ГОСТ Р ИСО 13628-4-2016. Национальный стандарт Российской Федерации. Нефтяная и газовая промышленность. Проектирование и эксплуатация подводных эксплуатационных систем. Часть 4. Подводное устьевое оборудование и фонтанная арматура
5. Общие системные требования
5.1. Проектные и эксплуатационные требования
5.1.1 Общие положения
5.1.1.1 Характеристики продукции
Характеристики продукции (изделий) определяются изготовителем на основе анализа и испытаний, в частности:
валидационных испытаний (см. 5.1.7), которые предназначены для демонстрации и определения эксплуатационных характеристик общих серий продукции (изделий), представляющих определенные типы продукции (изделий);
требований эффективности, которые определяют рабочие характеристики конкретных изделий в состоянии на момент поставки (как предусмотрено в 5.1.1 и 5.1.2), основанные на данных FAT и соответствующих валидационных испытаний.
Требования эффективности являются специфическими и индивидуальными для изделия в состоянии на момент отгрузки. Изделия должны быть спроектированы и подвергнуты испытаниям для их применения в соответствии с 5.1, 6.1 и разделами 7 - 11.
5.1.1.2 Герметичность
Конструкции изделий должны быть способны выдерживать номинальное рабочее давление при номинальной температуре без деформаций, влияющих на соответствие любому другому требованию эффективности, при условии непревышения критериев напряженного состояния.
5.1.1.3 Теплостойкость
Конструкция изделия должна сохранять состояние функционирования в пределах диапазона температур, к которому было отнесено изделие. Компоненты должны быть аттестованы и подвергнуты испытаниям на максимальные и минимальные рабочие температуры, которым они будут подвержены в процессе эксплуатации, на определение охлаждающего эффекта Джоуля - Томпсона, на принудительный нагрев выкидных трубопроводов или на определение эффектов тепловой инертности (изоляции). При установлении требований к рабочей температуре компонентов допустимо использование термоанализа. Информация для проектирования и аттестации оборудования, работающего при повышенных температурах, приведена в ИСО 10423.
5.1.1.4 Материалы
Изделие должно быть спроектировано для приемлемого класса материала, выбранного из таблицы 1, и соответствовать требованиям ИСО 10423.
Таблица 1
Требования к материалам
Класс материала <a> | Минимальные требования к материалу | |
Корпус, крышка и фланец | Детали, регулирующие давление, штоки и держатели оправок | |
AA - общее применение | Углеродистая или низколегированная сталь | Углеродистая или низколегированная сталь |
BB - общее применение | Углеродистая или низколегированная сталь | Нержавеющая сталь |
CC - общее применение | Нержавеющая сталь | Нержавеющая сталь |
DD - исполнение для работы в присутствии сернистых соединений <a> | Углеродистая или низколегированная сталь <b> | Углеродистая или низколегированная сталь <b> |
EE - исполнение для работы в присутствии сернистых соединений <a> | Углеродистая или низколегированная сталь <b> | Нержавеющая сталь <b> |
FF - исполнение для работы в присутствии сернистых соединений <a> | Нержавеющая сталь <b> | Нержавеющая сталь <b> |
HH - исполнение для работы в присутствии сернистых соединений <a> | CRA <b>, <c>, <d> | CRA <b>, <c>, <d> |
Примечание - Информацию относительно выбора класса материала см. в 5.1.2.3. | ||
<a> Как определено в ИСО 10423; в соответствии с ИСО 15156 (все части). <b> В соответствии с ИСО 15156 (все части). <c> CRA требуется только для поверхностей, смачиваемых удерживаемым флюидом; для низколегированных и нержавеющих сталей допускается покрытие CRA. <d> Определение CRA см. в 3.1.13. Определение для CRA в ИСО 15156 (все части) не применимо.
Примечание - Для данной таблицы ANSI/NACE MR0175/ИСО 15156 эквивалентно ИСО 15156 (все части). |
5.1.1.5 Несущая способность
Конструкции изделий должны быть способны выдерживать номинальные нагрузки без деформаций, влияющие на соответствие любому другому эксплуатационному требованию, при условии непревышения критериев напряженного состояния. Конструкции изделий, удерживающих трубы, должны быть способными удерживать номинальные нагрузки без смятия труб на величину менее диаметра проходного сечения.
Проектные требования и критерии, приведенные в настоящем стандарте, основаны на номинальном рабочем давлении и внешних нагрузках, возникающих при монтаже, испытаниях и нормальной эксплуатации. Изготовителю необходимо рассмотреть дополнительные проектные требования при возникновении нагрузок, прикладываемых к буровому райзеру или райзеру для ремонта скважины, и документально оформлять общие эксплуатационные ограничения. ИСО 13628-7 определяет проектные требования к райзеру для ремонта скважины и включает дополнительные эксплуатационные условия, такие как экстремальные и случайные события (смещение судна, отключение или блокировка компенсатора перемещения). Такие условия нагружения должны быть рассмотрены при аттестации оборудования, см. 5.1.7. Потребитель должен подтвердить, что ожидаемые рабочие нагрузки находятся в пределах эксплуатационных ограничений оборудования для конкретных условий применения.
5.1.1.6 Циклы
Конструкции изделий должны отвечать функциональным требованиям и условиям работы при планируемом количестве рабочих циклов, как указано изготовителем. Изделие необходимо проектировать на требуемое количество циклов давления/температуры, на циклические внешние нагрузки и многократные свинчивания/развинчивания (закрепления/раскрепления), при соответствующих условиях и, где требуется, подтверждать соответствие валидационными испытаниями.
5.1.1.7 Рабочее усилие или крутящий момент
Изделия необходимо проектировать для работы в соответствии с техническими условиями изготовителя на рабочее усилие или крутящий момент, при соответствующих условиях и, где требуется, подтверждать соответствие валидационными испытаниями.
5.1.1.8 Накопленная энергия
Конструкция должна учитывать высвобождение накопленной энергии и обеспечивать возможность ее безопасного высвобождения до разъединения фитингов, компоновок, т.д. Характерными примерами этого являются, но не ограничиваются этим, сосуды под давлением и сжатые пружины.
5.1.2 Условия эксплуатации
5.1.2.1 Значения номинального давления
5.1.2.1.1 Общие положения
Значения номинального давления должны соответствовать 5.1.2.1.2 и 5.1.2.1.8. При прохождении трубопроводных линий малого диаметра, таких как управляющие линии SCSSV или линии нагнетания химических реагентов, через полость, такую как полость устьевой елки/трубодержателя НКТ, оборудование, граничащее с этой полостью, должно быть спроектировано на максимальное давление в любой из этих линий, если только не предусмотрены средства для контроля и сброса давления в полости в случае возникновения утечки в любой из этих линий; дополнительную информацию см. в 7.9.1 и 9.2.7. Дополнительно необходимо учитывать влияние внешних нагрузок (например, изгибающих моментов, растяжения), гидростатических нагрузок от окружающей среды и усталостных нагрузок. В контексте настоящего стандарта значения номинального давления должны интерпретироваться как значения номинального рабочего давления (3.1.41).
В конструкции уплотнений необходимо учитывать создаваемое на большой глубине обратное давление, оказывающее воздействие на уплотнение из-за наружного гидростатического давления, превышающего внутреннее давление в проходном отверстии. Необходимо учитывать все условия и этапы эксплуатации (например, ввод в эксплуатацию, испытания, пуско-наладочные работы, эксплуатацию, продувку).
5.1.2.1.2 Подводные устьевые елки
5.1.2.1.2.1 Стандартные значения номинального давления
Там, где возможно, потребитель должен указать одно из следующих стандартных значений номинального рабочего давления: 34,5 МПа (5 000 фунт/дюйм2), 69 МПа (10 000 фунт/дюйм2) или 103,5 МПа (15 000 фунт/дюйм2), в соответствии с которым необходимо спроектировать и изготовить компоновки оборудования, работающие под давлением и регулирующие давление, такие как задвижки, дроссели, корпуса устьевых оголовков и соединители. Стандартные значения номинального давления способствуют обеспечению безопасности и взаимозаменяемости оборудования, в частности там, где концевые соединения соответствуют требованиям настоящего стандарта или другим стандартам, таким как ИСО 10423. Промежуточные значения номинального давления, например 49,5 МПа (7 500 фунт/дюйм2) для деталей, работающих под давлением и регулирующих давление, не рассматриваются, за исключением трубной обвязки трубодержателей НКТ и/или проходок (пенетраций) в устьевой елке и соединений, расположенных до компонентов в скважине (таких как SCSSV, порты системы нагнетания химических реагентов, датчики), которые могут иметь более высокие проектные требования, чем проектные требования к рабочему давлению.
5.1.2.1.2.2 Нестандартные значения номинального рабочего давления
Нестандартные значения номинального давления не входят в область применения настоящего стандарта.
5.1.2.1.3 Трубодержатели скважинных трубопроводов
Стандартные значения RWP для подводных трубодержателей НКТ должны составлять 34,5 МПа (5 000 фунт/дюйм2), 69 МПа (10 000 фунт/дюйм2) и 103,5 МПа (15 000 фунт/дюйм2). Эксплуатационные или кольцевые соединения скважинных трубопроводов могут иметь RWP ниже, чем RWP для трубодержателей НКТ. Кроме того, трубодержатель НКТ может содержать проточные каналы, значения RWP которых не должны превышать 1,0 RWP компоновки трубодержателя НКТ плюс 17,2 МПа (2 500 фунт/дюйм2).
5.1.2.1.4 Оборудование подводного устьевого оголовка
Стандартные значения RWP для подводных устьевых оголовков должны составлять 34,5 МПа (5 000 фунт/дюйм2), 69 МПа (10 000 фунт/дюйм2) и 103,5 МПа (15 000 фунт/дюйм2). Для инструмента и внутренних компонентов, таких как трубодержатели обсадных колонн, допустимы другие значения номинального давления в зависимости от размера, резьбы соединения и эксплуатационных требований.
5.1.2.1.5 Донное оборудование
Стандартные значения номинального рабочего давления не применимы к донному трубодержателю обсадной колонны и наставочному оборудованию. Данное оборудование должно быть рассчитано на рабочее давление в соответствии с методами, представленными в разделе 10 и приложении E.
5.1.2.1.6 Гидравлически управляемые компоненты
Гидравлически управляемые компоненты и гидравлические управляющие линии, не подверженные воздействию скважинных флюидов, должны иметь гидравлическое RWP (проектное давление), соответствующее документально оформленным техническим условиям изготовителя. Компоненты, использующие для работы гидравлическую систему, необходимо проектировать для выполнения предусмотренных функций при 0,9 гидравлического RWP или менее, а также для возможности выдерживать случайные аномальные значения давления до 1,1 гидравлического RWP.
5.1.2.1.7 Ограничения по применению резьбы
Оборудование, проектируемое с механическими соединителями, имеющими небольшие внутренние каналы [до 25,4 мм (1,00 дюйм)], испытательные порты и измерительные присоединительные патрубки должны иметь внутреннюю резьбу, соответствовать ограничениям по применению, установленным в 7.3, и ограничениям по размерам и RWP, указанным в таблице 2. Допускается использование OEC с внутренней резьбой и удовлетворяющих требованиям 7.3, которые также спроектированы специально для применений для небольших каналов, испытательных портов или измерительных присоединительных патрубков.
Таблица 2
Номинальные значения давления для внутренних
резьбовых соединений
Тип резьбы | Размер, мм (дюйм) | Номинальное рабочее давление, МПа (фунт/дюйм2) |
Трубные изделия по стандарту API (размеры) | 12,7 (1/2) | 69,0 (10 000) |
Соединители высокого давления | Тип I, II и III по ИСО 10423 | 103,5 (15 000) |
5.1.2.1.8 Другое оборудование
Конструкции другого оборудования, такого как спуско-подъемный и испытательный инструмент, должны соответствовать техническим условиям покупателя/изготовителя.
5.1.2.2 Значения номинальной температуры
5.1.2.2.1 Стандартные значения номинальной рабочей температуры
Оборудование, входящее в область применения настоящего стандарта, должно быть спроектировано и аттестовано для работы в диапазоне температур, определенном изготовителем, и как система в целом в соответствии с ИСО 10423. Минимальным диапазоном температур для приводных механизмов задвижек и дросселей является интервал от 2 °C (35 °F) до 66 °C (151 °F). Минимальным диапазоном для проверки подводной системы, в соответствии с настоящим стандартом, должна быть классификация температуры V [от 2 °C (35 °F) до 121 °C (250 °F)]. В случае, где в качестве минимального уровня проверки для материалов, работающих под давлением и регулирующих давление, требующих ударную вязкость материалов (УТТ 3 и УТТ 3G), рекомендуется классификация температуры U [от минус 18 °C (0 °F) до 121 °C (250 °F)].
Допустимо проведение надводных (поверхностных) испытаний перед монтажом при более низких температурах окружающей среды, чем при температурах аттестации системы, указанной изготовителем. Аттестацию изделия при температуре испытаний перед монтажом проводить не требуется.
При эксплуатации оборудования необходимо учитывать переходные низкотемпературные эффекты на корпусах дросселей и сопряженных компонентах, расположенных после них, подвергаемых воздействию эффекта охлаждения Джоуля - Томпсона вследствие экстремальных перепадов давления газа.
Соответствие применяемого оборудования для работы при переходных низкотемпературных эффектах, связанных с эффектом охлаждения Джоуля - Томпсона и условиями пуска в эксплуатацию, устанавливается одним или несколькими методами:
a) валидации компонентов при требуемой минимальной температуре, как указано в 5.1.7;
b) валидации компонентов в стандартном рабочем температурном диапазоне с проверкой материала с V-образным надрезом по Шарпи при минимальной переходной рабочей или более низкой температуре в соответствии с требованиями 4.1.3;
c) валидации компонентов в стандартном рабочем температурном диапазоне при наличии документации, подтверждающей применимость материала для работы в диапазоне переходных температур.
5.1.2.2.2 Стандартные значения номинальной рабочей температуры, соответствующие условиям охлаждения морской водой
Если производитель подтвердит проведенным анализом либо испытаниями, что диапазон температур конкретного оборудования для компоновок подводного устьевого оголовка, донного подвесного оборудования и оборудования устьевой елки, например приводов задвижек и дросселей, не превышает 66 °C (150 °F) при эксплуатации под водой с удерживаемым флюидом с температурой как минимум 121 °C (250 °F), допустимо проектировать и аттестовывать оборудование для работы в диапазоне температур от 2 °C (35 °F) до 66 °C (150 °F).
С другой стороны, применение подводных компонентов и оборудования, которые термически защищены от морской воды, благодаря применению изоляционных материалов, должно продемонстрировать сохранение работоспособного состояния в пределах диапазона температур применяемой классификации температур.
5.1.2.2.3 Учет температуры при проектировании
При проектировании необходимо учитывать влияние температурных градиентов и циклов на металлические и неметаллические детали оборудования.
5.1.2.2.4 Учет температуры хранения/испытаний
При хранении и испытании подводного оборудования на поверхности при температурах, выходящих за пределы номинальных значений температуры, необходимо обратиться к изготовителю для уточнения наличия специальных рекомендованных процедур испытаний для периода хранения или процедур надводных (поверхностных) испытаний. Изготовитель должен документально оформить подобные рекомендованные процедуры испытаний для периода хранения или поверхностных испытаний.
5.1.2.3 Определение классов материалов
5.1.2.3.1 Общие положения
Оборудование должно быть изготовлено из материалов (металлических или неметаллических), отвечающих требованиям классификации материалов, в соответствии с таблицей 1. Таблица 1 не определяет все факторы окружающей среды на устье скважины, а представляет классы материалов для различных уровней условий эксплуатации и относительной коррозионной активности.
5.1.2.3.2 Классы материалов
Выбор материалов является ответственностью покупателя, так как он обладает информацией по условиям эксплуатации, а также контролирует нагнетаемые химические реагенты. Покупатель может предоставить изготовителю уточненную информацию об условиях эксплуатации и нагнетаемых химических реагентах с целью выбора производителем материалов с последующей проверкой и утверждением рекомендуемых к применению материалов.
Требования к материалам должны соответствовать таблице 1. Компоненты, работающие под давлением, должны интерпретироваться как "корпуса" при определении требований к материалу из таблицы 1. В настоящем стандарте другое оборудование прохода границ ствола скважины, такое как смазочные и отводные фитинги, должно интерпретироваться как "штоки", как представлено в таблице 1. Металлические уплотнения должны интерпретироваться как детали, регулирующие давление в соответствии с таблицей 1.
Детали, работающие под давлением и подверженные воздействию скважинных флюидов, должны соответствовать классам материалов AA - HH в соответствии с ИСО 15156 (все части) и таблицей 1.
5.1.3 Методы и критерии проектирования
5.1.3.1 Общие положения
В настоящем стандарте дается оценка конструкционной прочности и усталостной прочности. При расчете на усталостную прочность допустимо использование ASME BPVC (раздел VIII, подраздел 2, приложение 5) или другие общепринятые стандарты. Локальные значения напряжения смятия не входят в область применения настоящего стандарта. Влияния на компоновку или компоненты внешних нагрузок (например, изгибающего момента, растяжения, т.д.) подробно не рассматриваются в настоящем стандарте или ИСО 10423. При определении конструкционной прочности оборудования, входящего в область применения настоящего стандарта и подверженного воздействию внешних нагрузок, допустимо использование ИСО 13628-7.
Потребитель должен подтвердить соответствие ожидаемых рабочих нагрузок эксплуатационным ограничениям оборудования для конкретных условий применения.
5.1.3.2 Фланцы, стыковочные втулки и резьбовое оборудование по стандартам ИСО
Фланцы и стыковочные втулки для подводного использования должны быть спроектированы в соответствии с требованиями 7.1, 7.2 и/или 7.3.
5.1.3.3 Компоненты, регулирующие давление
Трубодержатели обсадных колонн и скважинных трубопроводов, а также компоненты, регулирующие давление, за исключением устьевого донного подвесного оборудования, следует проектировать в соответствии с ИСО 10423.
Компоненты, регулирующие давление, для донного подвесного оборудования должны быть спроектированы в соответствии с разделом 10.
5.1.3.4 Компоненты, работающие под давлением
Устьевые оголовки, корпуса, крышки, штоки и другие компоненты, работающие под давлением, должны быть спроектированы в соответствии с ИСО 10423.
5.1.3.5 Запорные и критические болтовые крепления
Запорные болтовые крепления (работающие под давлением) и критические болтовые крепления (несущие высокую нагрузку) требуют предварительного нагружения практически до предела текучести материала, как указано ниже.
Запорные болтовые крепления 6BX и 17SS фланцев должны быть выполнены с использованием метода, позволяющего создавать напряжения в диапазоне от 67% до 73% предела текучести материала болтов.
Данный диапазон напряжений необходим для создания предварительной нагрузки, величина которой превышает усилие разделения при давлении испытаний, но создаваемое при этом напряжение не превышает 83% от значения предела текучести материала болтов.
Для запорного болтового крепления, изготавливаемого из углеродистой или легированной стали для использования в подводных условиях, величина твердости примененного материала должна быть ограничена максимальным значением 321 HBN (Роквелл "C" 35) из-за возможности возникновения водородного охрупчивания при применении катодной защиты. Запорное болтовое крепление для классов материала AA - HH, покрываемое изоляцией, должно быть обработано согласно ИСО 15156 (все части) как болтовое крепление, подвергаемое воздействию.
Максимально допустимое напряжение растяжения для запорного болтового крепления необходимо определять с учетом условий первоначального напряжения крепления, номинального рабочего давления и условий испытаний гидростатическим давлением. Напряжения в болтах, определяемые на основании площади поперечного сечения резьбы, не должны превышать ограничения, установленные в ИСО 10423.
5.1.3.6 Первичные конструктивные компоненты
Первичные конструктивные компоненты, такие как донные направляющие плиты, следует проектировать в соответствии с общепризнанными отраслевыми технологиями и документально оформлять в соответствии с 5.1.5. При проектных расчетах должен использоваться расчетный/проектный коэффициент безопасности не менее 1,5, основанный на минимальном пределе текучести материала; также следует использовать требования других отраслевых стандартов. Многие требования включают в себя коэффициенты безопасности. Допустимо использование FEA для подтверждения отсутствия деформаций, вызываемых прикладываемыми нагрузками и приводящих к нарушению каких-либо эксплуатационных требований. В качестве альтернативы для анализа проекта допустимо использование проектных валидационных испытаний под нагрузкой, равной 1,5 номинальной несущей способности. Компонент должен выдерживать испытательное нагружение без деформаций, приводящих к нарушению каких-либо других эксплуатационных требований, при этом необходимо сохранять отчеты испытаний.
Для других условий нагружения применять расчетные коэффициенты (коэффициенты безопасности), приведенные в ИСО 13628-7.
5.1.3.7 Специальное оборудование
См. ИСО 10423. Кроме того, дополнительные требования к проектированию оборудования см. в разделах 6 - 11. В случае отличия специальных проектных требований разделов 6 - 11 от общих требований раздела 5 преимущество имеют специальные проектные требования.
5.1.3.8 Конструкции подъемного оборудования
5.1.3.8.1 Общие положения
В зависимости от конструкции и проводимых испытаний подъемное оборудование подразделяется на две категории: стационарное (постоянно установленное) подъемное оборудование и подъемное оборудование многократного применения. К испытаниям подъемного оборудования многократного применения предъявляют более жесткие требования, вследствие многократных циклов использования данного оборудования в течение срока службы. В приложении K приведено руководство по проектированию, испытаниям и техническому обслуживанию как для многократно применяемого, так и для стационарного подъемного оборудования.
Оборудование, используемое только для спуско-подъемных операций в скважину, на скважину или из скважины, должно быть спроектировано в соответствии с требованиями 5.1.3.6 или 5.1.3.7, приложения H или приложения K, в зависимости от применения.
5.1.3.8.2 Проушины
Проушины необходимо проектировать в соответствии с приложением K. Грузоподъемность на проушинах должна быть промаркирована, как указано в 5.5.2.
5.1.3.8.3 Основные элементы
Части конструкции, испытывающие нагрузки при подъеме, являются основными элементами конструкции. Грузоподъемность основных элементов, работающих под давлением или регулирующих давление, а также спроектированных таким образом, что в процессе спуско-подъемных операций они находятся под давлением, должна учитывать дополнительные напряжения, возникающие при воздействии внутреннего номинального рабочего давления.
5.1.3.8.4 Испытания нагрузкой
Испытания нагрузкой подъемных проушин следует выполнять в соответствии с приложением K.
5.1.4 Прочая проектная информация
5.1.4.1 Дробные и десятичные эквиваленты
В ИСО 10423 (приложение B) приведены эквивалентные дробные и десятичные значения.
5.1.4.2 Допуски
Следует применять следующие допуски, если иное не указано в соответствующих таблицах или на рисунках настоящего стандарта:
a) допуск для размеров формата "X" составляет +/- 0,5 мм ("X,X" составляет +/- 0,02 дюйма);
b) допуск для размеров формата "X,X" составляет +/- 0,5 мм ("X,XX" составляет +/- 0,02 дюйма);
c) допуск для размеров формата "X,XX" составляет +/- 0,13 мм ("X,XXX" составляет +/- 0,005 дюйма);
d) размеры, представленные как , рассматривают как максимальный размер ("XXXX") и минимальный размер ("YYYY"), перекрывающие номинальные допуски для удобства представления некоторых геометрических форм.
Размеры менее 10 мм (0,39 дюйма) необходимо представлять с двумя десятичными знаками так, что британский эквивалент будет находиться в пределах допуска на изготовление также с двумя десятичными знаками.
5.1.4.3 Концевые и выпускные болтовые крепления
5.1.4.3.1 Соосность отверстий
Концевые и выпускные отверстия под болты для фланцев по стандарту ИСО должны быть равномерно расположены на общей линии центров (см. таблицу 7).
5.1.4.3.2 Зацепление резьбовых шпилек
Длина зацепления резьбовой шпильки в корпусе фланцев по стандарту ИСО со шпильками должна быть равна как минимум одному НД шпильки.
5.1.4.4 Другие болтовые крепления
Средства анкерного крепления резьбовыми шпильками следует проектировать для выдерживания растягивающей нагрузки, эквивалентной нагрузке, передаваемой шпильке через полностью зацепленную гайку.
5.1.4.5 Испытальные, вентиляционные, нагнетальные и измерительные патрубки
5.1.4.5.1 Уплотнения
Испытальные, вентиляционные, нагнетальные и измерительные присоединительные патрубки (соединительные порты) должны обеспечивать герметичные уплотнения при давлении испытания оборудования, на котором они установлены.
Необходимо предусмотреть средства, обеспечивающие безопасный сброс давления после испытательного, вентиляционного, нагнетательного или измерительного присоединительных патрубков до удаления компонента.
5.1.4.5.2 Испытательные и измерительные соединительные порты
Испытательные и измерительные соединительные порты должны соответствовать требованиям 5.1.2.1.7 и 7.3.
5.1.4.6 Программа контроля наружной коррозии
Защита от наружной коррозии для подводных устьевых елок и оголовков должна быть обеспечена надлежащим выбором материалов, системой покрытий и катодной защитой. Программа защиты от коррозии представляет непрерывную деятельность по испытаниям, мониторингу и замене отработавшего срок службы оборудования. Внедрение программы защиты от коррозии не входит в область применения настоящего стандарта.
5.1.4.7 Наружные покрытия
5.1.4.7.1 Методы
Система покрытий и используемая методика должны соответствовать документально оформленным техническим условиям изготовителя оборудования или изготовителя покрытий и согласована между потребителем/поставщиком и изготовителем. При отсутствии спецификаций допустимо использование приложения I.
5.1.4.7.2 Хранение документации
Изготовитель должен поддерживать актуальность и обеспечивать доступность документации, регламентирующей системы покрытий и применяемые процедуры.
5.1.4.7.3 Цветовая окраска
Выбор цвета для обеспечения подводной видимости выполняется в соответствии с ИСО 13628-1.
5.1.4.8 Катодная защита
5.1.4.8.1 Для проектирования системы катодной защиты необходим учет наружной площади защищаемого оборудования. Документальное оформление и поддержание актуальности информации о площади поверхности, подверженной воздействию морской воды, для всего оборудования, поставляемого в соответствии с требованиями 5.1.5, является обязанностью изготовителя оборудования. Данная документация должна содержать как минимум следующую информацию:
- расположение и размер смачиваемого участка поверхности для конкретных материалов с покрытием или без покрытия;
- участки, где сварка допустима или недопустима;
- материалы конструкции и системы покрытий, прилегающие к наружным смачиваемым поверхностям;
- расположение сопряжений управляющих линий;
- сопряжения выкидных трубопроводов.
5.1.4.8.2 Для катодной защиты необходимо применять следующие стандарты проектирования:
- NACE SP0176;
- DNV RP B401.
5.1.4.8.3 Некоторые материалы чувствительны к водородному охрупчиванию при воздействии катодной защиты в морской воде. Необходимо уделять особое внимание выбору материалов для применения в условиях, требующих высокой прочности, коррозионной стойкости и стойкости к водородному охрупчиванию. К материалам с такой чувствительностью относятся мартенситные нержавеющие стали и большинство высоколегированных сталей, имеющих пределы текучести выше 900 МПа (131 000 фунт/дюйм2). Другими материалами, соответствующими данным признакам, являются упрочненные низколегированные стали, в частности, с уровнями твердости выше, чем Роквелл "C" 35 [с пределом текучести, превышающим 900 МПа (131 000 фунт/дюйм2)], дисперсионно-твердеющие медно-никелевые сплавы и некоторые высокопрочные титановые сплавы.
5.1.5 Проектная документация
Проектная документация должна включать методы, допущения, расчеты, протоколы квалификационных испытаний и требования к проверке правильности проектных решений. Требования проектной документации должны включать, но не ограничиваясь этим, критерии размеров, значения испытательного и рабочего давлений, описание материала, требования к окружающей среде и другие необходимые требования, которые должны быть учтены в конструкции. Носитель проектной документации должен быть четким, читаемым, воспроизводимым и восстанавливаемым. Проектную документацию следует хранить как минимум в течение пяти лет после изготовления последней установки данной модели, размера и номинального рабочего давления. Проектные требования должны быть занесены в технические условия изготовителя, которые должны отвечать требованиям настоящего стандарта, техническим условиям покупателя или собственным требованиям изготовителя. Технические условия изготовителя могут содержать текст, чертежи, компьютерные файлы и т.д.
5.1.6 Экспертиза проектной документации
Проектная документация должна быть проверена и подтверждена квалифицированным компетентным специалистом, не участвовавшим в разработке данного проекта.
5.1.7 Валидационные испытания
5.1.7.1 Введение
В настоящем подпункте определяются минимальные процедуры валидационных испытаний, используемые для проверки конструкций изделий в соответствии с таблицей 3. Изготовитель должен устанавливать дополнительные валидационные испытания, применимые и подтверждающие соответствие между конкретными валидационными испытаниями и предполагаемыми условиями эксплуатации и/или сроком службы, а также проводимыми в соответствии с требованиями заказчика.
5.1.7.2 Общие положения
Прототип оборудования (или опытный образец) и приспособлений, используемых для проверки конструкций с помощью процедур валидации, должен представлять собой серийные модели с точки зрения конструкции, производственных размеров/допусков, предусмотренных технологий изготовления, отклонений и материалов. При внесении в конструкцию каких-либо изменений физических, функциональных и эксплуатационных характеристик или материалов изготовитель должен документально описать влияние этих изменений на эксплуатационные свойства изделия. Конструкция, в которую вносятся существенные изменения, становится новой конструкцией, требующей повторных испытаний. Существенным изменением является изменение, влияющее на технические характеристики изделия в предполагаемых условиях эксплуатации. Существенным изменением будет любое изменение уже протестированной конфигурации или выбора материала, которое может повлиять на эксплуатационные свойства изделия или предполагаемое функционирование. Изменение должно быть документально оформлено, и изготовитель должен обосновать необходимость или отсутствие необходимости повторной проверки. Данное требование распространяется на изменения физических, функциональных и эксплуатационных характеристик или материала. При возможности обоснования применимости нового материала другими способами повторное испытание не требуется.
Примечание - Посадка, определяемая как геометрическое соотношение между деталями, включает критерии на допуск, используемые в процессе проектирования детали и сопрягаемых деталей. Посадка как состояние, которое должно быть адаптировано или подогнано, включает критерии на допуск, используемые в процессе проектирования уплотнения и сопрягаемых деталей уплотнения.
Для изделий с первичными и вторичными независимыми уплотнительными механизмами, уплотнительные механизмы должны быть верифицированы отдельно. Оборудование необходимо испытывать с минимальным количеством смазки, требуемым для сборки, за исключением случаев, когда смазку возможно добавлять во время эксплуатации оборудования или обеспечить его эксплуатацию в герметичной камере.
Фактические размеры оборудования, подвергаемого валидационным испытаниям, должны соответствовать допустимому диапазону размеров, указанных для типового эксплуатационного оборудования. Наихудшие параметры для допусков на размеры определяются изготовителем, принимая во внимание такие условия, как функционирование уплотнительной и механической частей оборудования.
5.1.7.3 Рабочая среда для испытаний
При испытании оборудования, работающего под давлением и регулирующего давление, в периоды выдерживания под давлением в качестве рабочей среды для испытаний должен быть использован газ. Для другого оборудования допустимо проведение гидростатических испытаний.
По усмотрению изготовителя могут не проводиться испытания газовой средой в качестве валидационных испытаний под давлением. Процедуры валидационных испытаний и приемочные критерии должны удовлетворять требованиям, установленным в 5.4.
5.1.7.4 Испытания с циклическим изменением давления
В таблице 3 представлен перечень оборудования, которое должно быть подвергнуто периодическим гидростатическим (или газовым, если применимо) испытаниям с циклическим изменением давления для моделирования циклического изменения давления при запуске и останове, которое происходит в течение длительного срока эксплуатации. Для данных гидростатических циклических испытаний оборудование необходимо попеременно нагружать давлением до полного номинального рабочего давления и затем полностью разгружать по завершении проведения заданного количества циклов изменения давления. Устанавливать период выдерживания под давлением для каждого цикла нагружения давлением не требуется. До и после гидростатических испытаний с циклическим изменением давления должны быть проведены стандартные гидростатические (или газовые, если применимо) испытания (см. 5.4).
5.1.7.5 Испытания под нагрузкой
Номинальная несущая способность оборудования, указанная изготовителем, в соответствии с настоящим стандартом должна быть подтверждена как валидационными испытаниями, так и инженерным анализом. В процессе испытаний оборудование должно быть нагружено до номинальной грузоподъемности с количеством циклов в соответствии с таблицей 3 без деформации, которая могла бы повлиять на какие-либо другие эксплуатационные требования (если не оговорено иначе). Инженерный анализ должен быть проведен с использованием методов и программ, которые соответствуют документально оформленной отраслевой практике.
Для испытаний под нагрузкой компонентов, регулирующих давление, см. 5.1.3.3, а также 5.1.3.6 - в случае испытаний под нагрузкой основных (первичных) конструктивных компонентов.
5.1.7.6 Испытания с циклическим изменением температуры
Валидационные испытания следует проводить при приложении RWP или в нагруженном состоянии при температуре, которая соответствует или выходит за рамки диапазона номинальной рабочей температуры.
В таблице 3 представлено оборудование, которое должно быть подвержено периодическим испытаниям с циклическим изменением температуры для моделирования циклического изменения температуры запуска и останова, которое будет происходить в течение длительного срока эксплуатации. Для этих циклических температурных испытаний оборудование необходимо попеременно нагревать и охлаждать до верхней и нижней предельных температур номинальной рабочей температуры, как определено в 5.1.2.2. В течение температурного цикла к оборудованию должно быть приложено номинальное рабочее давление при температурных максимумах, при этом не должно быть утечек сверх критериев допустимости, установленных в ИСО 10423. В качестве альтернативы испытаниям, изготовитель должен предусмотреть другие соответствующие отраслевой практике объективные доказательства того, что оборудование будет соответствовать эксплуатационным требованиям при обоих крайних значениях температуры.
5.1.7.7 Ресурсные испытания
Ресурсные испытания, такие как испытания на свинчивание/развинчивание соединителей и эксплуатационные испытания задвижек, дросселей и приводов, предназначены для оценки характеристик долговременного износа испытываемого оборудования. Проведение подобных испытаний допустимо при температурах, указанных изготовителем и документально оформленных, как соответствующие для изделия и температурного диапазона. В таблице 3 представлено оборудование, которое должно быть подвержено продолжительному ресурсному испытанию для моделирования длительного срока эксплуатации. При ресурсных испытаниях оборудование должно быть подвержено воздействию эксплуатационных циклов в соответствии с документально оформленными техническими условиями изготовителя (например, свинчивание с полным крутящим моментом, развинчивание, открытие/закрытие при полном номинальном рабочем давлении). Испытания соединителей, включающих в себя стыковочные устройства, должны включать полное разъединение/подъем как часть цикла испытаний. Дополнительные технические условия для ресурсных испытаний компонентов, приведенных в таблице 3, см. в соответствующих разделах 6 - 11, относящихся к конкретному оборудованию. В испытания должны быть включены вторичные функции, такие как вторичное разблокирование соединителя. Если возможно подтвердить, что испытания под давлением и/или температуре создают такие же нагрузки на компонент или узел, что и ресурсные испытания, общее количество приложенных циклов испытаний может суммарно соответствовать общему количеству циклов, указанному для ресурсных испытаний.
Пример - 200/3 циклов давления/температуры, приложенных при испытаниях задвижки, могут накопительно квалифицироваться как 203 цикла для 600 суммарных циклов, необходимых для ресурсных циклических испытаний.
Таблица 3
Минимальные требования к валидационным испытаниям
Компонент | Испытания под циклическим давлением/циклической нагрузкой | Испытания при циклической температуре <a> | Ресурсные циклические испытания (общее суммарное количество циклов) |
Металлическое уплотнение, подверженное воздействию среды в стволе скважины при эксплуатации | 200 | 3 | PMR <c> |
Металлическое уплотнение, не подверженное воздействию среды в стволе скважины при эксплуатации | 3 | 3 | PMR <c> |
Неметаллическое уплотнение, незащищенное в стволе скважины при эксплуатации | 200 | 3 | PMR <c> |
Неметаллическое уплотнение, защищенное в стволе скважины при эксплуатации | 3 | 3 | PMR <c> |
OEC | 200 | - | PMR <c> |
Соединители устьевого оголовка/устьевой елки/устьевой трубной головки | 3 | - | PMR <c> |
Соединители для ремонтных/внутрискважинных работ | 3 | - | 100 |
Устьевые трубные головки | 3 | - | - |
Задвижки <b> | 200 | 3 | 600 |
Приводы задвижек | 200 | 3 | 600 |
Соединители заглушки устьевой елки | 3 | - | PMR <c> |
Соединители выкидных трубопроводов | 200 | - | PMR <c> |
Подводные дроссели | 200 | 3 | 500 |
Приводы подводных дросселей | 200 | 3 | 1 000 <e> |
Подводные устьевые трубодержатели обсадных колонн | 3 | - | - |
Подводные уплотнительные узлы кольцевого пространства скважины (включая аварийные уплотнительные узлы) | 3 | 3 | - |
Подводные устьевые трубодержатели НКТ, внутренние заглушки HXT и коронные пробки | 3 | - | - |
Тарельчатые задвижки, скользящие втулки и обратная арматура | 200 | 3 | PMR <c> |
Донные устьевые трубные головки | 3 | - | - |
Донные устьевые оголовки, трубодержатели обсадных колонн, трубодержатели НКТ | 3 | - | - |
Спуско-подъемный инструмент <d> | 3 | - | PMR <c> |
<a> Температурные циклы должны соответствовать ИСО 10423. <b> До и после испытаний при циклическом давлении должны быть проведены испытания на герметичность при низком давлении, 2 МПа (300 фунт/дюйм2) +/- 10%. <c> PMR означает "по стандарту изготовителя". <d> Спуско-подъемный инструмент для подводного устьевого оголовка не включен. <e> Цикл привода дросселя определяется как общий ход дросселя от полного открытия до полного закрытия или от полного закрытия до полного открытия.
Примечание - Циклы давления, температурные и ресурсные циклы осуществляются, как показано выше, при накопительном испытании с одним изделием без замены уплотнений и компонентов. |
5.1.7.8 Валидация серии продукции
Допустимо использование изделия одного размера для верификации других размеров в серии продукции при выполнении следующих требований:
a) серией продукции считать группу продукции, для которой одинаковыми являются принципы проектирования, внешние конфигурации и выполняемые функции, но которые имеют разные размеры;
b) геометрические параметры изделия следует моделировать таким образом, чтобы уровни проектных напряжений и отклонения относительно механических свойств материала базировались на одних и тех же критериях для элементов серии продукции для того, чтобы верифицировать конструкции с помощью данного метода;
c) для верификации элементов серии продукции допустимо использование масштабирования в соответствии с ИСО 10423 (приложение F).
5.1.7.9 Документация
Изготовитель должен документально описывать используемые процедуры и результаты валидационных испытаний, используемых для проверки оборудования в соответствии с настоящим стандартом. Требования к документации для валидационных испытаний такие же, как и требования к проектной документации в 5.1.5, но дополнительно устанавливается личность персонала, проводящего и засвидетельствовавшего испытания, а также время и место испытания.
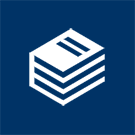