ГОСТ Р 57180-2016. Национальный стандарт Российской Федерации. Соединения сварные. Методы определения механических свойств, макроструктуры и микроструктуры
5. Определение механических свойств сварных соединений
Механические свойства сварных соединений в конструкциях и деталях определяют при проведении следующих испытаний:
- измерении твердости металла различных участков сварного соединения (см. 5.3);
- испытании металла различных участков сварного соединения на ударный изгиб (см. 5.4);
- испытании металла различных участков сварного соединения и на статическое (кратковременное) растяжение;
- испытании металла различных участков сварного соединения на стойкость против механического старения;
- испытании сварного соединения на статический изгиб (загиб).
Другие виды статических испытаний для определения свойств сварных соединений конструкций и деталей проводят в том случае, если они регламентируются нормативными и техническими документами на эти конструкции и детали.
5.1 Отбор проб и изготовление образцов для определения механических свойств
5.1.1 Образцы для определения механических свойств при механических испытаниях изготавливают из проб, вырезанных непосредственно из конструкции или детали, или из специально сваренных для проведения испытаний контрольных сварных соединений.
При выполнении контрольных сварных соединений характер подготовки под сварку, марка и толщина основного металла, марки сварочных материалов, положение шва в пространстве, начальная температура основного металла, режим сварки и термической обработки должны полностью отвечать условиям изготовления конструкций и деталей или назначению испытания.
5.1.2 Вырезку проб и заготовок для образцов целесообразно выполнять холодным способом, не допускающим деформации (поверхностного упрочнения) и нагрева, искажающего первоначальную структуру металла сварного соединения и механические свойства.
Допускается вырезать заготовки кислородной, плазменной, анодно-механической резкой и другими способами резки.
При термических способах вырезки проб их размеры определяют с учетом припуска на последующую механическую обработку, обеспечивающую отсутствие металла, подвергшегося термическому влиянию при резке в рабочей части образцов.
Припуск на величину заготовки, при котором обеспечивается отсутствие в рабочей части образца металла с измененными в результате резки свойствами, назначают в зависимости от способа резки. Значения припусков под механическую обработку должны соответствовать требованиям ГОСТ 6996.
5.1.3 Размеры проб определяются числом и размерами образцов. Пробы, заготовки и образцы для испытаний и анализа должны быть промаркированы. Клеймение проб, контрольных соединений заготовок и готовых образцов может быть проведено любым способом таким образом, чтобы клеймо было расположено вне рабочей части образца и сохранялось на образце после проведения испытания.
5.1.4 Форма и размеры образцов для испытаний на статическое растяжение при комнатной температуре должны соответствовать требованиям ГОСТ 1497, при пониженных температурах - требованиям ГОСТ 11150.
Форма и размеры образцов из сварных соединений для этих испытаний должны соответствовать требованиям ГОСТ 6996. К испытаниям не допускаются образцы, имеющие отступления по чистоте механической обработки, а также образцы с механическими повреждениями в рабочей части. Их заменяют таким же числом новых образцов, изготовленных из той же пробы или контрольного соединения.
5.1.5 При подготовке образцов для измерения твердости должна соблюдаться параллельность рабочей и опорной поверхностей образцов.
5.2 Оборудование для определения механических свойств
5.2.1 Приборы для измерения твердости (твердомеры) должны соответствовать требованиям ГОСТ 23677.
5.2.2 Оборудование для испытаний на статическое растяжение (разрывные машины) при комнатной температуре должно соответствовать требованиям ГОСТ 1497; при пониженной температуре - ГОСТ 11150.
5.2.3 Оборудование для испытаний на ударный изгиб (маятниковые копры) должно соответствовать требованиям ГОСТ 9454.
5.2.4 Измерительное и вспомогательное оборудование и средства контроля должны проходить периодическую поверку (калибровку) и аттестацию в соответствии с требованиями ГОСТ Р 8.568.
5.3 Измерение твердости сварных соединений
5.3.1 Измерение твердости сварных соединений конструкций и деталей проводят следующими методами: по Виккерсу (HV) в соответствии с требованиями ГОСТ 2999, по Бринеллю (HB) в соответствии с требованиями ГОСТ 9012 и по Роквеллу - шкалам A, B и C (HRA, HRB и HRC) в соответствии с требованиями ГОСТ 9013, отдавая предпочтение замеру по Виккерсу.
5.3.2 Измерение твердости по Виккерсу проводят на микрошлифах или образцах с полированной поверхностью, если очертания шва видны без травления. Шероховатость поверхности должна быть не более 0,16 мкм по ГОСТ 2789.
5.3.3 Измерение твердости по Бринеллю или по Роквеллу проводят на макрошлифах или на образцах с шлифованной поверхностью, если очертания шва видны без травления. Шероховатость поверхности образцов (или участка для измерения твердости) должна быть не более 2,5 мкм по ГОСТ 2789, если нет других указаний в нормативных и технических документах на металлопродукцию.
5.3.4 Измерение микротвердости проводят на микрошлифах или образцах с полированной поверхностью, если очертания шва видны без травления.
Шероховатость поверхности должна быть не более 0,32 мкм по ГОСТ 2789.
5.3.5 Измерение твердости проводят в поперечном сечении образцов для всех видов сварных соединений конструкций и деталей в соответствии с приложением А.
5.3.6 Твердость основного металла, различных участков зоны термического влияния и металла шва измеряют по одной или нескольким линиям, указанным на рисунке А.1 (приложение А). Если соединение выполнено из металлов различных марок, то твердость измеряют для каждого из них.
При измерениях, выполняемых в непосредственной близости от границы сплавления, рекомендуется проводить два-три измерения в соответствии с позицией I рисунка А.2 (приложение А) или дополнительные измерения по позиции II рисунка А.2 (приложение А).
Допускается проведение измерений на участках сварного соединения, указанных на рисунке А.3 (приложение А).
5.3.7 Твердость стыковых и угловых соединений, выполненных дуговой сваркой, измеряют:
- при толщине основного металла или углового шва от 1,5 до 9 мм - в соответствии с позицией VIII рисунка А.1 (приложение А) по одной пунктирной линии;
- при толщине от 9 до 25 мм - в соответствии с позициями I и III рисунка А.1 (приложение А) по двум сплошным линиям;
- при толщине от 26 до 60 мм - в соответствии с позициями II или III рисунка А.1 (приложение А) по двум сплошным и одной пунктирной линиям.
Схему измерения твердости при толщине основного металла или углового шва более 60 мм оговаривают в технических документах на сварное соединение конкретной детали или конструкции.
5.3.8 Твердость сварных соединений, полученных электрошлаковой сваркой, измеряют в соответствии с позицией IV рисунка А.1 (приложение А).
Число точек измерений в зоне термического влияния должно быть не менее 10.
5.3.9 Твердость различных участков металла шва измеряют в соответствии с позицией V рисунка А.1 (приложение А).
5.3.10 Твердость сварных соединений, полученных сваркой давлением, измеряют в соответствии с позицией VI рисунка А.1 (приложение А).
5.3.11 Твердость наплавленного металла при контроле качества сварочных материалов измеряют в соответствии с позицией VII рисунка А.1 (приложение А).
5.3.12 Измерение микротвердости проводят для определения свойств сварных соединений, глубина и площадь которых не позволяют проводить замеры твердости вышеуказанными методами; отдельных участков; структурных составляющих; зерен; тонких слоев покрытий и зон термического влияния сварных соединений; поверхностных явлений (обезуглероживания); явлений, связанных с локальным пластическим деформированием; изучения химической и структурной неоднородностей, а также для получения значительного количества замеров (для накопления объективной информации). Измерение микротвердости проводят в соответствии с требованиями ГОСТ 9450.
5.4 Испытание сварных соединений на ударный изгиб и (или) вязкость разрушения
5.4.1 Испытание сварных соединений на ударный изгиб с определением ударной вязкости или работы удара, или процентного соотношения хрупкой и вязкой составляющих поверхности излома (определяется температурный интервал хрупкости по наличию 50% вязкой составляющей в изломе) проводят для металла сварного шва (наплавленного металла), различных участков зоны термического влияния и основного металла. Предпочтительными для образцов из сварных соединений конструкций и деталей являются образцы с V-образным надрезом (образцы Шарпи).
5.4.2 Испытание сварных соединений на вязкость разрушения проводят для металла сварного шва, различных участков зоны термического влияния и основного металла.
5.4.3 Испытания на ударный изгиб и (или) вязкость разрушения проводят при нормальной температуре (18 °C) и при температуре минус 60 °C в том случае, если в нормативных и технических документах такое требование не предъявляется к основному материалу этих конструкций и деталей.
5.4.4 Численные значения параметров, определяющих механические свойства сварных соединений, устанавливаются нормативными и техническими документами отрасли (например, ГОСТ Р 53192) или в документации на конкретную конструкцию (изделие).
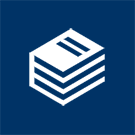