ГОСТ Р 59109-2020. Национальный стандарт Российской Федерации. Элементы реакционных трубчатых печей, работающих под давлением. Технические условия
6.2 Требования к трубам
Радиантные трубы и коллекторы радиантных труб должны быть изготовлены из центробежнолитых или деформированных труб.
6.2.1 Центробежнолитые трубы должны быть изготовлены по ТД [9], [10] (см. таблицу А.2 приложения А). При этом металл должен выплавляться в индукционных печах с основной или нейтральной футеровкой. В индукционных печах в процессе выплавки должна быть использована чистая, первородная шихта (металлическая шихта, полученная переплавом исходных материалов/руды или продуктов ее прямого восстановления/без применения стального лома), и должно быть запрещено в целях дошихтовки использование металлической стружки в любом виде (спрессованном, переплавленном и др.), а также лома металла, бывшего в эксплуатации. В целях дошихтовки [добавки недостающего количества смеси конкретных материалов (шихты) в исходный расплавленный материал до получения сплава оптимального состава с учетом данных, полученных с помощью анализа] допускается применение обрези и лома высококачественного стального проката, не бывших в эксплуатации, а также бросовых концов не бывших в эксплуатации центробежнолитых труб (от заливочной и незаливочной стороны) в объеме, не превышающем 20% от общего объема плавки. Технологию изготовления центробежнолитых труб конкретных типоразмеров (технологию выплавки и разливки конкретной марки стали и сплава, а также технологию сварки и термообработки) разрабатывает предприятие-изготовитель.
6.2.1.1 Химический состав и механические свойства металла труб должны соответствовать требованиям [9] и [10]. Зарубежные аналоги сталей и сплавов приведены в приложении Б. Право изготовления труб (и фасонных отливок) из иностранных марок сталей и сплавов по зарубежным стандартам должно быть подтверждено уполномоченными сертификационными организациями, специализирующимися на сертификации систем управления и квалификации персонала и продукции в соответствии с международными стандартами по итогам сертификационного аудита. При этом предприятие-изготовитель по итогам сертификационного аудита должно иметь сертификаты соответствия установленного образца, предоставляющие право на изготовление труб (отливок) конкретных размеров из конкретных иностранных марок сталей и сплавов в течение конкретного периода времени. Кроме того, сертифицированные изделия должны соответствовать требованиям настоящего стандарта.
6.2.1.2 Термообработка труб из сталей марок 20Х25Н20С, 45Х25Н20С, 45Х25Н20С2Б, 45Х25Н20С2, 35Х24Н24Б и сплавов марок 10Х20Н33Б, 10Х23Н34БСТЦ, 15Х25Н37Б, 45Х25Н35БС, 45Х25Н35БСТЦ, 45Х28Н49В5С, 45Х35Н46БСТЦ, 50Х25Н35С2Б, 50Х25Н35В5К15С не требуется. Термообработку труб из сталей марок 10Х18Н9, 03Х17Н14М3, 10Х18Н11Б, 20Х5М, 20ЮЧ, 20Х13 и сплавов марок 05Х20Н32Т, 10Х20Н32ТЮ, 06ХН28МДТ, 01Х15Н57В4М16К2, 05Х22Н42М2Т1Ю, 10Х20Н60Б4К1М9, 10Х20Н68Б3Г3КТ, 10Х22Н45К15М9ТЮ следует проводить по режимам, указанным в ПКД. Допускается проводить термическую обработку по режимам предприятия-изготовителя при условии обеспечения механических и специальных свойств, установленных в ТУ на изделия.
6.2.1.3 Трубы следует поставлять механически обработанными по внутреннему диаметру. По наружному диаметру трубы допускается поставлять с обработкой и без механической обработки. Размеры обработанных труб должны соответствовать требованиям чертежа.
Наружная поверхность трубных заготовок после отливки подвергается дробеструйной обработке сечкой из нержавеющей проволоки любой марки диаметром от 1,2 до 2,0 мм. Шероховатость наружной поверхности трубных заготовок при этом не должна превышать 0,8 мм.
Трубы поставляют с наружным диаметром от 85 до 328 мм и толщиной от 6 до 35 мм.
Припуск на обработку по внутренней поверхности литой заготовки - 5 мм.
Литые заготовки с наружным диаметром от 224 до 328 мм должны иметь припуск на механическую обработку по внутренней поверхности 8 мм. Столбчатость макроструктуры литых заготовок с наружным диаметром от 224 до 328 мм не регламентирована.
Допуск по внутреннему диаметру механически обработанной трубы составляет , а на расстоянии от 30 до 50 мм от концов трубы -
. Допускается расточка под углом 15° с выходом на наружный диаметр с торца.
Примечание - Допускается поставка труб размерами, выходящими за пределы указанных.
6.2.1.4 В макроструктуре трубных заготовок не должно быть трещин, спаев, шлаковых и других включений. Протяженность зоны столбчатых кристаллов в макроструктуре труб должна составлять не менее 50% от толщины стенки труб. Определение протяженности зоны столбчатых кристаллов проводят на нетравленых темплетах, выбираемых от незаливочного конца каждой трубной заготовки. Наличие шлаковых включений и скоплений пор определяется на травленых поперечных кольцевых темплетах, отбираемых от незаливочного конца последней трубной заготовки каждой плавки. Глубина пористого (дефектного) слоя на внутренней поверхности трубных заготовок не должна превышать 2/3 припуска на механическую обработку.
Примечание - Протяженность зоны столбчатых кристаллов в макроструктуре труб из сталей марок 03Х17Н14М3, 10Х18Н11Б, 20ЮЧ, 10Х18Н9, 20Х13, 20Х5М и сплава марки 06ХН28МДТ не регламентирована.
6.2.1.5 Кривизна трубных заготовок после правки на любом участке длины не должна превышать 1,0 мм на 1 пог. м, но не более 2 мм на всю длину трубной заготовки.
6.2.1.6 Разностенность труб после механической обработки по всей длине не должна превышать 1,0 мм и проверяться по торцам.
6.2.1.7 Овальность труб не должна выводить их размеры за пределы допускаемых отклонений по наружному и внутреннему диаметрам.
6.2.1.8 Наружная поверхность труб, поставляемых без механической обработки, после отливки должна быть подвергнута дробеструйной обработке сечкой из нержавеющей проволоки; шероховатость наружной поверхности при этом не должна превышать 0,8 мм.
6.2.1.9 На наружной поверхности трубных заготовок не должно быть трещин, раковин, ужимин, шлаковых включений. Выявленные при контроле наружной поверхности трубных заготовок дефекты глубиной более 0,8 мм, а также местные поверхностные выступы должны быть удалены зашлифовкой и находиться в пределах шероховатости согласно 6.2.1.8. При этом толщина стенки трубной заготовки на зашлифованных участках не должна выходить за пределы минимально допускаемых отклонений.
Зашлифованные места подвергают цветной дефектоскопии по [15]. При этом наличие индикаторных следов не допускается.
6.2.1.10 На концах труб выполняют фаски под сварку.
Нормы шероховатости контролируемой поверхности кромок под сварку должны соответствовать требованиям [15] (класс дефектности 2).
6.2.1.11 Шероховатость внутренней поверхности труб должна соответствовать Ra 5 по ГОСТ 2789. В обоснованных случаях и при согласовании с потребителем допускаются другие нормы шероховатости внутренней поверхности труб.
6.2.1.12 На внутренней поверхности труб допускаются переходы от одного диаметра к другому в виде уступа глубиной не более 0,5 мм, не выводящего размеры труб за пределы допускаемых отклонений. Для труб, предназначенных для установок производства этилена, уступы не допускаются.
6.2.1.13 На механически обработанных поверхностях труб не допускаются трещины, скопление пор, шлаковые включения и другие дефекты.
Ультразвуковой контроль металла центробежнолитой трубы из аустенитных сталей и сплавов не регламентирован.
Крупнозернистая столбчатая структура центробежнолитых труб из аустенитных сталей и сплавов делает их очень трудными (и подчас невозможными) для контроля ультразвуковым методом, т.к. указанная структура рассеивает ультразвуковую энергию и отклоняет волны.
По дополнительному требованию заказчика каждая труба должна быть подвергнута вихретоковому контролю (ВТК) на выявление поверхностных и сквозных дефектов в соответствии с требованиями инструкции предприятия-изготовителя.
6.2.1.14 Трубы после механической обработки и подготовки под сварку с обоих концов на длине 20 мм по наружной и внутренней поверхностям должны быть подвергнуты контролю методом цветной дефектоскопии по [15] (класс дефектности 2).
6.2.1.15 С целью выявления дефектов металлургического происхождения центробежнолитые трубы после отливки (до сварки в изделие) следует подвергать пневмоиспытанию давлением 0,59 Н/мм2 и гидроиспытанию давлением 19,6 Н/мм2 для труб из сталей марок 45Х25Н20С, 35Х24Н24Б и сплавов марок 20Х25Н25ТЮ, 45Х25Н35БС, 50Х25Н35В5К15С и давлением 9,8 Н/мм2 для сталей марок 20Х25Н20С, 45Х25Н20С2, 30Х23Н7С и сплавов марок 50Х20Н35С2Б, 50Х25Н35С2Б, 10Х20Н33Б, 45Х28Н49В5С, 05Х20Н32Т, 10Х20Н32ТЮ, 10Х20Н77ТЮ, 15Х25Н40М2ВТ, 10Х23Н34БСТЦ, 45Х25Н35БСТЦ, 45Х35Н46БСТЦ, но не более значения давления, при котором в трубах возникают напряжения, равные (
- предел текучести металла испытуемой трубы при комнатной температуре). Давление при пневмо- и гидроиспытании выдерживают не менее 10 мин.
6.2.1.16 После сварки труб в изделие должно быть проведено гидроиспытание на плотность и прочность пробным давлением, предусмотренным НТД на изделие.
6.2.1.17 Все стали и сплавы, из которых изготовлены центробежнолитые трубы, должны быть аттестованы на соответствие жаропрочных характеристик техническим требованиям [9] и [10], а предприятие-изготовитель должно иметь по результатам аттестационных испытаний разрешение гарантировать значения длительной прочности согласно требованиям [9] и [10].
6.2.2 Деформированные трубы должны быть изготовлены по [11] (см. таблицу А.3 приложения А).
6.2.2.1 Поставка трубной заготовки должна быть осуществлена по [12]. Трубы поставляют по наружному диаметру и толщине стенки. По требованию заказчика холодно- и теплодеформированные трубы могут поставляться по внутреннему диаметру и толщине стенки. Трубы поставляются с наружным диаметром от 20 до 89 мм включительно. Размеры горячедеформированных труб соответствуют приведенным в ГОСТ 9940, размеры холоднодеформированных труб - ГОСТ 9941 и определяются специализацией трубных станов и прессов. По соглашению между изготовителем и заказчиком допускается поставка труб диаметром, превышающим указанный интервал.
6.2.2.2 Сортамент (диаметр, длина, предельные отклонения по размерам) труб должны соответствовать ГОСТ 9940 и ГОСТ 9941. Трубы поставляют немерной, кратной и мерной длины. Длина горячедеформированных труб - согласно ГОСТ 9940, но не более 6,0 м, холоднодеформированных - по ГОСТ 9941. В каждой партии труб кратной и мерной длины допускаются 20% труб немерной длины. По соглашению между изготовителем и заказчиком допускается поставка труб мерной длины, превышающей указанную.
6.2.2.3 Овальность и разностенность труб не должны выводить их размеры за предельные отклонения соответственно по наружному диаметру и толщине стенки.
6.2.2.4 Кривизна горячедеформированных труб должна соответствовать требованиям ГОСТ 9940. Кривизна холоднодеформированных труб должна соответствовать требованиям ГОСТ 9941.
6.2.2.5 Качество наружной и внутренней поверхности труб должно соответствовать требованиям ГОСТ 9940 и ГОСТ 9941.
6.2.2.6 Поставка труб должна быть осуществлена с очищенной от окалины поверхностью.
6.2.2.7 Концы труб должны быть обрезаны под прямым углом и зачищены от заусенцев. Допускается обрезка концов труб автогенной, плазменной резкой или пилой горячей резки с последующей зачисткой концов труб от наплывов и заусенцев. При автогенной и плазменной резке припуск по длине трубы должен быть не менее 20 мм на каждый рез. Массу труб при поставке определяют без учета припусков.
6.2.2.8 По соглашению между изготовителем и заказчиком на концах труб, подлежащих сварке, должны быть сняты фаски под углом от 35° до 40° к торцу трубы с торцевым кольцом шириной от 1 до 3 мм.
6.2.2.9 В зависимости от заказа поставка труб может быть следующей: с травленой наружной и внутренней поверхностью; со шлифованной или электрополированной наружной поверхностью и травленой внутренней поверхностью; наружной и внутренней поверхностью после безокислительного отжига; электрополированной наружной и после безокислительного отжига внутренней поверхностью.
6.2.2.10 Трубы в состоянии поставки должны соответствовать требованиям [11].
6.2.2.11 Трубы допускается поставлять с проведением обязательных и дополнительных испытаний. Виды испытаний приведены в таблице 4.
Таблица 4
Виды испытаний
Характеристика испытаний | Вид испытания |
Обязательные испытания | Контроль размеров |
Контроль кривизны | |
Химический состав металла труб | |
Испытание на растяжение при комнатной температуре | |
Визуальный контроль качества поверхности | |
Испытание гидравлическим давлением | |
Ультразвуковой дефектоскопический контроль на выявление продольных дефектов всех видов труб | |
Контроль макроструктуры | |
Контроль загрязненности неметаллическими включениями | |
Контроль микроструктуры | |
Технологические испытания: сплющивание, раздача, загиб | |
Дополнительные испытания | Контроль химического состава труб |
Испытание на растяжение при повышенной температуре с определением | |
Испытание на длительную прочность (периодический контроль) | |
Испытание на растяжение при повышенной температуре с определением | |
Визуальный контроль качества поверхности по более жестким нормам | |
Ультразвуковой дефектоскопический контроль на выявление дефектов типа "расслоение" | |
Ультразвуковой дефектоскопический контроль на выявление поперечных дефектов | |
Ультразвуковой дефектоскопический контроль на выявление продольных дефектов по более жестким нормам | |
Электромагнитный (магнитный, вихретоковый и др.) контроль на выявление поверхностных и сквозных дефектов | |
Измерение толщины стенки труб с помощью ультразвукового толщиномера |
6.2.2.12 Трубная заготовка
Трубы изготовляют из катаной, кованой, ободранной или обточенной, сверленой трубной заготовки из аустенитных сплавов (05Х20Н32Т, 10Х20Н32ТЮ, 05Х22Н42М2Т1Ю, 10Х20Н60Б4К1М9, 01Х15Н57В4М16К2, 20Х25Н20С), выплавляемых в индукционных, электрических печах с применением (или без) обработки жидким синтетическим шлаком в ковше, электрошлакового переплава и прямого восстановления. Горячепрессованные трубы допускается изготовлять из кованой заготовки, поставляемой по ТД [12], и центробежнолитой, поставляемой по ТД [9].
6.2.2.13 Трубы должны поставлять в термически обработанном состоянии по режимам согласно требованиям ТД [11].
6.2.2.14 Механические свойства труб при комнатной температуре в состоянии поставки должны соответствовать требованиям ТД [11].
6.2.2.15 Пределы текучести при повышенных температурах и длительной прочности металла труб должны соответствовать требованиям ТД [11] (см. таблицу 4).
Изготовитель гарантирует соответствие пределов текучести при повышенных температурах и длительной прочности металла труб указанным требованиям без проведения испытаний. Данные гарантии должны быть подтверждены регулярными аттестационными испытаниями.
По требованию заказчика трубы поставляют с определением предела текучести при одной или нескольких температурах.
6.2.2.16 Периодически, не реже чем один раз в три года, проводят контрольную проверку соблюдения технологии изготовления труб и контрольные испытания пределов текучести при повышенных температурах и длительной прочности металла труб.
Контрольные испытания проводит специализированная организация. При положительных результатах контроля специализированная организация подтверждает изготовителю правомочность гарантировать значения пределов текучести при повышенных температурах и длительной прочности металла труб на срок не более трех лет.
6.2.2.17 Качество поверхности
На наружной и внутренней поверхностях труб не должно быть плен, трещин, закатов, рванин, глубоких рисок и грубой рябизны. Допускается удаление дефектов путем местной зачистки или сплошной шлифовки при условии, что величина шлифовки не выводит диаметр и толщину стенки за минусовые предельные отклонения, а местной зачистки - толщину стенки за минусовые предельные отклонения.
На наружной поверхности труб не допускаются цвета побежалости.
На внутренней поверхности труб допускаются мелкие поверхностные дефекты, обусловленные способом производства: шероховатость, рябизна, риски, пологие вмятины, царапины, цвета побежалости, - при условии, что они не выводят толщину стенки за минусовые предельные отклонения и соответствуют нормам ультразвукового контроля.
Наружная и внутренняя поверхности труб должны соответствовать требованиям ГОСТ 9941.
Примечание - При определении терминов следует руководствоваться положениями ГОСТ 21014.
На наружной и внутренней поверхностях труб допускаются без зачистки вмятины от окалины или прокатного инструмента, продольные риски (без острых углов), мелкая рябизна и другие мелкие дефекты, обусловленные способом производства, глубиной не более 10% от номинальной толщины стенки, но не более 2 мм для горячедеформированных труб и 0,2 мм для холодно- и теплодеформированных труб при отношении D/S > 5 и 0,6 мм для холодно- и теплодеформированных труб при отношении D/S < 5 при условии, что они не выводят толщину стенки за минусовые допустимые значения.
По требованию заказчика горячедеформированные трубы диаметром не более 89 мм, а также горячепрессованные трубы поставляют по более жестким требованиям к качеству поверхности.
На наружной и внутренней поверхностях допускаются без зачистки дефекты, перечисленные в настоящем подпункте, глубиной не более 5% от номинальной толщины стенки, но не более 1 мм.
6.2.2.18 Сплошность металла
Каждая труба должна выдерживать без обнаружения течи испытание внутренним гидравлическим давлением P, Н/мм2, значение которого вычисляют по следующим формулам:
при S/D <= 0,13 , (1)
при S/D > 0,13 , (2)
где Sm - минимальная толщина стенки с учетом минусового предельного отклонения, мм;
R - допускаемое напряжение, Н/мм2, равное 80% предела текучести для данной марки сплава;
D - номинальный наружный диаметр трубы, мм;
S - номинальная толщина стенки, мм.
Изготовитель гарантирует, что поставляемые им трубы выдержат пробное гидравлическое давление, вычисленное по указанным формулам, без проведения испытаний при условии 100%-ной ультразвуковой дефектоскопии (УЗД) труб.
Каждая труба должна быть подвергнута ультразвуковому контролю сплошности металла - УЗД в соответствии с требованиями инструкции предприятия-изготовителя на выявление продольных дефектов для горячепрессованных труб, изготовленных из непрерывно литой заготовки на обнаружение дефектов типа "расслоение".
По дополнительному требованию заказчика и по соглашению с предприятием-изготовителем каждая труба должна быть подвергнута УЗД на выявление поперечных дефектов и дефектов типа "расслоение" в соответствии с требованиями инструкции предприятия-изготовителя.
По дополнительному требованию заказчика и по соглашению с предприятием-изготовителем каждая труба с отношением D/S > 5 должна быть подвергнута УЗД на выявление продольных и поперечных дефектов по более жестким нормам в соответствии с требованиями инструкции предприятия-изготовителя.
По дополнительному требованию заказчика каждая труба должна быть подвергнута магнитному контролю (МК) или ВТК на выявление поверхностных и сквозных дефектов в соответствии с требованиями инструкции предприятия-изготовителя.
6.2.2.19 Макро- и микроструктура
В макроструктуре металла труб не должно быть трещин, расслоений и флокенов, инородных металлических и неметаллических шлаковых включений, видимых без применения увеличительных приборов.
Макроструктуру контролируют в трубах с толщиной стенки 12 мм и более.
Изготовитель гарантирует соответствие макроструктуры металла труб указанным требованиям без проведения контроля при условии проведения 100%-ной УЗД труб.
Загрязненность металла труб неметаллическими включениями (в соответствии с нормами, установленными для металла заготовки) не должна превышать значений, приведенных в таблице 5.
Таблица 5
Загрязненность металла труб неметаллическими включениями
Неметаллическое включение | Загрязненность | |
по среднему баллу | по максимальному баллу | |
Сульфиды (С) | 3,5 | 4,0 |
Оксиды и силикаты (ОС, ОТ, СХ, СП) | 3,5 | 4,5 |
Загрязненность металла труб неметаллическими включениями принимают по сертификату на трубную заготовку.
Изготовитель гарантирует соответствие загрязненности металла труб неметаллическими включениями указанным требованиям без проведения испытаний.
Величина зерна металла труб из сплавов 05Х20Н32Т и 10Х20Н32ТЮ наружным диаметром 25 мм и более в состоянии поставки должна быть не крупнее 3 - 7 номера (факультативно на первых двух партиях и при необходимости уточняется по результатам изготовления опытных партий). Для металла труб из сплавов 05Х22Н42М2Т1Ю, 10Х20Н60Б4К1М9 и 01Х15Н57В4М16К2 нормы по величине зерна не устанавливают. Нормы по величине зерна металла труб диаметром менее 25 мм согласовывают дополнительно.
6.2.2.20 Технологические свойства
Трубы должны выдерживать одно или несколько технологических испытаний диаметром:
- не более 60 мм включительно - на загиб вокруг оправки или на раздачу;
- более 60 до 89 мм включительно, с толщиной стенки не более 4,2 мм включительно - на раздачу или на сплющивание.
Испытания труб на загиб вокруг оправки и на загиб полосы проводят до угла 90°.
Испытания на раздачу проводят оправкой с углом конусности 30° до увеличения наружного диаметра труб на 20%.
Трубы с наружным диаметром от 60 до 89 мм с толщиной стенки не более 15% от наружного диаметра должны выдерживать испытание на сплющивание до получения между сплющивающими поверхностями расстояния H, мм, вычисляемого по формуле
, (3)
где a - коэффициент деформации (a = 0,09);
S - номинальная толщина стенки, мм;
D - номинальный наружный диаметр трубы, мм.
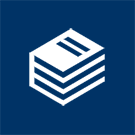