ГОСТ 31446-2017 (ISO 11960:2014). Межгосударственный стандарт. Трубы стальные обсадные и насосно-компрессорные для нефтяной и газовой промышленности. Общие технические условия
10.6. Контроль твердости
10.6.1 Требования PSL-3
Дополнительные требования PSL-3 для групп прочности N80 тип Q, R95 и P110 приведены в приложении E.
10.6.2 Общие положения
Периодичность контроля твердости изделий приведена в таблице C.46. Если для партии или плавки требуется проведение не одного испытания, образцы для испытаний должны быть отобраны от разных изделий.
Дополнительные контроль твердости наружной поверхности и контроль твердости по толщине стенки тела и высаженных концов труб могут быть проведены по согласованию между заказчиком и изготовителем. Процедура проведения дополнительного контроля твердости должна быть согласована между заказчиком и изготовителем.
Допускается не подвергать контролю короткие трубы, муфтовые заготовки и заготовки для соединительных деталей групп прочности M65, L80, C90, T95, C110, Q125 и Q135, изготовленные из подвергаемых контролю труб, трубных заготовок для муфт и заготовок для соединительных деталей, не подвергавшихся после контроля термообработке.
10.6.3 Периодичность контроля изделий групп прочности M65 и L80
Контроль твердости по толщине стенки для плавки проводят с той же периодичностью, что и испытания на растяжение для плавки.
Контроль твердости для плавки, проведенный на образцах от изделий, может считаться контролем для партии изделий.
10.6.4 Периодичность контроля изделий групп прочности M65 и L80
Контроль твердости труб, муфтовых заготовок, трубных заготовок для муфт и заготовок для соединительных деталей проводят с той же периодичностью, что и испытания этих изделий на растяжение.
Дополнительные требования PSL-3 приведены в приложении E.
10.6.5 Периодичность контроля и отбор образцов для контроля труб с невысаженными концами группы прочности C90, T95 и C110
Контроль твердости по толщине стенки труб с невысаженными концами проводят:
a) для групп прочности C90 и T95 - в одном квадранте одного кольцевого образца, отобранного от одного из концов каждой трубы партии. Отбирают приблизительно по 50% образцов от передних и задних концов труб;
b) для группы прочности C110 - в одном квадранте одного кольцевого образца, отобранного от каждого из концов каждой трубы партии. Если изготовитель применяет план контроля процесса и может подтвердить, что этот контроль является достаточным для обеспечения равномерной твердости труб по всей длине, периодичность испытаний может быть уменьшена до периодичности, указанной в перечислении a).
Дополнительные требования PSL-3 приведены в приложении E.
10.6.6 Периодичность контроля и отбор образцов для контроля труб с высаженными концами групп прочности C90, T95 и C110
Контроль твердости по толщине стенки тела труб проводят с периодичностью, указанной в 10.4.3 для испытаний на растяжение, в четырех квадрантах одного кольцевого образца. Для контроля твердости по толщине стенки высаженных концов труб отбирают одну трубу от каждых 20 труб партии. Контроль твердости по толщине стенки проводят в четырех квадрантах одного кольцевого образца, вырезанного из одного из высаженных концов отобранных труб на участке с наибольшей толщиной стенки.
Дополнительно к контролю твердости по толщине стенки должен быть проведен контроль твердости по Бринеллю или по шкале C Роквелла наружной поверхности тела и одного из высаженных концов каждой трубы.
10.6.7 Периодичность контроля и отбор образцов для контроля коротких труб, муфтовых заготовок, трубных заготовок для муфт и заготовок для соединительных деталей групп прочности C90, T95 и C110
Контроль твердости по толщине стенки толстостенных труб, используемых для изготовления нескольких муфтовых заготовок, коротких труб или соединительных деталей проводят на одном кольцевом образце, отобранном от каждого из концов этих толстостенных труб.
Контролю твердости по толщине стенки подвергают муфтовые заготовки, короткие трубы и заготовки для соединительных деталей, термообработанные в виде отдельных изделий, с наибольшей поверхностной твердостью в партии.
Контроль твердости по толщине стенки муфтовых заготовок, подвергаемых термообработке в виде отдельных изделий, проводят на одном кольцевом образце, отобранном в середине длины муфтовой заготовки, как указано на рисунке D.9. Контроль твердости по толщине стенки коротких труб и заготовок для соединительных деталей, подвергаемых термообработке в виде отдельных изделий, проводят на одном кольцевом образце, отобранном в середине длины изделия, как указано на рисунке D.9, или отобранном в середине длины образца-свидетеля, термообработанного вместе с изделиями.
Контроль твердости по толщине стенки проводят в четырех квадрантах кольцевого образца.
10.6.8 Периодичность контроля изделий группы прочности Q125 и Q135
Для контроля твердости по толщине стенки из партии труб выбирают три трубы, представляющие начало, середину и конец процесса термообработки партии. От заднего и переднего концов труб отбирают по одному образцу.
Для контроля твердости по толщине стенки коротких труб, трубных заготовок для муфт и заготовок для соединительных деталей, подвергаемых термообработке в виде труб, отбирают по одному образцу от одного из концов каждой трубы (приблизительно по 50% от передних и задних концов).
Для контроля твердости по толщине стенки коротких труб, муфтовых заготовок и заготовок для соединительных деталей, подвергаемых термообработке в виде отдельных изделий, отбирают один образец от одного из изделий партии.
Контроль твердости по толщине стенки проводят в одном квадранте кольцевого образца.
Дополнительные требования PSL-3 приведены в приложении E.
10.6.9 Образцы для контроля твердости
Образцы для контроля твердости вырезают на конце изделия, середине длины изделия или на участке, показанном на рисунке D.9. Контроль твердости по толщине стенки проводят на кольцевых образцах или сегментах, контроль поверхностной твердости - непосредственно на изделии или на образцах для испытаний на растяжение.
Контроль твердости по толщине стенки в одном квадранте проводят на кольцевом образце или одном из сегментов, на которые разрезан этот образец. Контроль твердости по толщине стенки в четырех квадрантах проводят на кольцевом образце или четырех сегментах, на которые разрезан этот образец. Контроль твердости по толщине стенки в одном или четырех квадрантах кольцевого образца проводят, как показано на рисунке D.10.
Плоскости противоположных сторон образцов должны быть параллельными и отшлифованы таким образом, чтобы их поверхность была плоской и гладкой. На поверхности образцов не должно быть окалины, посторонних веществ и следов смазочно-охлаждающих жидкостей.
10.6.10 Метод контроля
Контроль твердости по Бринеллю проводят по [18] или [19], контроль твердости по Роквеллу - по [20] или [21].
Указанные стандарты предусматривают два вида контроля твердости:
a) контроль твердости наружной поверхности, включающий один отпечаток;
b) контроль твердости по толщине стенки, включающий несколько отпечатков.
Контроль поверхностной твердости по Роквеллу или Бринеллю применяют для контроля управляемости процесса производства и подтверждения соответствия изделий требованиям настоящего стандарта.
Контроль твердости по толщине стенки по Роквеллу применяют для подтверждения соответствия изделий требованиям к максимальной твердости, разбросу значений твердости и прокаливаемости изделий. Контроль твердости по толщине стенки проводят в сечении, перпендикулярном к оси изделия. Если кольцевой образец отрезают от конца изделия, контроль твердости проводят на поверхности торца образца, противоположного торцу изделия (торцу с закаленной поверхностью). Для уменьшения погрешности измерений первый отпечаток на каждом квадранте кольцевого образца или каждом сегменте должен быть выполнен посередине стенки и не должен учитываться.
Контроль твердости изделий групп прочности M65, L80, C90, T95 и C110 следует проводить прибором, имеющим десятичную шкалу измерений (с одним или несколькими десятичными знаками).
При контроле твердости по толщине стенки тонкостенных изделий (толщиной стенки менее 7,62 мм) допускается выполнение трех отпечатков только в одном ряду посередине стенки. Разброс значений твердости в этом случае определяют между отдельными значениями твердости в этом ряду. При контроле твердости других изделий в каждом из трех рядов должно быть выполнено по три отпечатка. По трем отпечаткам в каждом ряду (вблизи наружной поверхности, посередине стенки и вблизи внутренней поверхности) определяют среднее значение твердости. Контроль твердости по толщине стенки проводят в одном или в каждом из четырех квадрантов с определением средних значений твердости для каждого ряда.
Отпечатки вблизи наружной и внутренней поверхности выполняют на расстоянии 2,5 - 3,8 мм от поверхности, при этом расстояние от поверхности до центра отпечатка должно быть не менее двух с половиной диаметров отпечатка. Расстояние от центра отпечатка до центра другого отпечатка должно быть не менее трех диаметров отпечатка. Для тонкостенных изделий допускается альтернативное расположение отпечатков.
Отклонение от параллельности сторон сегмента или кольцевого образца, контактирующих со столиком и индентором, не должно быть более 0,5°. Допускается не проводить проверку параллельности сторон при подготовке сегментов и кольцевых образцов в случае применения плоскошлифовальной машины с магнитной плитой или способа подготовки, обеспечивающего соответствие этому требованию. При применении других способов подготовки проводят проверку параллельности сторон каждого сегмента или кольцевого образца.
Шероховатость поверхности сегмента или кольцевого образца, контактирующей со столиком прибора, должна быть не хуже шероховатости, достигаемой сухим шлифованием с помощью наждачной бумаги с зернистостью не менее 240 ед.
Поверхности сегмента или кольцевого образца, контактирующие со столиком и другими элементами прибора для контроля твердости (например, индентором, держателем индентора, подставкой), должны подвергаться визуальному контролю, на них не должно быть посторонних веществ, смазки, ржавчины и заусенцев, видимых без применения увеличительных приспособлений.
Допускается свисание сегмента или кольцевого образца с опорной поверхности столика, не превышающее 40% поверхности сегмента или кольцевого образца. Допускается свисание сегмента или кольцевого образца с опорной поверхности столика, превышающее 40% поверхности в случае, если прибор предназначен для таких измерений, и имеет подтвержденную способность показывать стабильные точные результаты при таком применении. Применение внешних опор не допускается.
На поверхности столика и подставки не должно быть выступов или вмятин, которые могут отрицательно повлиять на результаты измерений твердости.
Если для поверки прибора применяют стандартные образцы, то поверку следует проводить на том же приборе, на котором после поверки будет проводиться приемочный контроль.
Для поверки применяют только калиброванные (поверенные) инденторы для прибора конкретного типа, аналогичные инденторам, применяемым для косвенной поверки. Если применяют другие инденторы, то предварительно подвергают их косвенной поверке относительно более точного индентора (контрольного индентора, имеющего меньшую погрешность). Поверхность индентора, применяемого для измерений твердости HRC, подвергают периодическому визуальному контролю на отсутствие повреждений (трещин, сколов, точечной коррозии и т.д.) при достаточном увеличении (20X и более).
Если в одном квадранте в одном ряду (вблизи наружной поверхности, посередине стенки или вблизи внутренней поверхности) хотя бы два отпечатка имеют твердость более 20 HRC, а разность наибольшего и наименьшего значений твердости в этом ряду более 2,5 HRC, то в этом ряду должны быть выполнены три дополнительных отпечатка. Среднее значение твердости в этом случае должно быть определено по трем дополнительным отпечаткам. При этом в записях по контролю твердости указывают, что были выполнены дополнительные отпечатки, а по требованию заказчика предоставляют результаты первичного контроля. Не допускается выполнять дополнительные отпечатки в том случае, если какой-либо из отпечатков имеет твердость более 27,0 HRC для групп прочности C90 и T95 и более 32,0 HRC для группы прочности C110.
Контроль твердости по толщине стенки материалов с твердостью 20 HRC и более проводят по шкале C Роквелла. Допускается проводить контроль твердости по шкале C Роквелла материалов с твердостью менее 20 HRC. Однако при оценке результатов измерений твердости менее 20 HRC по шкале C Роквелла следует учитывать, что такие измерения являются не очень точными. По выбору изготовителя или требованию заказчика, указанному в заказе, для контроля твердости материалов с твердостью менее 20 HRC применяют шкалу B Роквелла. Значения твердости по шкале C Роквелла, измеренные и переведенные, указывают в записях по контролю с округлением до первого или второго десятичного знака. Если в заказе указано требование SR15, изготовитель должен предоставить результаты контроля твердости заказчику.
Если в заказе не указано иное, то перевод значений твердости проводят по выбору изготовителя по соответствующей таблице перевода или показаниям прибора для измерений твердости.
Значения твердости по Бринеллю должны быть указаны в записях по контролю с округлением до третьего десятичного знака, условия контроля также указывают в записях, если они отличаются от следующих: испытательное усилие - 29,42 кН, диаметр наконечника - 10 мм, время приложения испытательного усилия - 10 - 15 с.
В спорных случаях должен быть проведен лабораторный контроль твердости по шкале C Роквелла.
10.6.11 Признание контроля недействительным
Если на образце до или после контроля обнаружены дефекты подготовки или несовершенства материала, не связанные с проведением контроля, он может быть забракован и заменен другим образцом от того же изделия.
10.6.12 Периодическая проверка приборов для контроля твердости
Периодическую проверку приборов для контроля твердости по Бринеллю проводят по [19] или [22], для контроля твердости по Роквеллу - по [21] или [23].
Примечание - Соответствующие разделы в [18] и [20] озаглавлены как "Процедура периодических проверок испытательных машин, проводимых пользователем", в [19] и [21] - как "Ежедневная поверка".
При проверке приборов для контроля твердости по толщине стенки изделий групп прочности M65, L80, C90, T95 и C110 разброс значений твердости применяемых стандартных образцов должен быть не более 0,4 HRC. При проверке приборов для контроля твердости изделий других групп прочности и контроля прокаливаемости разброс значений твердости применяемых стандартных образцов должен быть не более 1,0 HRC. Разброс значений твердости стандартного образца определяют как разность наибольшего и наименьшего значений твердости, указанных в паспорте стандартного образца.
Для уменьшения погрешности измерений не менее двух отпечатков на каждом стандартном образце не должны учитываться. После предварительных отпечатков на стандартном образце должно быть выполнено не менее трех отпечатков. Для контроля твердости по толщине стенки изделий групп прочности M65, L80, C90, T95 и C110 погрешность измерений не должна быть более +/- 0,5 HRC. Для контроля твердости изделий других групп прочности и контроля прокаливаемости погрешность измерений не должна быть более +/- 1,0 HRC. Погрешность измерений определяют как разность между сертифицированным средним значением твердости стандартного образца и средним значением твердости, определяемым при периодической проверке прибора.
Проверка приборов должна быть проведена в начале и конце непрерывной серии испытаний, а также, если изготовителю или заказчику (или его представителю) требуется подтверждение удовлетворительного состояния установки. В любом случае, проверку следует проводить не реже чем через каждые 8 ч непрерывной серии испытаний. Проверку приборов проводят по стандартным образцам с твердостью:
a) 20 - 27 HRC - для класса прочности 2 (кроме группы прочности C110);
b) 24 - 32 HRC - для группы прочности C110;
c) 24 - 35 HRC - для групп прочности Q125 и Q135;
d) 35 - 55 HRC - для контроля прокаливаемости.
Если результаты проверки прибора неудовлетворительны, необходимо провести косвенную проверку прибора с применением стандартных образцов по [19] или [22] при контроле твердости по Бринеллю, [21] или [23] - при контроле твердости по Роквеллу.
При возникновении разногласий для подтверждения точности и линейности характеристик прибора проводят его поверку с применением двух стандартных образцов, для групп прочности C90, T95 и C110 - стандартных образцов с твердостью 20 - 26 HRC и 30 - 46 HRC. Разброс значений твердости стандартного образца, определяемый как разность между наибольшим и наименьшим значениями твердости, указанными в паспорте стандартного образца, не должен быть более 0,4 HRC. Погрешность измерений, определяемая как разность между сертифицированным средним значением твердости стандартного образца и средним значением твердости, определяемым при периодической проверке, не должна быть более +/- 0,5 HRC.
Результаты контроля твердости, полученные при периодической проверке, должны быть зарегистрированы и проанализированы с применением общепринятых статистических методов контроля процесса, таких как X-bar (гистограммы средних значений), R-диаграммы (интервалов измерений) и обычные гистограммы.
10.6.13 Поверка (калибровка) приборов для контроля твердости и инденторов
Косвенную поверку (калибровку) приборов для контроля твердости проводят после проведения прямой поверки (калибровки) не реже одного раза в год по [22] или [19] для контроля твердости по Бринеллю, [23] или [21] - для контроля твердости по Роквеллу.
Подтверждение точности и линейности характеристик прибора при поверке (калибровке) проводят с применением двух стандартных образцов, имеющих твердость 20 - 55 HRC. Поверку приборов для приемочного контроля твердости HRC следует проводить с применением стандартных образцов с твердостью, охватывающей весь интервал измерений твердости. Разброс значений твердости стандартного образца, определяемый как разность между наибольшим и наименьшим значениями твердости, указанными в паспорте стандартного образца, не должен быть более 0,4 HRC. Погрешность измерений, определяемая как разность между сертифицированным средним значением твердости стандартного образца и средним значением твердости, определяемым при косвенной поверке (калибровке), не должна быть более +/- 0,5 HRC.
Индентор подвергают прямой поверке (калибровке) не реже одного раза в два года. Погрешность измерений индентора для контроля твердости HRC должна быть подтверждена изготовителем по более точному индентору (с меньшей погрешностью измерений) и стандартным образцам с твердостью, охватывающей весь интервал измерений твердости. Погрешность измерений индентора для контроля твердости HRC не должна быть более +/- 0,4 HRC.
Свидетельство о поверке (сертификат калибровки) прибора для контроля твердости должен быть выдан независимой организацией. Организация, которую привлекают для поверки (калибровки) приборов и инденторов для контроля твердости HRC, должна быть аккредитована по [24] или эквивалентному стандарту уполномоченным аккредитационным органом, функционирующим в соответствии с [25]. В свидетельстве о поверке (сертификате калибровки) должны быть приведены как минимум следующие сведения:
a) ссылка на стандарт [22] и (или) [19] или [23] и (или) [21];
b) метод поверки (калибровки) [прямой и (или) косвенный];
c) средства поверки (калибровки): стандартные образцы, упругие поверочные устройства и т.д.;
d) температура;
e) поверяемые шкалы твердости;
f) дата поверки (калибровки);
g) данные стандартных образцов (среднее значение твердости, шкала твердости, порядковый номер, изготовитель и разброс твердости);
h) результаты контроля;
i) идентификационные данные прибора для контроля твердости (изготовитель, номер модели и серийный номер);
j) серийный номер индентора;
k) организация, проводившая поверку (калибровку);
l) имя и фамилия представителя организации, проводившего поверку (калибровку).
10.6.14 Повторный контроль твердости изделий групп прочности M65 и L80
Если результаты контроля твердости по толщине стенки образца, представляющего партию изделий групп прочности M65 и L80, не соответствуют установленным требованиям, изготовитель может принять решение о проведении повторного контроля образцов от двух дополнительных изделий из той же партии, отобранных на том же конце изделий (переднем или заднем), что и первичный образец. Если все результаты повторного контроля удовлетворяют установленным требованиям, партия должна быть принята, за исключением изделия, не прошедшего контроль. Если при повторном контроле хотя бы один из образцов не соответствует установленным требованиям, изготовитель может подвергнуть контролю все остальные изделия партии или забраковать партию.
10.6.15 Повторный контроль твердости изделий групп прочности C90, T95 и C110, кроме коротких труб, муфтовых заготовок и заготовок для соединительных деталей, подвергаемых термообработке после разрезания на отдельные длины
Если при контроле изделия групп прочности C90 и T95 среднее значение твердости находится в интервале 25,4 - 27,0 HRC, в непосредственной близости от первичных отпечатков должны быть выполнены три дополнительных отпечатка для определения еще одного среднего значения твердости. Если новое среднее значение твердости не более 25,4 HRC, изделие должно быть принято. Если это значение более 25,4 HRC, изделие должно быть забраковано.
Если при контроле изделия группы прочности C110 среднее значение твердости находится в интервале 30,0 - 32,0 HRC, в непосредственной близости от первичных отпечатков должны быть выполнены три дополнительных отпечатка для определения еще одного среднего значения твердости. Если новое среднее значение твердости не более 30,0 HRC, изделие должно быть принято. Если это значение более 30,0 HRC, изделие должно быть забраковано.
10.6.16 Повторный контроль твердости коротких труб, муфтовых заготовок и заготовок для соединительных деталей групп прочности C90, T95 и C110, подвергаемых термообработке после разрезания на отдельные длины
Если при контроле коротких труб, муфтовых заготовок и заготовок для соединительных деталей групп прочности C90, T95 и C110, подвергаемых термообработке после разрезания на отдельные длины, результаты контроля твердости образца, представляющего партию изделий, не соответствуют установленным требованиям, партия должна быть забракована. Изготовитель должен провести повторную термообработку партии или контроль дополнительных образцов, отобранных от трех других изделий той же партии так же, как и при первичном контроле. Если результаты контроля хотя бы одного из трех дополнительных образцов окажутся неудовлетворительными, партия должна быть забракована.
10.6.17 Общие положения по повторному контролю твердости изделий групп прочности Q125 и Q135
Если разброс значений твердости на образце не соответствует требованиям, указанным в 7.8 и таблице C.5, изготовитель может удалить первичные отпечатки и провести повторный контроль. Для каждого образца допускается одно удаление отпечатков и один повторный контроль. После повторного контроля изделие, не соответствующее установленным требованиям, должно быть забраковано.
10.6.18 Повторный контроль твердости труб, трубных заготовок для муфт групп прочности Q125 и Q135
Если забраковано более одного из трех изделий, отобранных для контроля партии, изготовитель может подвергнуть контролю все остальные изделия партии. Повторный контроль изделий должен быть проведен по 10.6.16.
Если забраковано одно из трех изделий, дополнительно могут быть отобраны еще три изделия из партии. Повторный контроль изделий должен быть проведен по 10.6.16. Если какое-либо из дополнительных изделий будет забраковано, изготовитель может подвергнуть контролю все остальные изделия партии или провести повторную термообработку партии (для того чтобы принять партию изделий, пять из шести испытанных изделий должны соответствовать требованиям 7.8 и таблицы C.5).
10.6.19 Повторный контроль твердости коротких труб, муфтовых заготовок или заготовок для соединительных деталей групп прочности Q125 и Q135, подвергаемых термообработке в виде отдельных изделий
Если разброс значений твердости на образце от изделия не соответствует требованиям, указанным в 7.8 и таблице C.5, изготовитель может провести повторный контроль твердости трех других изделий из партии. Если разброс значений твердости на образце хотя бы от одного из дополнительных изделий превышает допустимый разброс значений твердости, партия должна быть забракована.
10.6.20 Повторная термообработка изделий классов прочности 2 и 4
Забракованная партия изделий может быть подвергнута повторной термообработке и контролю твердости как новая партия.
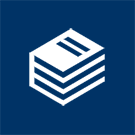