ГОСТ Р 57180-2016. Национальный стандарт Российской Федерации. Соединения сварные. Методы определения механических свойств, макроструктуры и микроструктуры
7. Определение микроструктуры сварных соединений
Оценку микроструктуры сварных соединений конструкций и деталей проводят с использованием следующих методов металлографического контроля:
- качественного (идентификация и описание структур);
- количественного - определение геометрии (размеров, площадей, формы) структурных составляющих;
- полуколичественного (сравнение с фотоэталонами и шкалами микроструктур).
7.1 Отбор и изготовление образцов для определения микроструктуры
7.1.1 Место отбора и число образцов для изготовления микрошлифов с целью определения микроструктуры сварных соединений устанавливают в нормативных и технических документах на сварные соединения конструкций и деталей.
7.1.2 При отсутствии указаний отбор образцов для определения геометрии сварного шва (наплавленного металла), участков зоны термического влияния и основного металла проводят произвольно для выявления закономерностей между механическими свойствами и структурным состоянием сварных соединений конструкций и деталей. Отбор образцов для микроанализа проводят в месте отбора для механических испытаний или темплетов для макроанализа.
7.1.3 Площадь сечения микрошлифа на образце должна быть не менее 1 см2. Для металлопродукции толщиной менее 8 мм допускается изготовление шлифов площадью менее 1 см2 в соответствии с требованиями ГОСТ 5639.
7.1.4 По окончании полирования на микрошлифах не допускаются заусенцы, острые кромки, завалы, выбоины, царапины, выкрашивания включений. Шероховатость поверхности должна быть не более 0,32 мкм по ГОСТ 2789.
7.1.5 По окончании подготовки микрошлифы промывают в этиловом спирте (ГОСТ 18300) и просушивают фильтровальной бумагой (ГОСТ 12026).
7.1.6 Отобранные пробы, заготовки и лабораторные образцы следует хранить при температуре от 15 °C до 25 °C и относительной влажности воздуха не более 50%.
7.2 Оборудование для изготовления и подготовки микрошлифов
7.2.1 Вырезку образцов для изготовления микрошлифов рекомендуется выполнять на абразивных металлорежущих станках с интенсивным охлаждением в процессе резания заготовки, обеспечивающих одновременно в процессе резания шлифовку поверхности.
7.2.2 Шлифовальные и полировальные работы при подготовке микрошлифов проводят ручным или автоматизированным способами, позволяющими удалять с поверхности нетравленого микрошлифа царапины, видимые при увеличении 100x.
7.2.3 Для проведения шлифовальных и полировальных работ автоматизированным способом используют шлифовально-полировальные станки с автоматическими головками для фиксации образцов, регулируемыми скоростями и направлением - поворотом шлифовального круга и держателя образцов, прижимным давлением держателя образцов, подачей воды для удаления остатков абразивных материалов.
7.2.4 Шлифовальные работы при ручной подготовке микрошлифов проводят на шлифовальных станках или на шлифовальных шкурках, с постепенно уменьшающимся размером зерна (ГОСТ 10054). Полировальные работы проводят на полировальном станке с горизонтальным расположением диска, обтянутого сукном, с использованием полировальных паст или суспензий.
7.2.5 Для проведения автоматизированных шлифовальных и полировальных работ образцы должны быть запрессованы с помощью специальных смол в плотные пробы "горячим" или "холодным" способом.
7.2.6 "Горячую" запрессовку проводят с использованием термоактивных и термопластичных порошков при температуре от 180 °C до 200 °C, с использованием автоматического гидравлического пресса. Образец помещают в камеру пресса, засыпают порошком, камеру закрывают, включают пресс. Процесс "горячей" запрессовки образца занимает от 18 до 22 мин, после чего готовую пробу извлекают из пресса.
7.2.7 "Холодную" запрессовку используют для материалов, чувствительных к повышенным температурам и давлению, для этого используют специальные смеси порошков и жидкостей. Образец помещают в форму, заливают приготовленной смесью, затем образец вместе с застывшим формовочным составом извлекают из формы.
7.2.8 В зависимости от конфигурации образца формы для их запрессовки и держатели для этих образцов могут иметь следующую геометрию:
- цилиндрические формы диаметром 25, 30, 40 и 50 мм;
- прямоугольные формы с размерами 30 x 60 мм и 40 x 60 мм;
- средняя высота образца должна составлять 10 - 15 мм.
7.3 Оценка микроструктуры сварных соединений
7.3.1 Количественную оценку микроструктуры проводят с использованием систем численного анализа изображения и получением спектра геометрических параметров элементов структуры (минимальные, максимальные и средние диаметры, площади структурных составляющих, характеристики и распределение неметаллических включений, характеристики анизотропии гистограммы распределений и другие). По итогам анализа должен быть сформирован отчет.
Примечание - Для определения соответствия реального масштаба полученным изображениям производят калибровку программно-аппаратного комплекса анализа изображений.
7.3.2 Оценку микроструктуры сварных соединений проводят с использованием следующих методов и требований:
- оценку дисперсности пластинчатого и зернистого перлита, размеров игл мартенсита, количества нитридов, карбидной сетки и карбидной неоднородности, соотношения мартенсита и троостита производят методом сравнения с эталонными шкалами в соответствии с требованиями ГОСТ 8233;
- оценку дисперсности и соотношения зернистого и пластинчатого перлита, оценку остатков цементитной сетки проводят в соответствии с требованиями ГОСТ 1435;
- определение обезуглероженного слоя по структуре под микроскопом - методом М; методом замера твердости - Т; методом замера микротвердости - МТ в соответствии с требованиями ГОСТ 1763;
- определение неметаллических включений в стали и сплавах сравнением с эталонными шкалами - методом Ш; подсчетом количества включений - методом К согласно требованиям ГОСТ 1778.
7.3.3 Методы выявления и определения величины зерна для сварных соединений в конструкциях и деталях из сталей и сплавов проводят в соответствии с ГОСТ 5639 и ГОСТ 21073:
- методом сравнения вида структуры с эталонными шкалами;
- методом подсчета зерен с использованием анализа изображения;
- методом подсчета пересечений границ зерен (метод хорд) с использованием анализа изображения.
7.3.4 Для сварных соединений в конструкциях и деталях из деформированных (прокатных) сталей проводят оценку перлита, структурно-свободного цементита, полосчатости феррито-перлитной структуры, видманштеттовой структуры методом сравнения с эталонными шкалами согласно требованиям ГОСТ 5640.
7.3.5 Для сварных соединений в конструкциях и деталях из аустенитных сталей проводят оценку содержания альфа-фазы методом сравнения с эталонными шкалами согласно требованиям ГОСТ 11878.
7.3.6 Для сварных соединений в конструкциях и деталях из отливок из чугуна конструкционного назначения микроструктуру оценивают в соответствии с требованиями ГОСТ 3443 по следующим критериям:
- оценка типа структуры, соотношения перлита и феррита и дисперсности перлита;
- оценка формы, размеров, распределения включений графита и количества графита;
- оценка строения, распределения, диаметра ячеек фосфидных сеток, площадь включений;
- оценка включений цементита.
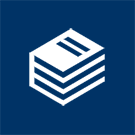