ГОСТ Р 57357-2016/EN 10080:2005. Национальный стандарт Российской Федерации. Сталь для армирования железобетонных конструкций. Технические условия
8. Оценка соответствия
8.1. Заводской производственный контроль
8.1.1 Общие положения
Арматурные стали в соответствии с настоящим стандартом должны изготовляться при постоянно действующей системе заводского контроля, которая обеспечивает один и тот же уровень достоверности соответствия готовой продукции, каким бы не был производственный процесс.
Система заводского производственного контроля должна включать в себя процедуры оценки показателей, установленных в 8.1.2 и 8.1.3.
Принимается, что изготовители, имеющие систему заводского производственного контроля, которая соответствует требованиям ЕН ИСО 9001 и ориентирована на требования настоящего стандарта, выполняют требования, предъявляемые к заводскому производственному контролю настоящим стандартом.
8.1.2 Отбор образцов и испытание готовых изделий
8.1.2.1 Определение стандартных показателей
Отбор образцов и испытание готовых изделий для определения стандартных показателей проводят в соответствии с положениями 8.1.2.1.1 - 8.1.2.1.4.
8.1.2.1.1 Стержни и мотки
Единицей испытания является плавка или часть плавки.
Испытания должны проводиться следующим образом:
- по химическому составу, один анализ на единицу испытания. Химический состав стали при анализе плавки должен определяться производителем стали;
- для испытаний на изгиб и/или отгиб, определения массы на 1 м и геометрии поверхности требуется один образец на единицу испытания для каждого номинального диаметра;
- для испытаний на растяжение требуется один образец-изделие на 30 т и не менее трех образцов на единицу испытания для каждого номинального диаметра. Результаты испытания оцениваются в соответствии с 8.1.3.
8.1.2.1.2 Размотанные изделия
Предприятие-обработчик изделий в мотках должно работать по задокументированной процедуре, обеспечивающей в последующем соответствие изделий в мотке требованиям, установленным на показатели изделия в технических условиях. Данная процедура включает в себя минимум следующее:
- визуальный контроль повреждений геометрии поверхности каждого предназначенного для дальнейшей обработки мотка;
- измерение геометрии поверхности не менее одного образца полученного размера в день;
- испытание на растяжение с периодичностью не менее одного образца от каждого типа установки (качение или вращение) в неделю, от каждого из двух обрабатываемых размеров. За период 6 мес отбор образцов должен обеспечивать охват всех установок и размеров. От каждого мотка допускается отбирать только один образец.
Испытание может проводиться либо собственными ресурсами обработчика (внутренними и внешними), либо обработчиком в кооперации с изготовителем мотка. Испытания не рассматриваются как промышленные испытания, но как основа для оценки долгосрочного уровня качества, как описано в 8.5.
8.1.2.1.3 Арматурная сетка
Испытуемая единица состоит из сеток с одинаковой комбинацией технических классов арматуры и диаметров, изготовленных на одной и той же сварочной машине, с максимальной массой 50 т.
Образцы для проверки свойств отбирают в соответствии с таблицей 9. Данные образцы могут быть отобраны по выбору изготовителя из одной или разных сеток, при условии, что испытываются разные проволоки.
Измеряются все установленные размеры арматурной сетки (длина, ширина, шаг, выступ - см. 7.3.5).
Химический состав материала (анализ плавки) определяется изготовителем стали. Изготовителю арматурной сетки должно быть предоставлено подтверждение соответствия техническим условиям, в которое при требовании заказчика должно включаться указание химического состава.
Таблица 9
План выборочного контроля арматурной сетки
Свойство | Число образцов на единицу испытания |
Re | >= 2 <a> |
Rm/Re | >= 2 <a> |
I. > Re,act/Re,nom <b> | >= 2 <a> |
Agt | >= 2 <a> |
Размеры <d> | >= 1 |
Сила сдвига | >= 2 <c> |
Масса на метр <b> | >= 2 <a> |
Гибкость <e> | >= 2 <a> |
Геометрия поверхности | >= 2 <a> |
<a> Не менее одного образца для продольного направления и поперечного направления. <b> Где важно. <c> См. 7.2.4.1. <d> Можно измерить перед сваркой. <e> Это можно оценить по составляющим проволокам испытанием на изгиб или отгиб. |
8.1.2.1.4 Пространственные каркасы
Испытуемая единица состоит из пространственных каркасов максимальной массой 50 т одинаковой комбинации технических классов и диаметров, изготовленных на одной сварочной машине.
Образцы отбирают при каждой смене размеров компонентов или применяемых технических классов стали, но не менее одного раза в день для каждой установки.
При любом сочетании номинальных диаметров высота и длина решетчатых балок не влияют на отбираемые фрагменты проб. Число фрагментов проб из поясов и диагоналей на каждую испытуемую единицу указано в таблице 10.
Все установленные размеры пространственных каркасов [длина, высота, ширина, шаг (см. 7.3.6)] должны быть измерены.
Таблица 10
План выборочного контроля пространственных каркасов
Свойство | Число образцов на единицу испытания |
Re | >= 1 <a> |
Mr/Re | >= 1 <a> |
I. > Re,act/Re,nom <b> | >= 1 <a> |
Agt | >= 1 <a> |
Размеры <c> | >= 1 |
Сила сдвига <d, e> | >= 2 |
Масса на метр <f> | >= 1 <a> |
Гибкость <g> | >= 1 |
<a> Каждый пояс и раскос. <b> Где существенно. <c> Каждый тип каркаса. <d> Каждый пояс. <e> См. 7.2.4.2. <f> Можно измерить перед сваркой. <g> Это можно оценить по составляющим проволокам, по испытанию на изгиб или повторный изгиб. |
Химический состав (анализ плавки) материала определяется производителем стали и при требовании заказчика должен быть представлен изготовителю пространственного каркаса для каждой плавки.
8.1.3 Оценка результатов испытания
8.1.3.1 Re, Agt, Rm/Re, Re,act/Re,nom
8.1.3.1.1 Cv установлен как нижний предел.
Если технические условия на изделие устанавливают Cv как нижний предел, то результаты рассматриваются как соответствующие настоящему стандарту, если:
- все индивидуальные значения больше или равны установленному характеристическому значению Cv,
- или
(8)
где a1 - установлено в техническом условии на изделие и все индивидуальные значения больше или равны
Cv - a2, (9)
где a2 - установлено в технических условиях на изделие.
8.1.3.1.2 Cv установлен как верхний предел.
Если технические условия на изделие устанавливают Cv как верхний предел, то результаты рассматриваются как соответствующие настоящему стандарту, если:
- все индивидуальные значения равны или ниже установленного характеристического значения Cv,
- или
(10)
где a3 - установлено в технических условиях на изделие, и все индивидуальные значения равны или ниже, чем
Cv + a4, (11)
где a4 - установлено в техническом условии на изделие.
8.1.3.2 Гибкость, сила сдвига, геометрия, масса на 1 м
При испытании на изгиб и/или отгиб все испытываемые образцы должны соответствовать требованиям технических условий на изделие.
При испытании на усилие сдвига сваренных или зажимных (клеммовых) соединений, все индивидуальные значения должны соответствовать требованиям технических условий на изделие.
При испытании геометрии поверхности результаты должны соответствовать требованиям технических условий на изделие.
При испытании массы на 1 м ни одно индивидуальное значение не должно выходить за установленные в 7.3.2 допуски.
8.1.3.3 Единицы испытания, которые не соответствуют установленным требованиям могут быть повторно испытаны согласно задокументированным в системе заводского производственного контроля методам.
8.1.4 Прослеживаемость
Поставленные партии должны идентифицироваться и прослеживаться по изготовителю и, если требуется, по технологическим данным. Изготовитель должен подготовить и сохранять необходимые документы и соответственно идентифицировать изделия и их документацию на поставку.
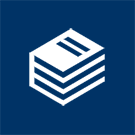