно-стойких сталей и сплавов - по ТУ.
4.2.21 Расчет на прочность корпусных деталей арматуры из углеродистых, низколегированных и легированных сталей - по ГОСТ 34233.10.
4.2.22 Значение эквивалента углерода для материалов патрубков, корпусов, катушек, предназначенных под приварку к трубопроводу, должно составлять: [C]э <= 0,41.
Для агрессивного газа - [C]э <= 38%.
Фактическую величину [C]э указывают в технологическом паспорте и паспорте на арматуру и маркируют на концах деталей под приварку к трубопроводу. Для низколегированных сталей эквивалент углерода [C]э рассчитывают по формуле
. (2)
Медь, никель, хром, содержащиеся в сталях как примеси, при расчете [C]э не учитывают, если их суммарное содержание не превышает 0,2%.
Величину эквивалента углерода углеродистых и низколегированных сталей только кремнемарганцовистой системой легирования, например 09Г2С, 17Г1С и др., рассчитывают по формуле
. (3)
4.2.23 Стали марок 20КА, 20ЮЧ, 09Г2С, 09Г2СА-А, 09ГСНБЦ, A350LF2 (селект) для изготовления корпусных деталей могут применять в средах, содержащих H2S, до температуры 260 °C, сталь 20ГМЛ - до температуры 80 °C.
Аустенитные нержавеющие стали для корпусных деталей применяют при температуре рабочей среды не выше 66 °C и парциальном давлении не выше 100 кПа.
Сплавы марок ХН43БТЮ-ВД, ХН55МБЮ и ХН65МВУ применяют для деталей арматуры при добыче нефти и газа без ограничения по температуре, , содержанию Cl- и pH.
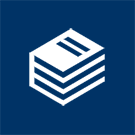