ГОСТ 33757-2016. Межгосударственный стандарт. Поддоны плоские деревянные. Технические условия
4 Общие технические требования
Поддоны изготовляют в соответствии с требованиями настоящего стандарта по технической и/или технологической документации, рабочим чертежам на поддоны для конкретных видов продукции.
4.1 Характеристики
4.1.1 Конструкция поддонов должна обеспечивать: надежность и удобство в эксплуатации; сохранность груза при штабелировании, загрузке и выгрузке; возможность выполнения и безопасность погрузочно-разгрузочных работ с применением вилочных погрузчиков или других транспортных средств (иного оборудования).
4.1.2 Поверхность нижнего настила поддонов должна составлять не менее 40% от поверхности верхнего настила.
4.1.3 Детали поддонов должны быть без пороков древесины: острого обзола, прорости, механических повреждений, гнили и инородных включений.
4.1.4 Тупой обзол допускается на двух кромках каждой детали при условии, что на них отсутствует кора и размер обзола в поперечном направлении не превышает 15 мм.
4.1.5 В каждой доске допускается одна глубокая трещина длиной не более ширины доски, если трещина образовалась не при сборке поддона. В шашках допускаются только пластевые трещины усушки.
4.1.6 Внутренняя заболонь допускается в древесине лиственных пород, если она не более 1/4 ширины доски и 1/2 толщины доски.
В древесине хвойных и лиственных пород допускаются грибные заболонные окраски, не являющиеся результатом плохих условий сушки или хранения.
4.1.7 Сучки диаметром до 10 мм не учитывают. Допускаются сросшиеся сучки. Диаметр одного сучка не должен превышать:
- 1/4 ширины доски - для поперечных досок;
- 1/3 ширины доски - для остальных досок.
На каждом отрезке доски, соответствующем по длине, ширине доски, сумма диаметров нескольких сучков не должна превышать:
- 1/3 ширины доски - для поперечных досок;
- 1/2 ширины доски - для остальных досок.
4.1.8 Отверстия от сучков, выпавших при обработке досок, должны заделываться пробками из древесины той же породы, что и доски, с применением водостойкого клея по ГОСТ 12172 или другой технической документации.
4.1.9 Доски и шашки должны быть цельными.
Допускается по согласованию с заказчиком применять шашки, состоящие из двух частей, соединенные водостойкими клеями по технической документации.
Волокна древесины шашек должны располагаться вдоль поддона. В шашках не допускается сердцевина.
4.1.10 Все поверхности досок и шашек должны быть опилены, за исключением фасок на продольных кромках досок основания в местах ввода вил погрузчика. Фаски образуют строганием или фрезерованием. Углы поддона должны быть опилены.
4.1.11 Параметр шероховатости верхней поверхности деталей верхнего настила поддона Rmmax <= 500 мкм и остальных поверхностей - Rmmax <= 1250 мкм по ГОСТ 7016.
4.1.12 Влажность древесины поддонов не должна превышать 22%.
4.1.13 Поддоны изготовляют соединением продольных досок настила с поперечными досками, шашками и досками основания крепежными элементами.
Типы и определения крепежных элементов - по ГОСТ ISO 445.
В качестве крепежных элементов для соединения досок настила с поперечными досками применяют фосфатированные или оксидированные гвозди с кольцевой накаткой диаметром от 2,8 до 3,5 мм и длиной от 40 до 60 мм по технической документации.
Доски настила соединяют с шашками винтовыми или ершеными гвоздями по технической документации диаметром от 2,8 до 4,2 мм и длиной от 80 до 90 мм.
Доски основания соединяют с шашками винтовыми или ершеными гвоздями диаметром от 2,8 до 4,2 мм и длиной от 70 до 90 мм по технической документации.
Гвозди должны быть забиты со стороны продольных досок настила. Выступающие концы гвоздей должны быть подогнуты и утоплены в древесину на нижней стороне поперечных досок поперек волокон. Крайние доски настила и поперечные доски соединяют не менее чем одним гвоздем.
Головки забитых гвоздей должны быть утоплены в древесину на 1,0 - 1,5 мм.
Каждая шашка должна быть соединена как с настилом, так и с досками основания не менее чем тремя гвоздями, которые не должны входить в одно и то же волокно шашки и должны быть удалены на максимально возможное расстояние друг от друга.
Допускается по согласованию с заказчиком для изготовления поддонов применять другие типы, размеры и количество гвоздей по технической документации.
При сборке поддонов крепежные элементы устанавливают вертикально на расстоянии не менее 25 мм от торца и кромки досок.
После сборки в шашках и досках не должно быть трещин, образовавшихся при забивании гвоздей.
Шашки и доски из твердых пород древесины предварительно надсверливают. Диаметр отверстия должен быть на 1 мм меньше диаметра детали крепления. Глубина отверстия должна составлять 70% длины детали крепления.
4.1.14 При сборке поддонов не допускаются:
- отклонение габаритных размеров - более 5 мм;
- отклонение от параллельности поверхностей верхнего и нижнего настилов - более 3 мм;
- разность длин диагоналей верхней или нижней поверхности - более 2 мм;
- сквозные зазоры между соприкасающимися поверхностями деталей;
- несквозные зазоры между соприкасающимися поверхностями деталей - более 0,5 мм;
- сколы, сквозные трещины, трещины в местах установки крепежных деталей.
4.1.15 Значение наработки на отказ поддона должно быть не менее 150 операций для двухзаходного поддона и 300 - для четырехзаходного.
4.1.16 Усилие соединения деталей поддона на отрыв (среднее значение из 20 измерений и не менее 75% всех измеренных усилий) должно быть в соединениях не менее, кН:
- 3,0 - промежуточная доска настила - поперечная доска;
- 5,5 - доска настила - поперечная доска - шашка;
- 5,5 - доска основания - шашка.
4.1.17 Требования к характеристикам для испытаний поддонов, методы испытаний и определение рабочих нагрузок в зависимости от применения поддонов приведены в ГОСТ ISO 8611-1, ГОСТ ISO 8611-2, ГОСТ ISO 8611-3.
4.1.18 Поддон должен выдерживать испытание на изгиб верхнего настила при стеллажировании по длине и ширине поддона (жесткость при изгибе, испытание 1 b), по п. 8.1 и рисунок 1 ГОСТ ISO 8611-1; таблица 1 (испытание 6) ГОСТ ISO 8611-2 и ГОСТ ISO 2234.
При этом максимальный прогиб, мм, верхнего настила в зависимости от типоразмера поддона и укладываемого на него груза P = const = 1000 кг; 1250 кг; 1350 кг; 2000 и 3200 кг в течение 30 мин должен быть; не более 2% - остаточный прогиб; после периода релаксации - не более 0,7% от расстояния между опорами поддона L1 (L2).
4.1.19 Поддон должен выдерживать испытание на подъем вилочным захватом погрузчика верхнего настила поддона (жесткость при изгибе, испытание, 2 b) по п. 8.2, таблица 1 и рисунок 2 ГОСТ ISO 8611-1, таблица 1 (испытание 6) ГОСТ ISO 8611-2 и ГОСТ 18211.
При этом максимальный прогиб, мм, верхнего настила под нагрузкой в зависимости от типоразмера поддона с равномерно распределенным грузом на поддоне и при нахождении его на вилах погрузчика или другого транспортного средства для транспортирования поддонов с грузами P = const = 1000 кг; 1250 кг; 1350 кг; 2000 и 3200 кг должен быть не более 20 мм - остаточный прогиб, после периода релаксации - 0 мм.
4.1.20 Поддон должен выдерживать испытание на изгиб верхнего и нижнего настилов поддона при штабелировании (жесткость при изгибе, испытание 4 b) по п. 8.4, таблица 1 и рисунок 4 ГОСТ ISO 8611-1, таблица 1 (испытание 6) ГОСТ ISO 8611-2 и ГОСТ ISO 2234.
При этом максимальный прогиб, мм, настилов в зависимости от типоразмера поддона и укладываемого на него груза под нагрузкой 2,5P = const = 2500 кг; 3125 кг; 3375 кг; 5000 и 8000 кг в течение 24 ч должен быть не более 2% - остаточный прогиб, мм; после периода релаксации - не более 0,7% от расстояния между опорами поддона L1 (L2).
4.1.21 Поддон с выступами должен выдерживать испытание на изгиб верхнего настила при подъеме с помощью строп (жесткость при изгибе, испытание 6 b) по п. 8.6, таблица 1 и рисунок 6 ГОСТ ISO 8611-1, таблица 1 (испытание 6) и ГОСТ ISO 8611-2.
При этом максимальный прогиб, мм, верхнего настила в зависимости от типоразмера поддона и укладываемого на него груза под нагрузкой 1,25P = const = 1250 кг; 1563 кг; 1688 кг; 2500 кг; 4000 кг в течение 10 мин должен быть не более 2%, остаточный прогиб, мм, после периода релаксации - не более 0,7% от расстояния между опорами поддона L1 (L2).
4.1.22 Поддоны всех типоразмеров должны выдерживать испытания: при падении на угол, сопротивление ударам (прочность сборки), вертикально подвешенного поддона с высоты, h = 1 м (диагональная жесткость, испытание 9) по п. 8.9, таблица 1 и рисунок 9 ГОСТ ISO 8611-1, таблица 1 (испытание 6) ГОСТ ISO 8611-2 и ГОСТ 18425.
При этом изменение длины диагонали поддона, мм, после шести падений на один и тот же угол должно быть не более 4% от ее первоначальной длины.
4.1.23 После проведения испытаний не допускаются повреждения и поломка деталей поддона, ограничивающие рабочие показатели или функциональность поддона.
4.2 Требование к сырью и материалам
4.2.1 Детали поддонов изготовляют из пиломатериалов не ниже 2-го сорта: хвойных пород по ГОСТ 8486 и лиственных пород по ГОСТ 2695.
4.2.2 По согласованию с заказчиком допускается изготовлять детали поддонов из пиломатериалов 3-го сорта хвойных пород по ГОСТ 8486 и лиственных пород по ГОСТ 2695.
4.2.3 В качестве крепежных элементов для соединения деталей поддонов применяют фосфатированные или оксидированные гвозди с кольцевой накаткой, винтовые или ершеные гвозди по технической документации.
4.2.4 По согласованию с заказчиком допускается поверхности деталей поддона обрабатывать фунгицидом по технической документации.
4.2.5 Санитарно-гигиенические показатели безопасности материалов, применяемых при изготовлении поддонов, должны соответствовать требованиям технического регламента [1] (если область его действия распространяется на поддоны) и/или установленным законодательством государства, принявшего настоящий стандарт.
4.3 Маркировка
4.3.1 Транспортная маркировка поддонов - по ГОСТ 14192.
4.3.2 Маркировку наносят непосредственно на поддоны и/или на ярлыки с указанием:
- наименования и назначения поддона;
- наименования страны-изготовителя;
- наименования предприятия-изготовителя и его юридического адреса;
- товарного знака (при наличии);
- типа, размера поддона и его условного обозначения;
- массы поддона, в кг;
- массы брутто, в т;
- даты изготовления;
- обозначения настоящего стандарта или другой технической документации, по которой изготовлен поддон;
- символа возможности утилизации "Петля Мебиуса".
4.3.3 Маркировку наносят на русском языке и/или государственном языке страны - изготовителя поддонов с учетом соответствующих требований, установленных законодательством государства, принявшего настоящий стандарт.
По согласованию с заказчиком маркировку наносят на другом языке.
4.3.4 Маркировка должна быть нанесена на продольных сторонах шашек. Маркировку наносят способом выжигания.
Допускается выполнение тиснением с последующей окраской.
Способы, место нанесения и содержание маркировки устанавливают в технической и/или технологической документации на поддоны для конкретных видов продукции с учетом требований и норм, установленных законодательством государства, принявшего настоящий стандарт.
Маркировка должна быть четкой, стойкой к истиранию и легко читаемой.
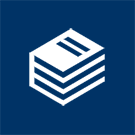