ГОСТ 33796-2016. Межгосударственный стандарт. Моторвагонный подвижной состав. Требования к прочности и динамическим качествам
8.2. Оценка сопротивления усталости
8.2.1 Оценку прочности по коэффициенту запаса сопротивления усталости несущих элементов проводят как при проектировании, так и по результатам проведенных испытаний. Коэффициент запаса сопротивления усталости вычисляют по 8.2.2, а в случае, если определено фактическое значение предела выносливости натурной детали (по результатам стендовых испытаний на усталость) - по 8.2.3.
8.2.2 Коэффициент запаса сопротивления усталости n вычисляют по формуле
(8.1)
где - предел выносливости стандартного образца при растяжении-сжатии с симметричным циклом нагружения, МПа;
- амплитуда напряжений (максимальных в зоне концентрации) цикла, МПа;
- коэффициент, характеризующий влияние асимметрии цикла; принимают
при
,
при
;
- среднее напряжение цикла, МПа;
- теоретический коэффициент концентрации напряжений;
- коэффициент, характеризующий понижение предела выносливости конструкции по отношению к пределу выносливости стандартного образца (коэффициент концентрации).
Предел выносливости принимают по справочным данным или определяют экспериментально по ГОСТ 25.502 на круглых образцах диаметром 7,5 мм или 10 мм.
Для несущих элементов с высотой сечения до 100 мм включительно, работающих на изгиб, а также для зон элементов несущей конструкции, имеющих местную деформацию изгиба листа, коэффициенты запаса сопротивления усталости рассчитывают по формуле
(8.2)
где - предел выносливости при изгибе с симметричным циклом нагружения, полученный по результатам испытаний стандартных образцов или принятый по справочным данным.
Допускается использовать следующие эмпирические зависимости:
;
- для прокатной стали;
- для литых сталей и алюминиевых сплавов.
Значение коэффициента принимают равным:
- 1,4 - для зон концентрации на границах сварных швов (кроме стыковых), в выточках и переходах с радиусами не более 150 мм;
- 1,1 - на границах сварных стыковых швов;
- 1,0 - для других зон.
8.2.2.1 За среднее напряжение цикла как при проведении испытаний, так и при расчете принимают напряжения, возникающие от постоянно действующих вертикальных статических нагрузок
, т.е.
8.2.2.2 При испытаниях амплитуду напряжений цикла определяют на основании экспериментальных данных, полученных при проведении динамико-прочностных испытаний. Значение
определяют в порядке, аналогичном установленному в 6.2.1 для определения динамической составляющей рамной силы.
При проектировании расчетную амплитуду напряжений цикла определяют методом решения задачи вынужденных колебаний динамической модели экипажной части.
8.2.2.3 Значения коэффициента концентрации рассчитывают по формуле:
, (8.3)
где К1 - коэффициент, учитывающий влияние неоднородности материала детали:
- 1,1 - для проката, поковки и штамповки;
- 1,25 - для литых деталей;
К2 - коэффициент, учитывающий влияние внутренних напряжений в детали, принимаемый в зависимости от ее поперечных размеров равным:
- 1,0 - при размере до 250 мм;
- от 1,0 до 1,2 - при размере от 250 до 1000 мм пропорционально размеру;
Кm - коэффициент, учитывающий состояние поверхности детали. В зависимости от способа обработки его принимают равным:
- 1,0 - для полированной поверхности;
- 0,9 - для поверхности после станочной обработки чистовой;
- 0,8 - для поверхности после станочной обработки грубой;
- 0,8 - для поверхности с окалиной;
- 0,8 - для поверхностей стальных литых деталей после пескоструйной обработки;
- коэффициент, учитывающий влияние размерного фактора; принимают в зависимости от наибольшего размера сечения детали h равным:
- 0,8 - при высоте сечения h до 100 мм включ.;
- 0,75 - при высоте сечения h от 100 до 250 мм включ.;
- 0,7 - при высоте сечения h более 250 мм;
К3 - корректирующий коэффициент, используемый для зон сварных соединений, зон выточек и переходов с радиусами менее 10 мм сварных несущих конструкций экипажной части, за исключением сварных несущих конструкций надрамного строения кузова (боковые стенки кузова, крыша кузова, лобовая и торцевая стенка, перегородки и др.).
Значение корректирующего коэффициента К3 принимают равным:
- 1,4 - для сплавов на основе алюминия;
- 1,0 - для малоуглеродистых прокатных сталей типа Ст15, Ст20, Ст3сп;
- 1,2 - для низколегированных прокатных сталей типа 09Г2, 09Г2Д, 09Г2С, 09Г2СД;
- 1,2 - для коррозионно-стойких прокатных сталей.
При применении новых марок прокатных сталей, не применяемых ранее для изготовления сварных несущих конструкций тягового подвижного состава железнодорожного транспорта, предназначенного для эксплуатации на территории государств, принявших стандарт, коэффициент К3 определяют в соответствии с приложением Б.
8.2.3 Если определено фактическое значение предела выносливости натурной детали (по результатам стендовых испытаний на усталость), коэффициент запаса сопротивления усталости n рассчитывают по формуле
(8.4)
где - предел выносливости детали при симметричном цикле нагружения, определенный экспериментально, МПа;
- коэффициент снижения предела выносливости детали по отношению к пределу выносливости стандартного образца.
При известном пределе выносливости детали при асимметричном цикле нагружения коэффициент n может быть вычислен по формуле
, (8.5)
где - предел выносливости при асимметричном цикле нагружения, МПа.
8.2.4 Значения коэффициентов запаса сопротивления усталости, определенных по 8.2.2 или 8.2.3, должны соответствовать значениям, приведенным в 5.5.
8.2.5 Для оценки сопротивления усталости рам тележек и промежуточных рам (балок, брусьев и т.п.) второй ступени рессорного подвешивания проводят стендовые вибрационные испытания на базе 10 млн. циклов нагружения. Испытаниям подвергают один образец.
К объекту испытаний прикладывают статические и динамические (циклические) нагрузки. Величины статических нагрузок принимают равными силам тяжести устанавливаемого на объект испытаний оборудования, включая кузов при максимальной загрузке вагона, с учетом максимальной экипировки вагона.
Величины основных динамических (циклических) нагрузок - динамических составляющих вертикальных сил от веса надрессорного строения ( - для рамы тележки;
- для промежуточной рамы (балки, бруса и т.п.)) и динамических составляющих рамных сил
принимают по результатам динамико-прочностных испытаний конкретного типа МВПС, конструкции которого подлежат стендовым вибрационным испытаниям. При отсутствии результатов динамико-прочностных испытаний конкретного типа МВПС за величины циклических нагрузок принимают увеличенные на 20% значения
,
,
(см. 6.2.1, 6.2.2 и 6.2.3), полученные по результатам математического моделирования движения соответствующего вагона МВПС, но не более значений, вычисленных умножением максимально допустимых величин соответственно показателей, приведенных в 4.1.1, 4.1.2 и 4.1.3, на соответствующие статические нагрузки.
Для рам тележек и промежуточных рам (балок, брусьев и т.п.) второй ступени рессорного подвешивания, нагружаемых в эксплуатации вертикальными силами от веса надрессорного строения и рамными силами, необходимым условием является одновременное нагружение этими силами.
Оценку сопротивления усталости рам тележек и промежуточных рам (балок, брусьев и т.п.) второй ступени рессорного подвешивания выполняют в следующих случаях:
- при изготовлении новой конструкции;
- при модернизации конструкции;
- при смене изготовителя;
- при замене материала для изготовления конструкции;
- при изменении технологии изготовления, влияющей на прочность конструкции;
- при увеличении нагрузок более чем на 10% по сравнению с ранее реализованными при проведении стендовых вибрационных испытаний.
Повторные испытания необходимы, если любая из составляющих нагружения (статическая, циклическая) увеличилась более чем на 10%.
В случае, если в конструкции МВПС применяют рамы тележек, промежуточные рамы (балки, брусья и т.п.), изготовленные разными предприятиями, оценке подлежат конструкции всех изготовителей.
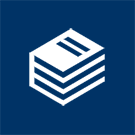