ГОСТ Р 59851-2021. Национальный стандарт Российской Федерации. Арматура трубопроводная. Требования к материалам арматуры, применяемой для сероводородосодержащих сред
4.7 Требования к сварке и наплавке
4.7.1 Сварку выполняют по ГОСТ 33857.
4.7.2 Конструкция сварных соединений корпусных деталей арматуры и других деталей при возможности должна предусматривать получение сварных швов с полным проплавлением на всю толщину металла. При наличии конструктивного зазора (непровара) не должно быть замкнутой полости или должна быть произведена засверловка отверстия в зону конструктивного зазора для выхода H2S из замкнутой полости.
При входном контроле дополнительно для сварочных материалов перлитного класса, предназначенных для автоматической, полуавтоматической, электрошлаковой сварки и др., по действующей ТД изготовителя необходимо определять химический состав металла шва (наплавленного металла).
4.7.3 Технология сварки, применяемая при изготовлении и ремонте арматуры, должна быть аттестована в установленном порядке. При аттестации технологии сварки необходимо дополнительно изготавливать контрольные сварные соединения из углеродистых и низколегированных сталей для определения твердости металла шва и зоны термического влияния (от 1 до 2 мм от шва) и основного металла. Твердость не должна превышать 220 HB.
Контрольные образцы для определения твердости изготавливают из сварных соединений, детали которых изготавливают из таких же марок сталей и плавок, как и контролируемые сварные соединения. Сварку контрольных сварных соединений выполняют такими же сварочными материалами по марке, плавке, как и контролируемые сварные соединения, на таких же режимах сварки. Толщина контрольного образца должна соответствовать толщине контролируемого соединения по технологии со всеми припусками на механическую обработку.
Контрольные образцы могут распространяться для других изделий, сварные соединения которых отличаются по толщине от контрольного образца не более чем на 3 мм включительно
Sк.с <= (Sс.с +/- 3) мм, (4)
где Sк.с - толщина контролируемого сварного соединения;
Sс.с - толщина контролируемого сварного соединения по абсолютному размеру изделия.
4.7.4 Контроль качества и оценка дефектов сварных соединений - по ГОСТ 33857.
Методы и объем контроля сварных соединений назначает разработчик КД в зависимости от условий эксплуатации с учетом возможности проведения контроля:
- сварные соединения корпусных деталей подлежат контролю по I категории ГОСТ 33857-2016 (таблица 11) в объеме, указанном в ГОСТ 33857-2016 (таблица 12);
- остальные сварные соединения - в соответствии с требованиями КД.
В КД могут быть указаны другие методы контроля сварных соединений по требованию заказчика, отсутствующие в ГОСТ 33857 и настоящем стандарте.
4.7.5 Для остальных сварных соединений, находящихся внутри корпуса под давлением рабочей среды (сильфонные сборки, диски, шток, плунжер, направляющие и др.) и не находящихся под давлением рабочей среды (рукоятки, опоры, ребра жесткости и др.), методы и объем контроля устанавливает разработчик КД.
4.7.6 Испытание на стойкость против МКК металла шва аустенитного класса - по ГОСТ 6032, метод контроля указывают в КД. В случае необходимости в КД может быть оговорено требование об испытании на стойкость против МКК как металла шва, так и всего сварного соединения.
4.7.7 Наплавка и контроль качества наплавки коррозионно-стойкими и твердыми износостойкими материалами - в соответствии с ГОСТ 33258.
Аттестация сварщиков для проведения наплавочных работ - по программам, разработанным изготовителем арматуры в соответствии с ГОСТ 33258.
4.7.8 Наплавку сварочными материалами аустенитного класса выполняют по технологии, указанной в ГОСТ 33258 и ГОСТ 33857, контроль качества наплавленной поверхности - по ГОСТ 33258.
4.7.9 Испытание сварных соединений (образцов) на стойкость к СКР и HIC - по НД (рекомендуемые НД - [2], [3]).
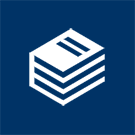