ГОСТ 33756-2016. Межгосударственный стандарт. Упаковка потребительская полимерная. Общие технические условия
9. Методы контроля
9.1 Порядок подготовки к проведению контроля
9.1.1 Образцы упаковки, отобранные в выборку, помещают в транспортную упаковку и направляют для проведения контроля.
9.1.2 Перед испытанием образцы упаковки кондиционируют не менее трех часов при температуре (22 +/- 4) °C и относительной влажности (65 +/- 5)%.
9.2 Контроль внешнего вида
Внешний вид, качество поверхности и покрытий, маркировку проверяют визуально без применения увеличительных приборов, путем сравнения с образцами-эталонами (при наличии), по стандартам и технической документации на конкретные виды упаковки.
Цвет изделия оценивают визуально сравнением с образцом-эталоном при естественном и искусственном освещении и/или в световом шкафу (на световом столе).
9.3 Контроль геометрических размеров
9.3.1 Порядок проведения контроля и обработки результатов измерений
При контроле проверяют наружные габаритные размеры упаковки (диаметр, длина, ширина и высота), а также присоединительные размеры горловины упаковки (внутренние и наружные диаметры).
Количество образцов для контроля - в соответствии с разделом 8.
Наружный диаметр упаковки измеряют в месте наибольшего диаметра в двух взаимно перпендикулярных направлениях. За результат измерения принимают среднеарифметическое значение двух измерений, при этом разница между двумя измерениями не должна превышать суммарный допуск.
При контроле габаритных размеров упаковки контроль проводят в месте наибольшего сечения упаковки.
Внутренний и наружный диаметры горловины упаковки измеряют в двух взаимно перпендикулярных положениях. За значение измерения принимают среднеарифметическое значение двух измерений, при этом разница между двумя определениями не должна превышать суммарный допуск.
Высоту упаковки определяют в двух противоположных направлениях. За результат измерения высоты принимают среднеарифметическое значение двух определений.
Размеры должны соответствовать установленным в стандартах и/или технической документации на конкретные виды упаковки.
9.3.2 Контроль диаметров, длины, ширины упаковки штангенциркулем
Губки штангенциркуля по ГОСТ 166 раздвигают на величину, несколько большую, чем измеряемый размер упаковки. Устанавливают штангенциркуль так, чтобы образец был расположен параллельно оси, а губки штангенциркуля - перпендикулярно к измеряемому размеру образца упаковки. Плавно уменьшают расстояние между губками штангенциркуля до их соприкосновения с образцом упаковки.
9.3.3 Контроль высоты упаковки штангенрейсмасом
Контролируемый образец упаковки устанавливают вертикально на поверочную (разметочную) плиту по ГОСТ 10905. Устанавливают на эту же плиту штангенрейсмас по ГОСТ 164. Плавно уменьшают высоту ножки штангенрейсмаса до касания с торцом горловины упаковки. Фиксируют показания штангенрейсмаса.
9.3.4 Контроль калибрами
Образец упаковки устанавливают между проходными сторонами калибра, а затем между непроходными. Образец должен свободно проходить между проходными и не проходить между непроходными сторонами.
При контроле диаметра горловины упаковки калибр поочередно вставляют проходной и непроходной стороной в горловину образца упаковки. Проходная сторона должна проходить свободно, без усилия. Непроходная сторона калибра должна быть больше диаметра горловины.
При контроле высоты упаковки калибрами - образец при вращении вокруг своей оси должен проходить под плоскостью "максимальная высота" или не проходить под плоскостью "минимальная высота".
9.4 Контроль толщины стенки
9.4.1 Средства контроля и вспомогательные устройства
Для контроля толщины стенки методом неразрушающего контроля используют магнитно-индукционные толщиномеры; при контроле толщин изделий методом разрушающего контроля на плоских участках могут быть использованы гладкие микрометры по ГОСТ 6507, на закругленных участках - индикаторы часового типа по ГОСТ 577, штативы для измерительных головок - по ГОСТ 10197.
9.4.2 Порядок подготовки и проведения контроля
9.4.2.1 Для проведения измерений методом неразрушающего контроля включают магнитно-индукционный толщиномер, помещают металлический шарик внутрь изделия, к внешней стороне изделия подносят магнитный индикатор. Совмещают положение шарика и индикатора. Положение индикатора должно быть перпендикулярно по отношению к измеряемой поверхности. Результаты измерений считывают с дисплея прибора.
9.4.2.2 Для проведения измерений методом разрушающего контроля каждый образец упаковки с помощью ножниц разрезают в вертикальной плоскости и проводят измерение в точках, установленных в стандартах или технической документации на конкретные виды тары.
Если средство измерения не позволяет правильно произвести измерение толщины стенки, из каждого образца упаковки вырезают контрольные образцы в местах измерения (сферической или цилиндрической части упаковки) и проверяют толщину образца упаковки.
За результат измерения принимают наименьшее значение из всех измерений, проведенных в данной точке образцов упаковки.
Упаковку считают выдержавшей испытания, если значение толщины стенки соответствует значению, установленному в стандартах или технической документации на конкретный вид упаковки.
9.5 Контроль вместимости
9.5.1 Средства контроля и вспомогательные устройства:
- стеклянные мерные цилиндры по ГОСТ 1770;
- весы по ГОСТ OIML R 76-1;
- другие средства контроля в соответствии со стандартами или технической документацией на конкретные виды упаковки.
9.5.2 Порядок подготовки и проведения контроля
9.5.2.1 Объемный метод контроля
Каждый образец упаковки заполняют водой до номинальной вместимости, наливая воду из мерной посуды, при температуре (22 +/- 4) °C. За вместимость образца упаковки принимают среднеарифметическое значение по объему воды, налитой в контролируемые образцы упаковки.
Вместимость упаковки должна соответствовать установленной в стандартах и технической документации на конкретный вид упаковки.
9.5.2.2 Весовой метод контроля
Чистый и сухой образец упаковки взвешивают на весах. Затем наполняют до номинальной вместимости водой температурой (22 +/- 4) °C и снова взвешивают, определяя общую массу. При взвешивании наружная поверхность образца упаковки должна быть сухой.
Разность между массой образца упаковки, наполненного водой, и массой порожнего образца упаковки, в граммах, соответствует его вместимости в кубических сантиметрах.
Вместимость упаковки должна соответствовать указанной в технической документации на конкретный вид упаковки.
Отклонение номинальной вместимости должно соответствовать указанному значению в стандартах и технической документации на конкретный вид упаковки. Рекомендуемое отклонение номинальной вместимости составляет не более 5% заданного значения.
При разногласиях за окончательный результат принимают значение номинальной вместимости, полученное при весовом методе контроля.
9.6 Контроль массы
9.6.1 Средства контроля и вспомогательные устройства - в соответствии со стандартами или технической документацией на конкретный вид упаковки.
9.6.2 Порядок подготовки и проведение контроля
Каждый образец взвешивают на весах по ГОСТ OIML R 76-1.
Масса упаковки должна соответствовать указанной в технической документации на конкретный вид упаковки.
9.7 Контроль герметичности упаковки
9.7.1 Контроль герметичности упаковки проводят двумя методами: в вакуумной камере и/или статическим методом.
9.7.2 Подготовка и проведение контроля
Образец упаковки заполняют водой и/или окрашенной водой температурой (22 +/- 4) °C до номинального объема, удаляют следы воды с наружной поверхности образца упаковки и плотно укупоривают.
Укупоренный образец помещают на фильтровальную бумагу в положении, указанном в таблице 7.
Таблица 7
Положение упаковки при контроле герметичности
Вид упаковки | Положение упаковки при проведении контроля | ||
на боку | на горловине/крышке | под заданным углом | |
Банки | - | + | + |
Ведра | - | + | - |
Бутылки/флаконы | + | - | + |
Канистры | + | - | + |
Тубы | + | - | + |
Стаканчики | - | + | - |
Примечания 1 Знак "+" означает, что показатель проверяют, знак "-" - не проверяют. 2 Положение под заданным углом применяют только при статическом методе контроля. |
9.7.3 Определение герметичности упаковки в вакуумной камере
9.7.3.1 Используемое оборудование - вакуумный шкаф или специальный стенд для проверки упаковки на герметичность внутренним объемом не менее 0,02 м3.
9.7.3.2 Принцип испытания упаковки на герметичность приведен на рисунке 1.
Рисунок 1 - Контроль герметичности упаковки
в вакуумной камере
Вакуумную камеру герметизируют и с помощью вакуумного насоса понижают давление в замкнутом пространстве камеры до достижения остаточного давления, заданного в таблице 2.
После достижения остаточного давления включают секундомер и выдерживают образец упаковки в течение 15 с.
Отсутствие следов воды на фильтровальной бумаге свидетельствует о герметичности упаковки.
9.7.4 Статический метод испытания герметичности упаковки
Используемое оборудование - лабораторный стол.
Средства контроля и вспомогательные устройства - в соответствии со стандартами или технической документацией на конкретные виды упаковки.
Укупоренный образец упаковки помещают на ровную гладкую поверхность (лабораторный стол) на фильтровальную бумагу в положении, указанном в таблице 7.
В таком положении испытуемые образцы упаковки выдерживают в течение 2 ч.
Отсутствие следов воды на фильтровальной бумаге свидетельствует о герметичности упаковки.
9.7.5 При использовании для герметизации бутылок/флаконов укупорочного средства зажимного типа после проведения испытаний укупорочное средство снимают с образца упаковки и проверяют наличие следов воды на внешней поверхности горловины упаковки под укупорочным средством. Следы воды свидетельствуют о нарушении герметичности.
9.7.6 Допускается упаковку, укупориваемую методом запайки, не испытывать на герметичность на предприятии - изготовителе упаковки.
9.8 Контроль прочности на удар при свободном падении
9.8.1 Используемое оборудование - установка для испытания прочности на удар при свободном падении в соответствии с рисунком 2.
1 - приспособление для установки образцов
упаковки в исходное положение (сбрасывающее устройство);
2 - грузоподъемная штанга; 3 - укосины; 4 - вертикальная
стойка; 5 - контрольное устройство; 6 - стальная
плита фундамента
Рисунок 2 - Внешний вид стенда для испытания упаковки
на удар при свободном падении
Средства контроля и вспомогательные устройства - в соответствии со стандартами или технической документацией на конкретные виды упаковки.
Установка состоит из опорной стальной плиты толщиной не менее 80 мм и вертикальной стойки с нанесенной на нее шкалой и контрольным устройством положения. Грузоподъемная штанга крепится на отдельной стойке и снабжена сбрасывающим устройством.
9.8.2 Порядок подготовки к проведению контроля
Образец упаковки заполняют водой температурой (22 +/- 4) °C до номинального объема под укупорочное средство, удаляют следы воды с внешней поверхности тары и плотно закрывают укупорочным средством.
Заполненные и укупоренные образцы упаковки кондиционируют при температуре (22 +/- 4) °C не менее 4 ч.
Образец, подготовленный к испытаниям, поднимают на заданную по таблице 3 высоту, которая определяется как кратчайшее расстояние между самой низкой точкой образца и поверхностью ударной плиты.
Высоту подъема контролируют с помощью контрольного устройства положения, входящего в состав стенда. Затем образец упаковки фиксируют таким образом, чтобы обеспечить свободное падение испытуемой упаковки на дно без вращения. Погрешность установки высоты сбрасывания не более 2%.
9.8.3 Порядок проведения контроля
Образец упаковки сбрасывают один раз на дно. Упаковку считают выдержавшей испытания, если на образцах не наблюдают механических повреждений, приводящих к потере герметичности, контролируемой по отсутствию течи. Деформации, не приводящие к потере герметичности, не учитывают.
9.8.4 При проведении испытаний упаковки, укупоренной методом запайки, требование не распространяется на поверхность пленки (фольги) и место сварного шва.
9.9 Контроль прочности на сжатие
9.9.1 Контроль прочности на сжатие упаковки проводят двумя методами:
Метод А - испытания незаполненной упаковки и/или метод Б - испытания заполненной упаковки. Приоритетными считают испытания незаполненной упаковки.
9.9.2 Используемое оборудование - универсальная испытательная машина, обеспечивающая скорость приложения нагрузки от 1 до 200 мм/мин и воспроизведение усилия в диапазоне от 0 до 10000 Н (от 0 до 1000 кгс) с погрешностью не более 1% измеряемого значения. Если для определения прочности на сжатие используют заполненную и укупоренную упаковку, универсальная испытательная машина должна быть выполнена во влагозащищенном исполнении.
Средства контроля и вспомогательные устройства - в соответствии со стандартами или технической документацией на конкретные виды упаковки.
9.9.3 Порядок подготовки контроля
9.9.3.1 Метод А. Незаполненные (порожние) образцы упаковки устанавливают вертикально на дно между плитами универсальной испытательной машины, центрируют на середине плиты и опускают плиту до соприкосновения с образцом без приложения нагрузки. Задают скорость сжатия в соответствии со значениями, указанными в таблице 8.
Таблица 8
Условия проведения испытания на сжатие
Вместимость упаковки, дм3 | Скорость приложения нагрузки, мм/мин | ||||||
Банки | Ведра | Бутылки/флаконы | Канистры | Тубы | Коробки | Стаканчики | |
До 0,5 включ. | 100 | 100 | 30 | - | 30 | 30 | 100 |
Св. 0,5 " 1,5 " | 100 | 100 | 100 | 100 | 30 | 30 | 100 |
" 1,5 " 5,0 " | 100 | 100 | 100 | 100 | 100 | 100 | 100 |
" 5,0 " 12,0 " | 100 | 100 | 100 | 100 | - | 100 | 100 |
9.9.3.2 Метод Б. Образец упаковки заполняют водой температурой (22 +/- 4) °C до номинального объема, удаляют следы воды с наружной поверхности образца, упаковку плотно укупоривают.
Укупоренный образец помещают в водонепроницаемый мешок и неплотно его герметизируют рядом с горловиной упаковки. Образцы упаковки в мешке устанавливают вертикально на дно между плитами универсальной испытательной машины, центрируют на середине плиты и опускают плиту до соприкосновения с образцом без приложения нагрузки. Герметизирующий узел мешка не должен находиться между укупорочным средством и плитой. Задают скорость сжатия в соответствии со значениями, указанными в таблице 8.
9.9.4 Порядок проведения контроля
Образцы упаковки сжимают до появления точки перегиба на графике зависимости нагрузка-деформация.
По максимальному значению на графике определяют предельное значение усилия на сжатие.
Фиксируют значение усилия и снимают нагрузку. Усилие не должно быть меньше значений, приведенных в таблице 4.
Примеры типовых кривых нагрузок при сжатии приведены (приложение Г).
9.10 Контроль прочности крепления ручек
9.10.1 Подготовка и проведение контроля
Образец упаковки заполняют материалом в габаритно-массовом эквиваленте (см. 5.2.4) и закрывают укупорочным средством.
При испытании ручек на прочность или на прочность их крепления образец упаковки подвешивают за каждую ручку на жестко закрепленном приспособлении в виде оправки шириной 120 - 130 мм (средняя ширина руки человека) и скругленными краями, имитирующем распределенную нагрузку. Время выдерживания в нагруженном состоянии не менее 6 ч.
Упаковку считают выдержавшей испытание, если по истечении указанного времени: нет повреждения сопряжения ручки с местом ее крепления к упаковке; нет повреждений в месте сопряжения ручки с упаковкой или горловины упаковки с укупорочным средством, не произошло открывания укупорочного средства и/или его разрушения, на ручках нет трещин и разрушений.
Допускается незначительная деформация отверстия для крепления ручки, не приводящая к выпадению ручки после снятия нагрузки.
9.11 Контроль стойкости к горячей воде
9.11.1 Используемое оборудование, средства контроля и вспомогательные устройства - в соответствии со стандартами или технической документацией на конкретные виды упаковки.
9.11.2 Определение стойкости к горячей воде проводят методами А и Б.
9.11.3 Метод А
Испытуемый образец полностью погружают в термостат с водой. Включают термостат, нагревают воду в термостате до температуры (70 +/- 5) °C и выдерживают при данной температуре в течение 30 мин. Затем термостат отключают, вода в термостате остывает до температуры (22 +/- 4) °C, образец упаковки вынимают из термостата, сливают воду из образца и образец насухо вытирают.
После испытания образец должен остаться без видимых изменений. В случае испытания окрашенной упаковки вода не должна окрашиваться. В случае испытания декорированной упаковки покрытие не должно отслаиваться, вода не должна окрашиваться.
В стандартах и технической документации на конкретные виды упаковки в зависимости от используемого полимерного материала может быть установлена другая температура испытания, но не менее 50 °C.
Не подлежит испытанию по данному методу упаковка с покрытием, содержащим водорастворимые компоненты.
9.11.4 Метод Б
Испытуемый образец упаковки заполняют водой температурой (70 +/- 5) °C до номинального объема, удаляют следы воды с внешней поверхности упаковки, плотно закрывают укупорочным средством и оставляют в помещении с температурой (22 +/- 4) °C до полного остывания воды.
После испытания образец упаковки должен остаться без видимых изменений по боковой поверхности. Допускается втягивание дна и укупорочного средства, не приводящее к нарушению герметичности.
В случае испытания окрашенной упаковки вода не должна окрашиваться. В случае испытания декорированной упаковки покрытие не должно отслаиваться.
В стандартах и технической документации на конкретные виды упаковки в зависимости от используемого полимерного материала для испытания может быть установлена другая температура, но не менее 50 °C.
9.12 Контроль химической стойкости
Средства контроля и вспомогательные устройства - в соответствии со стандартами или технической документацией на конкретные виды упаковки.
В качестве химического реагента используют модельные среды: ОП-7 и ОП-10 ГОСТ 8433, ацетон ГОСТ 2768, этиловый спирт ГОСТ 18300.
В стандартах и технической документации на упаковку для проведения испытаний на химическую стойкость могут быть указаны другие модельные среды.
9.12.1 Контроль стойкости к растрескиванию
9.12.1.1 Подготовка к проведению контроля
Испытания проводят на образцах упаковки любой вместимости.
Количество образцов для испытаний упаковки устанавливают в технической документации на конкретные виды упаковки, но не более 10 образцов.
Перед испытаниями отбирают образцы, кондиционируют по 9.1.2, и каждому образцу присваивают соответствующий порядковый номер.
После кондиционирования отбирают два эталонных образца для оценки внешнего вида упаковки после испытаний.
Каждый образец упаковки заполняют продуктом до номинальной вместимости, герметично закрывают и переворачивают несколько раз до достижения равномерного смачивания всей внутренней поверхности упаковки.
9.12.1.2 Порядок проведения контроля
Одинаковое количество образцов упаковки с продуктом выдерживают в климатической камере при температуре (40 +/- 3) °C и при температуре (22 +/- 4) °C в течение 28 сут.
При невозможности проведения испытаний в климатической камере все образцы упаковки с модельной средой выдерживают при температуре (22 +/- 4) °C в течение гарантийного срока хранения упаковываемого продукта.
В стандартах или технической документации на конкретные виды упаковки и/или конкретной продукции могут быть указаны другие значения температуры и другие значения продолжительности испытаний, другие модельные среды.
По истечении установленного времени 28 сут или гарантийного срока хранения упакованной продукции проводят оценку внешнего вида упаковки.
Образцы упаковки в течение установленного времени не должны изменять свой внешний вид при сравнении с образцом, не подвергавшимся испытаниям. Оценку изменения внешнего вида проводят в соответствии с 5.2.
9.13 Контроль стойкости к проницаемости химических растворителей
9.13.1 Подготовка к проведению контроля
Испытания проводят на образцах упаковки любой вместимости.
Количество образцов для испытаний упаковки устанавливают в технической документации на конкретные виды упаковки, но не более 10 образцов.
Для испытаний отбирают образцы упаковки, прошедшие кондиционирование по 9.1.2, и каждому образцу присваивают соответствующий порядковый номер.
После кондиционирования каждый образец взвешивают на весах и отбирают два эталонных образца для оценки внешнего вида после испытаний.
Каждый образец упаковки заполняют модельной средой в соответствии с 9.13.1 до номинальной вместимости, герметично закрывают и взвешивают на весах.
Стойкость к проницаемости органических растворителей определяют по изменению массы модельной среды, содержащейся в упаковке, за 28 сут или в течение гарантийного срока хранения упакованной продукции.
9.13.2 Проведение контроля
Половину выборки образцов с модельной средой выдерживают в климатической камере при температуре (22 +/- 4) °C в течение 28 сут. Вторую половину выборки образцов упаковки с модельной средой выдерживают при температуре (40 +/- 3) °C в течение 28 сут.
При невозможности проведения испытаний в климатической камере все образцы с модельной средой выдерживают при температуре (22 +/- 4) °C в течение гарантийного срока хранения упакованного продукта.
В стандартах или технической документации на конкретные виды упаковки и/или конкретные виды продукции могут быть указаны другие значения температуры и другие значения продолжительности испытаний, другие модельные среды.
По истечении установленного времени 28 сут или гарантийного срока годности упаковываемой продукции образцы взвешивают на весах, затем определяют потерю массы в процентах и оценивают изменение внешнего вида упаковки.
9.13.3 Изменение массы модельной среды, содержащейся в упаковке, за установленное время AM, %, после окончания испытаний определяют по формуле
(5)
где M1 - масса упаковки с модельной средой до испытаний, г;
M2 - масса упаковки с модельной средой после выдержки в климатической камере в течение установленного времени, г;
M0 - исходная масса модельной среды, определяемая как разность массы упаковки с модельной средой и массы порожней упаковки, г.
За результат испытаний принимают среднеарифметическое значение не менее пяти определений.
Изменение массы модельной среды не должно превышать значений, установленных в 5.2.6.2.
9.13.4 Образцы упаковки в течение установленного времени не должны изменять своего внешнего вида по сравнению с образцом, не подвергавшимся испытаниям. Изменения внешнего вида оценивают в соответствии с 5.2.1.
9.14 Контроль стойкости рисунка, нанесенного на упаковку
9.14.1 Порядок подготовки к проведению контроля
Образцы упаковки после нанесения рисунка или покрытия выдерживают при температуре (22 +/- 4) °C не менее 24 ч.
9.14.2 Порядок проведения контроля
На упаковку с покрытием накладывают полосу клейкой ленты длиной 100 мм, шириной не менее 10 мм, оставляя конец полосы длиной 10 мм неприклеенным.
Для испытания декоративных покрытий, наносимых методом офсета, используют клейкую ленту с адгезией от 5,5 до 5,7N/25 мм. Для испытания декоративных покрытий, наносимых методом впаиваемой этикетки, используют клейкую ленту с адгезией от 4,5 до 5,0N/25 мм.
Затем приглаживают клейкую ленту вручную для удаления из-под нее пузырьков воздуха и оттягивают назад под углом менее 180°. Первые 50 - 60 мм ленты оттягивают медленным движением, а затем резким движением.
9.14.3 Правила обработки результатов контроля
За стойкость покрытия к клейкой ленте принимают среднее арифметическое значение трех испытаний в соответствии с балльной системой:
- четыре балла - на клейкой ленте отсутствуют следы покрытия;
- три балла - незначительное отслаивание покрытия (не более 10%);
- два балла - умеренное отслаивание покрытия (10% - 30%);
- один балл - значительное отслаивание покрытия (более 30%).
Упаковку считают выдержавшей испытания, если состояние покрытия может быть оценено не менее двух баллов.
9.15 Контроль теплостойкости
9.15.1 Используемое оборудование, средства контроля и вспомогательные устройства - в соответствии со стандартами или технической документацией на конкретные виды упаковки.
9.15.2 Порядок подготовки и проведения контроля
Образцы упаковки помещают в климатическую камеру, устанавливают температуру (40 +/- 3) °C. Образцы выдерживают в камере в течение 2 ч.
Затем образцы вынимают из камеры, выдерживают при комнатной температуре в течение 30 мин.
После выдержки проводят проверку внешнего вида, параметров и размеров, механических свойств.
Образцы считают выдержавшими испытания, если они соответствуют требованиям, установленным в 4.3, 4.4, 5.2.1, 5.2.3 и 5.2.4.
9.15.3 Подготовка и проведение испытания упаковки, применяемой при повышенных температурах
Необходимость проведения испытания упаковки при повышенных температурах предусматривают в стандартах или технической документации на упаковку для конкретных видов продукции.
Образцы упаковки помещают в климатическую камеру, устанавливают температуру (40 +/- 3) °C. Образцы выдерживают в камере в течение 2 ч.
Затем образцы вынимают из камеры и сразу же проводят испытания в соответствии с 9.9.3 настоящего стандарта.
Образцы считают выдержавшими испытания, если стойкость к вертикальной нагрузке снизилась не более, чем на 30% по отношению к образцам, не подвергавшимся нагреву.
9.16 Контроль морозостойкости
9.16.1 Используемое оборудование, средства контроля и вспомогательные устройства - в соответствии со стандартами или технической документацией на конкретные виды упаковки.
9.16.2 Порядок подготовки и проведения контроля
Образцы упаковки помещают в климатическую камеру, устанавливают температуру (минус 25 +/- 2) °C. Образцы выдерживают в камере в течение 2 ч.
Затем образцы вынимают из камеры, выдерживают при комнатной температуре в течение 30 мин.
После выдержки проводят контроль внешнего вида, параметров и размеров, показателей механической прочности.
Образцы упаковки считают выдержавшими испытания, если они соответствуют требованиям, установленным в 4.3, 4.4, 5.2.1, 5.2.3 и 5.2.4.
9.16.3 Порядок подготовки и проведения контроля для упаковки, применяемой при отрицательных температурах
Образцы тары наполняют модельной средой на 70% от номинального объема под крышку, закрывают неплотно укупорочным средством и помещают в морозильную камеру. Устанавливают температуру минус 18 +/- 4 °C и выдерживают в камере до достижения температуры модельной среды минус 18 +/- 4 °C.
Затем образцы вынимают из камеры и сразу проводят испытание на прочность по 9.8.3.
В качестве модельной среды используют воду. В стандартах и технической документации на конкретные виды упаковки для проведения испытаний на морозостойкость могут быть указаны другие модельные среды.
9.17 Определение прочности шарнирного соединения
Для определения прочности шарнирного соединения крышку коробки открывают и закрывают в соответствии с 5.3. Упаковку считают выдержавшей испытания, если отсутствуют повреждения стенок и крышек коробок.
9.18 Правила оформления результатов контроля
Результаты контроля регистрируют в журнале или оформляют протоколом, содержащим следующие данные:
- наименование и условное обозначение упаковки;
- вместимость упаковки;
- наименование материала, из которого изготовлена упаковка;
- обозначение нормативного или технического документа, по которому изготовлена упаковка;
- количество образцов, подвергнутых испытанию;
- номер партии;
- дата изготовления;
- объем партии;
- дата проведения испытаний;
- результаты испытаний;
- подпись специалиста, проводившего испытания.
Результаты контроля при периодических испытаниях оформляют протоколом.
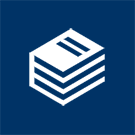