ГОСТ 24788-2018. Межгосударственный стандарт. Посуда хозяйственная стальная эмалированная. Общие технические условия
6 Методы контроля
6.1 Внешний вид, качество сборки, дефекты эмалевого покрытия и декоративной отделки проверяют визуально при естественном или комбинированном освещении. Осмотр проводят на расстоянии от 300 до 400 мм.
6.2 Размеры посуды проверяют универсальным измерительным инструментом по ГОСТ 166, ГОСТ 427 или шаблонами.
6.3 Вместимость посуды проверяют, наливая воду из мерной посуды по ГОСТ 1770, до переливания через сливное устройство или через борт.
6.4 Легкость вращения подвижных ручек, легкость поворота и прилегания крышек к борту корпусов, плотность прилегания ободков к бортам посуды проверяют опробованием, при этом не допускается смещение ободка с места установки.
6.5 Толщину эмалевого покрытия измеряют на плоских участках изделий магнитными или электромагнитными толщиномерами, обладающими погрешностью не более 10%.
6.6 Контроль ДКМ вредных веществ и органолептических свойств на соответствие требованиям национальных органов здравоохранения проводят по методикам, утвержденным этими органами <*>. Для контроля ДКМ в качестве модельной среды используют дистиллированную воду. Объем дистиллированной воды должен составлять 2/3 вместимости испытуемого изделия. Воду в посуде, предназначенной для тепловой обработки, кипятят в течение 30 мин, а для приготовления холодных блюд - выдерживают в течение 3 сут при комнатной температуре.
--------------------------------
<*> В Российской Федерации действует Инструкция от 2 февраля 1971 г. N 880-71 "Инструкция по санитарно-химическому исследованию изделий, изготовленных из полимерных и других синтетических материалов, предназначенных для контакта с пищевыми продуктами".
6.7 Коррозионную стойкость эмалевого покрытия на внутренней поверхности посуды определяют кипячением в растворе уксусной кислоты массовой доли 4,0% одним из двух методов.
6.7.1 Метод 1
Стальную пластину толщиной 0,5 мм размером 100 x 100 мм или круглую диаметром 90 мм покрывают грунтовой и испытуемой покровной эмалью по той же технологии, что и посуду. Затем испытуемую пластину, обезжиренную органическим растворителем или теплой водой с мылом, промытую дистиллированной водой, высушенную при температуре (110 +/- 10) °C в течение 2 ч в сушильном шкафу и охлажденную в эксикаторе в течение 2 ч, взвешивают на аналитических весах с погрешностью, не превышающей 0,2 мг, и закрепляют в установке для определения коррозионной стойкости (рисунок 1).
1 - испытуемый образец; 2 - кварцевый патрубок;
3 - гайка-барашек М6 по ГОСТ 3032; 4 - холодильник
типа ХШ по ГОСТ 25336; 5 - уплотнение; 6 - основание
Рисунок 1 - Установка для определения коррозионной стойкости
Крышка и основание установки должны быть изготовлены из стали марки Х18Н9Т по ГОСТ 5632, все уплотнения - из резины марки ТМКЩ по ГОСТ 7338.
Установку с пластиной нагревают в сушильном шкафу при температуре (110 +/- 10) °C в течение 30 мин, затем в нее наливают на 2/3 высоты стакана из кварцевого стекла кипящий раствор уксусной кислоты массовой доли 4,0%, после чего устанавливают на предварительно нагретую электрическую плитку, мощность которой должна быть такой, чтобы закипание раствора в установке начиналось через 8 - 10 мин. Раствор должен нагреваться и кипеть в установке в течение 1 ч с момента вливания раствора.
Далее раствор из установки сливают, пластину с испытуемым эмалевым покрытием извлекают, промывают дистиллированной водой, высушивают при температуре (110 +/- 10) °C в течение 2 ч и после охлаждения в эксикаторе в течение 2 ч взвешивают.
Коррозионную стойкость X, мг/см2·ч, вычисляют по формуле
,
где - потеря массы образца, мг;
S - площадь испытуемой поверхности образца, см2;
- продолжительность испытания, ч.
6.7.2 Метод 2
Внутреннюю поверхность испытуемых изделий промывают органическим растворителем или теплой водой с мылом, ополаскивают дистиллированной водой и высушивают.
В изделие вливают нагретый до кипения раствор уксусной кислоты массовой доли 4,0% из расчета 1,6 см3 на 1 см2 испытуемой поверхности. Уровень раствора фиксируют.
Изделие без крышки устанавливают на предварительно нагретую (время нагрева не менее 30 мин) электрическую плитку с закрытыми нагревателями номинальной мощностью 800 Вт, доводят раствор до кипения и регулируют мощность конфорок таким образом, чтобы слабое кипение продолжалось в течение 1 ч с момента вливания раствора в изделие. По мере выкипания раствора его уровень поддерживают постоянным, доливая нагретый до кипения раствор уксусной кислоты.
После кипячения раствор переливают из изделия в лабораторный стакан для охлаждения, внутреннюю поверхность изделия ополаскивают небольшим количеством дистиллированной воды, которую переливают в тот же стакан. Охлажденный до комнатной температуры раствор переливают в мерный сосуд, доводят его объем до определенного округленного значения, доливая дистиллированную воду.
Из мерного сосуда отбирают аликвотную часть находящегося в нем раствора объемом 200 см3 и выпаривают в фарфоровой чашке, не допуская разбрызгивания раствора. Полученный остаток высушивают до постоянной массы m при температуре (110 +/- 10) °C.
Коррозионную стойкость X1, мг/см2·ч, вычисляют по формуле
,
где m - масса высушенного остатка, мг;
V - объем раствора уксусной кислоты и промывной воды, доведенный до округленного значения, см3;
200 - объем выпариваемой части раствора, см3.
6.8 Коррозионную стойкость наружного эмалевого покрытия определяют нанесением на плоские участки поверхности посуды нескольких капель раствора уксусной кислоты массовой доли 4,0% при температуре (20 +/- 2) °C.
Испытуемая поверхность посуды должна быть без дефектов.
Испытания проводят на трех различных участках.
Испытуемые участки протирают ватным тампоном, смоченным этиловым спиртом по нормативным документам государств, проголосовавших за принятие настоящего стандарта <*> после испарения спирта эти участки обводят восковым карандашом и смачивают (0,4 +/- 0,1) см3 раствора уксусной кислоты массовой доли 4,0%. После воздействия кислоты в течение (60 +/- 5) с посуду тщательно промывают водой и просушивают салфеткой.
--------------------------------
<*> В Российской Федерации действует ГОСТ Р 51723-2001 "Спирт этиловый питьевой 95%-ный. Технические условия".
Результаты оценивают немедленно после испытания.
Эмалированную поверхность осматривают на расстоянии от 250 до 300 мм без применения увеличительных приборов.
6.9 Испытание коррозионной стойкости эмалевого покрытия кипячением в растворе лимонной кислоты массовой доли 6,0% проводят по ГОСТ 29020.
6.10 Испытания коррозионной стойкости наружного эмалевого покрытия при комнатной температуре в лимонной кислоте концентрации 100 г/дм3 проводят по ГОСТ 29021.
6.11 Испытание коррозионной стойкости эмалевого покрытия в кипящей воде и водяном паре - по ГОСТ 29022.
6.12 Испытание ударной прочности эмалевого покрытия проводят на плоских участках внутренней или наружной поверхности посуды воздействием свободно падающего с определенной высоты ударника массой 0,2 кг со сферической рабочей поверхностью диаметром 25,4 мм на установке (рисунок 2).
1 - направляющая труба; 2 - ударник; 3 - фиксатор;
4 - кронштейн; 5 - стопор трубы; 6 - основание;
7 - стопор кольца; 8 - кольцо (комплект)
Рисунок 2 - Установка для определения ударной прочности
Перед испытанием изделие устанавливают на сменное кольцо, соответствующее высоте предмета посуды.
В зависимости от заданной работы удара ударник устанавливают фиксатором на определенную высоту. Ударник сбрасывают на испытуемую поверхность поворотом рукоятки фиксатора.
Испытание проводят не менее чем в трех различных точках поверхности посуды, расстояния между которыми должны быть не менее 40 мм. На посуде с диаметром дна до 100 мм включительно или с рельефной формовкой дна допускается проводить испытания в одной точке поверхности. Во время испытаний изделие следует придерживать на кольце.
После испытаний проводят визуальный осмотр поверхности изделий без применения увеличительных приборов.
Допускается проводить испытания на установках другого типа, обеспечивающих необходимую точность испытаний.
6.13 Термическую стойкость эмалевого покрытия посуды, предназначенной для тепловой обработки пищи, определяют ее попеременным нагревом и охлаждением.
Для нагрева посуды используют электрическую плитку по ГОСТ 14919 с закрытыми нагревателями номинальной мощностью 800 Вт. На конфорку плитки плотно насаживают дополнительное кольцо из нержавеющей стали, диаметр которого определяется диаметром используемой конфорки.
Высота кольца должна быть выше поверхности конфорки плитки на 8 - 10 мм. На конфорку с кольцом насыпают металлическую дробь по ГОСТ 11964, или медную дробь, или порошок электротехнического периклаза по ГОСТ 13236, или песок. Размер частиц должен быть не более 0,3 мм. Посуду заполняют водой до половины вместимости, устанавливают на предварительно нагретую плитку и доводят воду до кипения.
Через 15 - 30 с интенсивного кипения воды посуду снимают с плитки, быстро выливают из нее кипящую воду и вливают равное количество воды температурой (20 +/- 1) °C.
Спустя 5 - 10 с посуду полностью заполняют холодной водой температурой (20 +/- 1) °C. После охлаждения посуды из нее удаляют воду и насухо вытирают.
Затем на дно посуды помещают кусочки фольги из олова марок 01пч или 01 по ГОСТ 860 (температура плавления 232 °C) в соответствии со схемой, приведенной на рисунке 3 (d - диаметр дна изделия).
Рисунок 3
Толщина оловянных частиц должна быть не более 0,5 мм, длина наибольшей стороны - не более 5 мм.
Для посуды с диаметром дна до 100 мм включительно допускается применять одну оловянную частицу. Изделие с частицами оловянной фольги вновь устанавливают на нагретую электрическую плитку и нагревают до расплавления первой частицы.
После этого в посуду за один прием вливают холодную воду в количестве, равном половине вместимости испытуемого предмета посуды, и снимают ее с плитки. Спустя 5 - 10 с посуду полностью заполняют водой. После охлаждения посуды из нее удаляют воду и кусочки фольги, насухо вытирают, затем на внутреннюю поверхность ватным тампоном наносят тонкий слой чернил для авторучек синего или фиолетового цвета.
После выдержки испытуемой поверхности посуды в течение 3 мин под слоем чернил ее промывают проточной водой в течение 30 с и осматривают без применения увеличительных приборов для выявления трещин и отколов.
6.14 Удержание крышек на посуде проверяют, наклоняя предмет посуды на требуемый угол.
6.15 Слив жидкости без подтеков проверяют при выливании воды из посуды, наполненной не менее чем на 1/2 вместимости. Посуду наклоняют таким образом, чтобы вода сливалась непрерывной струей.
6.16 Прочность крепления арматуры (ручек) проверяют следующим образом: посуду закрепляют или подвешивают за дужку или ручки, затем к посуде прикладывают в течение 5 мин статическую нагрузку, в два (полтора) раза превышающую массу воды, соответствующей номинальной вместимости.
6.17 Устойчивость посуды на плоскости определяют с помощью поверочной плиты по ГОСТ 10905, поверочной линейки по ГОСТ 8026, щупа по НД. Допускается использование других средств измерений.
6.18 Теплостойкость пластмассовых деталей ручек проверяют, устанавливая посуду в предварительно нагретый до температуры (150 +/- 5) °C сушильный шкаф и выдерживая ее там в течение 1 ч. Поверхность ручек после испытания посуды не должна иметь трещин, вздутий, сколов, деформации и других видимых изменений.
6.19 Пористость эмалевого покрытия проверяют, наполняя посуду водой и выдерживая ее в течение 72 ч при температуре (20 +/- 5) °C. После испытания на эмалевом покрытии не должны появляться следы коррозии.
6.20 Стойкость против адсорбции красящих веществ проверяют 10-минутным кипячением воды с добавлением чая (15 г на 1 дм3 воды), налитой до половины вместимости посуды, устанавливая ее на предварительно нагретую электрическую плитку. После ополаскивания посуды теплой водой и обтирания ее салфеткой или бумажным фильтром эмалевое покрытие не должно иметь видимого изменения цвета.
6.21 Качество защитных покрытий ручек проверяют по ГОСТ 9.302.
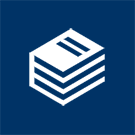