ГОСТ Р 59109-2020. Национальный стандарт Российской Федерации. Элементы реакционных трубчатых печей, работающих под давлением. Технические условия
6.7 Сварка
Сварка радиантных труб, их элементов и коллекторов радиантных труб должна быть выполнена в соответствии с положениями настоящего стандарта и ТД, утвержденной в установленном порядке.
6.7.1 Специальные требования
6.7.1.1 При подготовке к сварке сталей и сплавов аустенитного класса кроме общих положений (см. 6.5) должны быть учтены специальные требования, изложенные в настоящем подразделе.
6.7.1.2 Требования к испытаниям на сопротивляемость образованию трещин в сварных соединениях
Сварочная проволока каждой партии должна быть проконтролирована на стойкость к образованию горячих трещин при сварке.
Требования к испытаниям на сопротивляемость образованию горячих трещин в сварных соединениях должны соответствовать ГОСТ Р ИСО 17641-1, ГОСТ Р ИСО 17641-2 и ГОСТ Р 54790.
Металл сварного шва и зоны термического влияния сварки аустенитных сплавов на никелевой основе чувствителен к воздействию окружающей атмосферы (в том числе влажности), масел и прочих загрязнений, которые приводят к образованию горячих трещин и пор. Для предотвращения образования горячих трещин требуется организация сварочных работ.
При разработке технологии сварки аустенитных сталей (или сплавов) на никелевой основе необходимо учитывать:
- технологические особенности сварного соединения (требования к подогреву при сварке, термообработке и пр.);
- возможность образования дефектов, особенно холодных и горячих трещин, специфичных для каждого свариваемого сплава;
- возможность образования горячих трещин при отсутствии зазора между свариваемыми кромками стыковых соединений для обеспечения свободной усадки металла;
- необходимость и достаточность обеспечения механических свойств сварного соединения в соединениях сплавов разной толщины не ниже, чем у сплава, обладающего меньшими показателями указанных свойств.
Сварочная проволока каждой партии должна быть проконтролирована на стойкость к образованию холодных трещин при сварке.
Требования к испытаниям на сопротивляемость образованию холодных трещин в сварных соединениях должны соответствовать ГОСТ Р ИСО 17642-1, ГОСТ Р ИСО 17642-2 и ГОСТ Р 56143.
Сварочные материалы, предназначенные для выполнения сварных соединений, к которым предъявляются требования по стойкости к МКК, перед использованием должны быть подвергнуты испытаниям на склонность к МКК по ГОСТ 6032. Испытание сварочных материалов на склонность к МКК допускается совмещать с испытанием на склонность к МКК сварных соединений, для сварки которых они предназначены.
6.7.1.3 Каждая партия электродов независимо от наличия сертификата подвергается контрольным испытаниям для определения технологических свойств, а также склонности к образованию трещин по ГОСТ 9466.
Результаты контроля технологических свойств должны удовлетворять требованиям ГОСТ 9466.
6.7.1.4 Резка изделий из сталей и сплавов аустенитного класса, а также обработка кромок под сварку должны быть выполнены механическими способами.
В случае применения термической (пламенной) резки на кромках должен быть удален механическим способом слой металла до полного устранения всех неровностей, цветов побежалости и возможных горячих трещин.
6.7.1.5 Для предотвращения дефектов при сварке в защитных газах и возможного снижения коррозионной стойкости металла шва сварочную проволоку перед использованием необходимо обезжирить ацетоном высшего сорта (ГОСТ 2768).
6.7.1.6 Для уменьшения перегрева, обеспечения коррозионной стойкости и оптимальных механических свойств сварку соединений небольшой толщины (менее 8 мм) необходимо вести при максимально возможной скорости.
6.7.1.7 При многослойной сварке каждый проход выполняют после охлаждения предыдущего до температуры ниже 100 °C и тщательной зачистки (абразивным камнем или металлическими щетками из нержавеющей стали).
6.7.1.8 Для предотвращения горячих трещин в сварных соединениях (толщиной 10 мм и более) сталей и сплавов с аустенитной структурой рекомендуется следующее:
- аргонодуговую сварку и ручную дуговую как плавящимся, так и неплавящимся электродом выполнять при минимальной длине дуги, без поперечных колебаний усиленными валиками;
- автоматическую сварку осуществляют на пониженных скоростях с минимальным числом проходов;
- кратеры швов тщательно заплавлены до получения выпуклого мениска или вышлифованы при запрете выводить кратеры на основной металл;
- в случае вынужденного обрыва дуги до ее повторного возбуждения необходимо убедиться в отсутствии горячей кратерной трещины, при наличии трещины кратер удалить механическим способом;
- сварщики, допущенные к сварке сталей и сплавов аустенитного класса, должны быть обучены приемам борьбы с горячими трещинами.
6.7.2 Технология сварки
Режим сварки должен обеспечить оптимальные значения темпа деформаций, скорости охлаждения и погонной энергии сварки для получения благоприятной структуры и сопротивления образованию трещин.
6.7.2.1 Сварка стыкуемых элементов должна быть выполнена под руководством специалиста аттестованными сварщиками, имеющими опыт аргоно-дуговой сварки труб (отливок, поковок) из аустенитных сталей и сплавов. Сварщики должны пройти специальное обучение по отработке технологии сварки центробежнолитых и деформированных труб с фасонными отливками, отводами, фланцами с полным проплавлением корневого шва.
Перед изготовлением сварных радиантных труб предприятие обязано выполнить производственную аттестацию технологии сварки в соответствии с [29].
6.7.2.2 При выполнении корневого шва и отсутствии зазора в стыке или при зазоре не более 0,5 мм аргоно-дуговая сварка должна быть осуществлена без подачи проволоки, а при наличии зазора от 0,5 до 1,5 мм - с подачей проволоки.
6.7.2.3 Зажигание и гашение дуги должны быть выполнены или на кромке трубы, или на уже наложенном шве на расстоянии от 20 до 25 мм от конца шва. Зажигание дуги на поверхности трубы не допускается.
6.7.2.4 Рекомендуемый расход аргона в горелке - от 8 до 10 л/мин, на поддув во внутреннюю полость трубы - от 5 до 7 л/мин.
6.7.2.5 Для защиты сварочной ванны корневого слоя при аргоно-дуговой сварке следует устанавливать заглушки с подачей инертного газа внутрь полости. Подачу аргона во внутреннюю полость трубы необходимо начинать не менее чем за 2 - 2,5 мин до начала сварки.
6.7.2.6 Подача аргона в горелку должна быть прекращена через 5 - 8 с после обрыва дуги, и в течение этого времени струю аргона следует направлять в кратер для защиты металла от окисления.
6.7.2.7 Поверхность корневого шва со стороны внутренней поверхности трубы (отливки) должна быть ровной с усилением (1 +/- 0,5 мм) и с плавным переходом к основному металлу, что следует проверять с помощью эндоскопа.
В случае превышения указанного усиления сварной шов подвергают шлифовке с внутренней стороны. При этом не допускается повреждение внутренней стороны трубы (отливки).
6.7.2.8 Во избежание прожога металла корневого шва второй слой рекомендуется выполнять с подачей присадки.
6.7.2.9 Аргоно-дуговую сварку осуществляют на возможно короткой дуге узкими валиками при силе тока от 80 до 100 А. Ручную дуговую сварку выполняют электродами диаметром 3 мм при силе тока от 80 до 90 А или электродами диаметром 4 мм при силе тока от 100 до 120 А. Перед гашением дуги сварщик должен заварить кратер и вывести место обрыва дуги на шов на 8 - 10 мм против направления сварки. Последующее зажигание дуги осуществляют на металле шва на расстоянии от 12 до 15 мм от кратера. Вывод кратера и зажигание дуги на основном металле труб (отливок) не допускаются.
6.7.2.10 После наложения каждого слоя (валика) проводят визуальный осмотр шва на отсутствие дефектов. Дефектные участки шва должны быть удалены механическим способом и заварены вновь.
Поверхность каждого наплавленного валика перед наложением последующего слоя следует зачищать механическим способом (абразивным кругом или щетками из нержавеющей стали) и обезжирить. Каждый технологический слой, особенно кратер, необходимо проконтролировать на предмет обнаружения горячих трещин. Сварку сталей и сплавов, проявляющих склонность к образованию горячих трещин (в том числе коррозионно-стойких сплавов на никелевой основе), следует осуществлять на режимах с ограничением погонной энергии.
Для исключения трещин в кратерах необходимо обеспечить их полное заполнение с образованием выпуклой поверхности.
6.7.2.11 При сварке высоколегированных аустенитных сталей и сплавов на железоникелевой основе следует ограничивать температуру свариваемой поверхности стыка. Сварку последующего слоя шва выполняют после охлаждения предыдущего слоя ниже 100 °C. При сварке теплоустойчивых сталей руководствоваться инструкциями предприятия-изготовителя, согласованными с независимыми экспертными материаловедческими организациями.
6.7.2.12 Все сварные швы подлежат клеймению, позволяющему установить сварщика, выполняющего эти швы.
6.7.2.13 Клеймо на деформированных трубах (изготовленных из стали марки 20Х25Н20С и сплавов марок 05Х20Н32Т, 10Х20Н32ТЮ и др.) наносят на расстоянии от 20 до 50 мм от шва, глубина клеймения - не более 0,5 мм.
6.7.2.14 Клеймо на центробежнолитых трубах наносят на наплавленную и зашлифованную площадку диаметром от 10 до 12 мм, расположенную в околошовной зоне на расстоянии от 30 до 50 мм от шва.
6.7.2.15 Допускается обозначение клейм сварщиков приводить на схеме трубы, приложенной к паспорту.
6.7.3 Требования к качеству сварных соединений
Требования к качеству сварных соединений радиантных труб, их элементов и коллекторов радиантных труб должны соответствовать положениям настоящего стандарта и НТД, утвержденных в установленном порядке.
6.7.3.1 Сварные соединения труб (центробежнолитых, деформированных), бобышек, фланцев, фасонных отливок, гнутых и штампосварных отводов должны быть выполнены с полным проплавлением по всему периметру стыка.
6.7.3.2 Усиление корневого шва с внутренней стороны должно быть в пределах от 0,5 до 1,5 мм, местная "утяжка" (ослабление) шва - не более 0,5 мм.
Усиление шва с наружной стороны свариваемых элементов должно быть в пределах (1,5 +/- 1,0) мм.
6.7.3.3 В сварных соединениях не допускаются следующие внешние дефекты:
- трещины всех видов и направлений;
- свищи и пористость;
- подрезы, наплывы, прожоги и незаплавленные кратеры;
- смещение и совместный увод кромок свыше норм, предусмотренных настоящим стандартом и НТД, утвержденных в установленном порядке;
- несоответствие формы и размеров швов требованиям чертежа, проекта и настоящего стандарта.
6.7.3.4 В сварных соединениях не допускаются следующие внутренние дефекты:
а) трещины и микротрещины всех видов и направлений;
б) непровары швов, провисание корня шва;
в) свищи, поры в виде сплошной сетки;
г) единичные шлаковые и газовые включения шириной (диаметром) свыше 10% от толщины стенки, длиной более 0,25·S (S - толщина стенки), количество дефектов допускаемых размеров должно быть не более 5 шт. на стык;
д) цепочки пор и шлаковых включений, имеющих суммарную длину дефектов более толщины стенки на участке шва, равном десятикратной толщине стенки, а также отдельные дефекты с размерами, превышающими указанные в перечислении г) настоящего подпункта;
е) скопление газовых пор и шлаковых включений на отдельных участках шва свыше 5 шт. на 1 см2 площади шва; при этом максимальный линейный размер отдельного дефекта по наибольшей протяженности не должен превышать 1,5 мм, а сумма их линейных размеров в стыке - 3 мм.
6.7.3.5 Предел прочности сварных соединений центробежнолитых труб должен быть не ниже фактического предела прочности основного металла труб.
6.7.4 Контроль качества сварных соединений
Контроль качества сварных соединений радиантных труб, их элементов и коллекторов радиантных труб должен быть выполнен в соответствии с положениями настоящего стандарта и НТД, утвержденной в установленном порядке.
6.7.4.1 Контроль качества сварных соединений элементов проводят следующими методами:
- пооперационным контролем;
- визуально-измерительным контролем (ВИК);
- цветным методом неразрушающего контроля (НК);
- механическими испытаниями, в том числе испытаниями на длительную прочность;
- испытаниями на межкристаллитную коррозию (по требованию ТД на изделие);
- радиографическим контролем;
- металлографическими исследованиями (по требованию ТД на изделие);
- гидроиспытанием.
6.7.4.2 Требования к оценке качества контрольных сварных соединений должны соответствовать данным, приведенным в таблице 12.
Таблица 14
Требования по контролю контрольных сварных соединений
Характеристика испытаний | Метод контроля | Объем контроля | Нормативная документация (НД) по методике контроля | НД по оценке качества |
Обязательные испытания | Визуальный (внешний осмотр) | 100% | [37] | [17], [18], [42] |
Измерительный | 100% | [37] | ||
Радиографический | 100% | ГОСТ 7512, [38], [39] | ||
Капиллярный (цветной метод НК) | 100% | ГОСТ 18442 | ||
Растяжение и изгиб (механические испытания) | Четыре образца (два - на статическое растяжение; два - на статический изгиб) | ГОСТ 6996, [40] | ||
Испытания на МКК | При наличии соответствующего требования в технических условиях на изделие или в чертежах | ГОСТ 6032 | ||
Металлография | Три образца | [41] | ||
Стилоскопирование | 100% | [42] | ||
Дополнительные испытания | Испытание на длительную прочность (периодический контроль - не реже одного раза в три года) | По три образца на три напряжения при расчетной температуре стенки свариваемых элементов | ГОСТ 10145 |
|
Испытания на сопротивляемость образованию горячих трещин | Три образца | ГОСТ Р ИСО 17641-1, ГОСТ Р ИСО 17641-2, ГОСТ Р 54790 | ||
Испытания на сопротивляемость образованию холодных трещин | Три образца | ГОСТ Р ИСО 17642-1, ГОСТ Р ИСО 17642-2, ГОСТ Р 56143 |
6.7.4.3 Результаты контрольных испытаний сварных соединений должны быть занесены в паспорт. Протоколы и заключения по результатам контрольных испытаний сварных соединений должны быть приложены в паспорт.
6.7.4.4 Пооперационный контроль
В процессе пооперационного контроля проверяют:
- соответствие состояния и качества свариваемых элементов и сварочных материалов требованиям действующих стандартов и ТУ;
- соответствие качества подготовки кромок и сборки под сварку требованиям технологических указаний, разработанных в установленном порядке;
- соблюдение технологического процесса сварки.
6.7.4.5 Внешний осмотр и измерение
Внешнему осмотру и измерению подлежат все сварные соединения (доступные к осмотру и измерению) по всей протяженности с наружной и внутренней (с помощью эндоскопа) сторон.
Внешний осмотр следует проводить в соответствии с требованиями ГОСТ 3242.
Обнаруженные в процессе осмотра или измерения недопустимые дефекты должны быть устранены.
6.7.4.6 Цветной метод неразрушающего контроля
Цветной метод НК (цветная дефектоскопия) относится к капиллярным методам и предназначен для выявления дефектов типа несплошностей, выходящих на поверхность.
Цветной метод НК должен быть применен согласно [15].
Сварные соединения элементов подлежат 100%-ному цветному методу контроля.
Цветному методу НК подлежат поверхности корневого и последнего слоев по всей протяженности каждого стыка.
Необходимый класс чувствительности контроля цветным методом по ГОСТ 18442 обеспечен применением соответствующих дефектоскопических материалов при выполнении требований [15].
Поверхность, подлежащая контролю цветным методом, должна быть очищена от металлических брызг, нагара, окалины, шлака, ржавчины, различных органических веществ (масел и т.п.) и других загрязнений.
При наличии металлических брызг, нагара, окалины, шлака, ржавчины и других загрязнений поверхность подлежит механической зачистке.
Очистку поверхности от воды, жировых и от прочих органических загрязнений необходимо проводить в соответствии с требованиями [15].
Шероховатость контролируемой поверхности должна соответствовать требованиям приложения А [15] (категория 1, класс II).
Поверхность, подлежащая контролю цветным методом, должна быть принята службой ОТК по результатам визуального контроля.
Контроль цветным методом должен быть выполнен специалистами, прошедшими теоретическую и практическую подготовку, аттестованными в установленном порядке и имеющими соответствующие удостоверения.
Оценку качества поверхности по результатам контроля цветным методом необходимо проводить по форме и размеру рисунка индикаторного следа в соответствии с [15] (таблица 2, класс дефектности 2).
Обнаруженные при контроле цветным методом недопустимые дефекты должны быть устранены.
6.7.4.7 Механические испытания
Проверку механических свойств сварных соединений центробежнолитых (деформированных) труб с фасонными отливками, отводами, фланцами осуществляют на образцах, изготовленных из контрольных стыков по ГОСТ 6996 и [39].
Порядок выполнения сварных контрольных соединений и проверка их на отсутствие недопустимых дефектов должны соответствовать требованиям НТД на контролируемое изделие.
Сварку контрольных соединений проводят одновременно со сваркой изделия каждым сварщиком с применением тех же основных и присадочных материалов, тех же методов и режимов сварки, которые используются при сварке изделия.
Сварку контрольных соединений проводят для каждой партии основного металла, сварочной проволоки и электродов. Количество сварных соединений должно быть не менее 1% (но не менее одного) от общего числа сваренных каждым сварщиком однотипных сварных соединений.
При выполнении испытаний по определению характеристик механических свойств контрольных сварных соединений на отдельных образцах вырезка заготовок для изготовления образцов должна быть проведена в соответствии со схемами, установленными производственными инструкциями по сварке и контролю сварных соединений (в зависимости от специфики сварных соединений и положений сварки на различных участках шва).
Из каждого контрольного сварного соединения должны быть вырезаны четыре образца для испытания на статическое растяжение (два образца) и на статический изгиб (два образца) в соответствии с требованиями ГОСТ 6996. Испытания на статический изгиб образцов из конкретных марок сталей и сплавов проводят согласно требованиям ПКД.
Временное сопротивление разрыву сварных соединений должно быть не ниже фактического временного сопротивления разрыву основного металла. Общий результат испытаний считается неудовлетворительным, если как минимум один из образцов показал результат, отличающийся от установленных норм (в сторону снижения): по временному сопротивлению разрыву - более чем на 10%.
Указанные положения сохраняют силу и в том случае, когда среднее арифметическое результатов испытаний соответствует нормативным показателям.
Показатели характеристик механических свойств сварных соединений элементов из сталей разнородных марок должны удовлетворять требованиям к однородным сварным соединениям тех же элементов (из стали соответствующих марок) с более низкими нормативными показателями характеристик механических свойств.
При получении неудовлетворительных результатов по механическим испытаниям необходимо проведение повторных испытаний на образцах, вырезанных из того же контрольного стыка. При этом принимается удвоенное количество образцов.
В случае невозможности вырезки требуемого количества образцов из тех же контрольных соединений повторные механические испытания (в удвоенном объеме) должны быть проведены на выполненных производственных стыках, вырезаемых непосредственно из контролируемых изделий.
Если при повторном испытании как минимум на одном из образцов получены результаты, не отвечающие установленным нормам, то общий результат механических испытаний считается неудовлетворительным.
При получении неудовлетворительного результата после повторного испытания швы считаются неудовлетворительными.
Периодически, не реже чем один раз в три года, проводят контрольную проверку соблюдения технологии изготовления труб и контрольные испытания на длительную прочность сварных соединений.
6.7.4.8 Испытания на межкристаллитную коррозию
Испытание сварных соединений на стойкость к МКК следует проводить при входном контроле сварочных материалов при наличии соответствующего требования в ТУ на изделие или в чертежах.
Стойкость сварных соединений к МКК оценивают на образцах, вырезанных из наплавленного металла или сварных соединений. Форма, размеры и количество образцов должны соответствовать требованиям ГОСТ 6032. При изготовлении образцов основной слой должен быть полностью удален. Метод испытания должен быть указан в техническом проекте или в чертеже.
6.7.4.9 Радиографический контроль (РГК)
Сварные соединения элементов подлежат 100%-ному РГК.
РГК сварных соединений следует проводить в соответствии с ГОСТ 7512 и [38].
Кольцевые сварные соединения следует контролировать по схемам согласно [38] (рисунок 2).
К проведению радиографического контроля допускаются специалисты, прошедшие теоретическое и практическое обучение по специальной программе, согласованной и утвержденной в установленном порядке, сдавшие экзамен и получившие удостоверения о допуске их к соответствующему виду контроля сварных соединений.
Программа обучения дефектоскопистов должна включать раздел по технике безопасности и производственной санитарии.
Радиографический контроль проводят с целью выявления в сварном соединении трещин, непроваров, пор, металлических и неметаллических включений.
При невозможности визуального контроля сварного соединения радиографический контроль может быть применен и для выявления внешних дефектов: вогнутости корня, превышения проплава, подреза, прожога, утяжин и т.д.
При радиографическом контроле не обеспечивается выявление следующих дефектов:
- пор и включений с диаметром поперечного сечения менее удвоенной чувствительности контроля;
- непроваров и трещин глубиной менее удвоенной чувствительности контроля;
- непроваров и трещин, плоскость раскрытия которых не совпадает с направлением просвечивания;
- металлических и неметаллических включений с коэффициентом ослабления излучения, близким к коэффициенту ослабления основного металла сварного соединения;
- любых дефектов, если их изображения на снимках совпадают с изображениями посторонних деталей, острых углов или резких перепадов толщин свариваемых элементов.
Для определения чувствительности радиографического контроля следует применять канавочные и проволочные эталоны чувствительности по ГОСТ 7512.
Гаммаграфический метод контроля следует осуществлять в случае невозможности или технической трудности применения рентгенографического метода и для контроля изделий в монтажных условиях.
РГК проводят после устранения обнаруженных при внешнем осмотре дефектов.
Околошовная зона, зачищенная от окалины, шлака, брызг расплавленного металла и других загрязнений, должна иметь ширину не менее 20 мм (15 мм при сварке сплавов с микролегированием).
Расшифровке подлежат радиографические снимки, полностью высушенные, не имеющие на поверхности царапин, загрязнений, пятен, отпечатков пальцев, подтеков, белого налета, следов электроразрядов и других дефектов, затрудняющих расшифровку снимков.
К работам по расшифровке радиографических снимков и выдаче по ним заключений о качестве сварных соединений допускаются специалисты и дефектоскописты соответствующего уровня квалификации, в удостоверении которых должна быть соответствующая отметка.
Если в процессе радиографического контроля будут получены неудовлетворительные результаты (выявлены недопустимые дефекты, указанные в 6.7.3.3, 6.7.3.4), швы считаются непригодными.
6.7.4.10 Металлографические исследования
С целью выявления возможных внутренних дефектов (трещин, непроваров, пор и др.) сварные соединения подвергают металлографическому исследованию, состоящему из макро- и микроструктурного анализа.
Металлографическое исследование проводят по [41] в качестве арбитражного при контроле качества сварных соединений радиографическим методом.
Для проведения металлографических исследований из контрольных сварных соединений должно быть вырезано три образца.
Макро- и микроструктурный анализы должны быть проведены последовательно на одном и том же образце (шлифе).
Контролируемая поверхность макрошлифа должна включать сечение шва, зону термического влияния с прилегающими к ней участками основного металла, не находившимися под термическим воздействием сварки.
Макроструктурный анализ проводят на макрошлифах невооруженным глазом или с помощью лупы до тридцатикратного увеличения, бинокулярного стереомикроскопа МБС-2 или других микроскопов с параметрами не хуже, чем у указанного.
С помощью макроанализа выявляют следующее: возможные внутренние дефекты сварных соединений - трещины всех видов и направлений; непровары и несплавления, расположенные в сечении сварного соединения; свищи и поры; шлаковые и другие включения; подрезы, наплывы, провисание и незаплавленные кратеры; смещение и совместный увод кромок свариваемых элементов.
Исследование микрошлифа проводят с помощью металлографических инвертированных микроскопов МИМ-7, МИМ-8 (или других металлографических микроскопов с параметрами не хуже, чем у указанных) при стократном, четырехсоткратном увеличении и выше.
С помощью микроанализа выявляют следующее: возможные внутренние дефекты сварных соединений; микротрещины всех видов и направлений, непровары или несплавления, расположенные в сечении сварного соединения между отдельными валиками или основным металлом и металлом шва; свищи и поры; шлаковые и другие неметаллические включения.
Если получены неоднозначно трактуемые результаты металлографического исследования, то допускается повторное испытание на удвоенном количестве образцов, вырезанных из того же контрольного стыка или сварного соединения сборочной единицы или детали. В случае неудовлетворительных результатов при повторном металлографическом исследовании швы считаются непригодными.
6.7.4.11 Гидравлические испытания сварных соединений
Сваренные изделия ("труба + труба", "труба + фланец", "труба + бобышка", "труба + фасонное литье", "труба + гнутый отвод", "труба + штампосварной отвод" и их комбинации) подлежат гидравлическому испытанию в соответствии с требованиями ПКД, а также ТД [43]. Пробное давление выдерживают в течение 10 мин (испытание на прочность), после чего снижают до расчетного давления, при котором проводят тщательный осмотр сварных швов (испытание на герметичность).
По окончании осмотра давление вновь повышают до пробного и выдерживают еще 5 мин, после чего повторно снижают до расчетного и вторично осматривают трубу.
Продолжительность испытания на прочность и герметичность определена временем осмотра трубы.
Результаты гидравлического испытания на прочность и герметичность признаются удовлетворительными, если во время испытания не произошло разрывов, видимых деформаций, падения давления по манометру, а в основном металле и сварных швах не обнаружены течи и запотевания.
Если при испытании будут обнаружены:
- падение давления по манометру;
- пропуски испытательной среды (течь, потение, пузырьки воздуха или газа);
- признаки разрыва;
- остаточные деформации,
то дефектные сварные соединения удаляются, свариваются вновь и подлежат повторному контролю.
В случае отрицательного результата повторного контроля общий результат считается неудовлетворительным.
6.7.4.12 Стилоскопирование
Для установления соответствия типа использованной стали (сплава) и сварочных материалов чертежам, проекту, отраслевым стандартам и требованиям настоящего стандарта необходимо определение химического состава составляющих элементов реакционных труб и коллекторов и сварных соединений методом стилоскопирования.
При этом допускается использование стационарных и переносных стилоскопов.
Стилоскопирование металла составляющих реакционных труб (и коллекторов) и металла шва проводят с целью установления соответствия марки использованных для сварки материалов требованиям соответствующих НТД на изготовление конкретных изделий (составляющих реакционных и коллекторных труб).
Обязательному стилоскопированию следует подвергать в изготовленных реакционных трубах и коллекторах все их составляющие, находящиеся под давлением, а также соединяющие их сварные швы.
Стилоскопирование необходимо проводить на зачищенных до металлического блеска участках (площадках) поверхности, которые должны быть предварительно замаркированы для идентификации на соответствующих картах контроля.
В случае неудовлетворительных результатов проводят повторное стилоскопирование металла составляющих реакционных труб и коллекторов и металла шва в трех различных участках.
При выявлении несоответствия марки используемой стали (сплава) или сварного соединения как минимум на одной детали, проверенных не в полном объеме, стилоскопированию должны быть подвергнуты все однотипные детали, сварные соединения.
Стилоскопирование не проводят в следующих случаях:
- при невозможности осуществления контроля вследствие недоступности сварных швов;
- по предписаниям соблюдения правил техники безопасности.
6.7.4.13 Каждую партию сварочной проволоки следует проверять на стойкость против образования горячих и холодных трещин путем многослойной наплавки с изготовлением макро- и микрошлифов и сваркой контрольных стыков.
а) Испытания на сопротивляемость образованию горячих трещин
Контрольные образцы подлежат испытанию согласно ГОСТ Р ИСО 17641-1, ГОСТ Р ИСО 17641-2 и ГОСТ Р 54790.
б) Испытания на сопротивляемость образованию холодных трещин
Контрольные образцы подлежат испытанию согласно ГОСТ Р ИСО 17642-1, ГОСТ Р ИСО 17642-2 и ГОСТ Р 56143.
6.7.4.14 Испытание на длительную прочность
Сварные образцы должны быть испытаны на длительную прочность согласно требованиям ГОСТ 10145 с периодическим контролем - не реже одного раза в три года. Испытания следует проводить при расчетной температуре стенки свариваемых элементов, указанной в техническом проекте и соответствующей условиям развития ползучести.
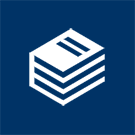