ГОСТ Р ИСО 18437-2-2014. Национальный стандарт Российской Федерации. Вибрация и удар. Определение динамических механических свойств вязкоупругих материалов. Часть 2. Резонансный метод
5. Метод испытаний
5.1. Подготовка образца и его установка
Образцы для испытаний отливают в форме стержня. Отливка должна иметь длину не менее 150 мм и квадратные основания со стороной . Из отливки с помощью ленточной пилы вырезают стержень длиной (100 +/- 10) мм. При необходимости выполняют механическую обработку (шлифовку) оснований стержня. Подготовленный стержень, если его поставить на горизонтальную поверхность, должен стоять вертикально без поддержки. Квадратные концы стержня должны обеспечить надежное соединение образца с установочными блоками.
Допускается использовать стержни круглого сечения диаметром приблизительно от 6 до 8 мм.
Допускается использовать стержни другой длины, но не менее 50 и не более 200 мм.
Примечание 1. У коротких стержней резонансы имеют место на более высоких частотах, что вследствие более интенсивного поглощения энергии вибрации на высоких частотах приводит к меньшему числу пиков в спектре сигнала. У длинных стержней резонансы смещаются в область более низких частот, что часто усложняет испытания вследствие возбуждения нежелательных изгибных колебаний.
Перед тем как прикрепить образец к установочным блокам, измеряют его длину (в метрах) с точностью до четырех значащих цифр в соответствии с ИСО 23529, массу (в килограммах) взвешиванием на весах с точностью до четырех значащих цифр и плотность (в килограммах на кубический метр) методом вытеснения жидкости.
Примечание 2. Для определения плотности может быть применен метод, описанный в [1].
К концам образца с помощью отвердевающих клеев приклеивают стальные установочные блоки (см. рисунок 1). Размеры установочного блока обычно равны 25 x 20 x 10 мм. В качестве клеящего средства обычно применяют эпоксидную смолу или цианоакрилат. Модуль упругости клеящего средства должен быть много выше измеряемого модуля упругости образца. При соблюдении указанных условий клеевое соединение не будет влиять на результаты измерений (см. [2]).
Перед соединением с образцом к каждому из установочных блоков с помощью того же клеящего средства приклеивают блок крепления акселерометра (см. рисунок 1). Форма блока крепления акселерометра должна быть согласована с формой сечения образца. Для образца квадратного сечения блок крепления имеет форму куба со сторонами 6 мм. Для образца круглого сечения сечение блока крепления должно также быть круглым с тем же самым диаметром. Масса акселерометра вместе с блоком крепления должна быть измерена на весах с точностью до трех значащих цифр.
Примечание 3. Блок крепления акселерометра применяют для того, чтобы предотвратить износ и повреждения акселерометра при его многоразовом приклеивании. В приведенной схеме установки акселерометр остается постоянно закрепленным на одной стороне установочного блока. Другой конец установочного блока при смене испытуемого образца каждый раз соединяют с образцом заново.
5.2. Кондиционирование образца
5.2.1. Хранение
Интервал времени между процессом отливки (вулканизацией) образца и его испытаниями, а также время выдерживания образца в заданных условиях перед проведением испытаний - в соответствии с ИСО 23529.
5.2.2. Температура
Перед каждой серией испытаний образцы выдерживают при заданной температуре. Время выдержки должно быть достаточным, чтобы привести образец в тепловое равновесие с воздухом в климатической камере, но не более необходимого и без перегрева, чтобы не допустить искусственного старения образца. Время выдержки зависит от размеров образца и от температуры испытаний. Подробное руководство приведено в ИСО 23529.
5.2.3. Механические воздействия
Обычно механическим воздействиям образец при его кондиционировании не подвергают, поскольку при испытаниях для обеспечения условий свободных колебаний достаточно однократного создания незначительной деформации. Однако в случае больших деформаций следует иметь в виду, что динамические свойства многих вязкоупругих материалов чувствительны к имевшим место ранее механическим и температурным воздействиям. Такие материалы с целью обеспечения воспроизводимости результатов испытаний рекомендуется подвергать предварительному механическому воздействию, позволяющему удалить остаточную "память" материала. Это воздействие состоит в создании не менее шести раз максимальных деформаций при температуре, соответствующей температурному режиму предстоящих испытаний. После механической обработки образец перед испытаниями выдерживают не менее 12 ч для релаксации структуры материала.
5.2.4. Влажность
Известно, что влажность влияет на физические свойства многих упругих материалов, особенно уретанов. Чтобы обеспечить воспроизводимость результатов испытаний, образец выдерживают в контролируемых условиях влажности в течение недели перед испытаниями. Для этого образец помещают в закрытый контейнер с поддерживаемой относительной влажностью воздуха от 50% до 55%. Температура в контейнере при этом должна находиться в интервале от 20 °C до 25 °C. Подробное руководство приведено в ИСО 483.
5.3. Число образцов для испытаний
Чтобы получить представление о возможном разбросе значений характеристик упругих свойств материала рекомендуется проводить испытания на не менее чем трех образцах материала.
5.4. Сбор и обработка данных
5.4.1. При проведении испытаний выполняют следующие процедуры:
a) с помощью вибростенда воспроизводят случайную вибрацию по сигналу управления с анализатора спектра;
b) с помощью двухканального анализатора спектра выполняют БПФ сигналов с двух акселерометров;
c) по результатам БПФ двух сигналов рассчитывают частотную характеристику (отношение ускорений) испытуемого образца и функцию когерентности. Для повышения их точности расчеты выполняют с усреднением по 32 спектрам сигнала. Функция когерентности должна принимать значения не менее 0,95 во всем диапазоне частот измерений;
d) по окончании испытаний анализатор спектра отображает модуль и фазу частотной характеристики образца в диапазоне частот измерений.
По отображенной кривой модуля частотной функции наблюдают резонансные пики в килогерцовой области частот. При этом фаза характеристики совершает несколько переходов через 360°. Типичные графики модуля и фазы частотной характеристики показаны на рисунке 2. Модуль при резонансе определяют в точках скачка фазы на угол
, (1)
где n - номер резонанса.
Примечание 1. Важно помнить, что частота резонанса не та, где наблюдается максимум модуля частотной характеристики, а та, где происходит скачок фазы на угол, рассчитываемый по формуле (1). Пик частотной характеристики всегда наблюдается на несколько более низкой частоте, чем частота резонанса, в зависимости от коэффициента потерь материала.
Примечание 2. На частотной характеристике могут наблюдаться паразитные резонансы, связанные с неправильной установкой образца или отклонением оси образца от направления возбуждаемой вибрации. Эти резонансы связаны с колебаниями в направлениях, перпендикулярных оси образца. Паразитные резонансы легко выделить, поскольку они попадают в интервалы между исследуемыми резонансами и дают несовместимые значения модулей упругости. Паразитные резонансы можно просто не принимать во внимание, но лучше принять меры по их устранению за счет более точного совмещения осей вибровозбудителя и испытуемого образца.
Рисунок 2. Типичная зависимость модуля и фазы частотной
характеристики от частоты
5.4.2. Число наблюдаемых резонансных пиков зависит от модуля упругости и коэффициента потерь материала, но обычно равно от трех до шести. Как видно из рисунка 2, фаза уменьшается с частотой, что означает, что запаздывание сигнала на свободном конце стержня по сравнению с сигналом в месте возбуждения вибрации по мере повышения частоты возрастает.
Величинами, необходимыми для расчетов модуля упругости, являются модуль частотной характеристики на резонансе и частота резонанса. Их определяют следующим образом:
a) по анализатору спектра, настроенному для работы в полном диапазоне частот от 25 Гц до 18 кГц, оценивают значения резонансных частот. Измерения фазового угла проводят с точностью до 5°;
b) на каждом резонансе уточняют значение резонансной частоты, переводя для этого анализатор спектра в режим работы с увеличением масштаба с разрешением приблизительно 1 Гц (если предварительная оценка частоты резонанса была недостаточно точна, то может потребоваться двукратное увеличение масштаба, прежде чем будет получено требуемое разрешение);
c) выполняют окончательную оценку фазового угла с точностью до 0,5°, резонансной частоты с точностью до 0,1 Гц и модуля частотной характеристики с точностью до 0,1 дБ.
5.5. Температурный цикл
Измерения выполняют в диапазоне температур обычно от минус 60 °C до плюс 70 °C, изменяя температуру образца по следующему циклу:
- охлаждают закрепленный в испытательной установке образец до температуры минус 60 °C;
- после достижения температурного равновесия выдерживают образец при указанной температуре в пределах +/- 0,1 °C не менее 15 мин, после чего проводят измерения;
- для проведения следующих измерений последовательно повышают температуру образца с шагом 5 °C;
- при каждом новом значении температуры, для которой выполняют измерения, выдерживают образец после достижения температурного равновесия не менее 6 мин. Во время выдержки температура не должна изменяться более чем на +/- 0,1 °C.
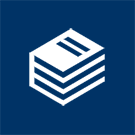