ГОСТ 32569-2013. Межгосударственный стандарт. Трубопроводы технологические стальные. Требования к устройству и эксплуатации на взрывопожароопасных и химически опасных производствах
11. Требования к монтажу трубопроводов
11.1. Общие требования к монтажу трубопроводов
11.1.1. Монтаж трубопроводов следует проводить в соответствии с требованиями настоящего стандарта, планом производства работ (ППР) и проектом.
Монтаж трубопроводов взрывопожароопасных производств с блоками I категории взрывоопасности следует, как правило, осуществлять на основе узлового или монтажно-блочного метода.
11.1.2. Не допускается отступление от проекта и ППР без проведения согласования в установленном порядке.
11.1.3. При монтаже трубопроводов следует осуществлять входной контроль качества материалов, деталей трубопроводов и арматуры на соответствие их сертификатам, стандартам, ТУ и другой технической документации, а также операционный контроль качества выполненных работ. Результаты входного контроля оформляют актом с приложением всех документов, подтверждающих качество изделий.
11.1.4. Отклонение линейных размеров сборочных единиц трубопроводов не должно превышать +/- 3 мм на 1 м, но не более +/- 10 мм на всю длину, если в проектной документации нет других указаний.
11.1.5. Изделия и материалы, на которые истекли расчетные сроки хранения (консервации), указанные в документации, могут быть переданы в монтаж только после проведения ревизии, устранения дефектов, испытания и других работ, обеспечивающих их качество и безопасность применения.
11.1.6. Условия хранения изделий и материалов для монтажа трубопроводов должны соответствовать требованиям технической документации.
11.1.7. Если трубу в процессе монтажа разрезают на несколько частей, то на все вновь образовавшиеся части наносят клеймение, соответствующее клеймению первоначальной трубы.
11.2. Монтаж трубопроводов
11.2.1. При приемке в монтаж сборочных единиц, труб, элементов и других изделий, входящих в трубопровод, необходимо визуальным осмотром (без разборки) проверить соответствие их требованиям рабочей документации и комплектности.
11.2.2. Не допускается монтаж сборочных единиц, труб, деталей, других изделий, загрязненных, поврежденных коррозией, деформированных, с поврежденными защитными покрытиями.
11.2.3. Специальные виды очистки внутренних поверхностей трубопроводов (обезжиривание, травление), если нет других указаний в рабочей документации, могут выполняться после монтажа в период пусконаладочных работ.
11.2.4. Трубопроводы допускается присоединять только к закрепленному в проектном положении оборудованию. Соединять трубопроводы с оборудованием следует без перекоса и дополнительного натяжения. Неподвижные опоры прикрепляют к опорным конструкциям после соединения трубопроводов с оборудованием.
11.2.5. При сборке трубопроводов под сварку не допускается нагрузка на сварной стык до его полного остывания после сварки и термообработки (если она необходима).
11.2.6. Расстояние от поперечного сварного соединения до края опоры или подвески должно обеспечить при необходимости возможность его термообработки и контроля.
11.2.7. Вварка штуцеров, бобышек, муфт и других деталей в местах расположения сварных швов в гнутые и штампованные детали трубопроводов не допускается.
В обоснованных случаях в гнутые и штампованные детали трубопроводов допускается вварка одного штуцера внутренним диаметром не более 25 мм.
11.2.8. Перед установкой сборочных единиц трубопроводов в проектное положение гайки на болтах (шпильках) фланцевых соединений должны быть затянуты, сварные стыки заварены (при необходимости - термообработаны) и проконтролированы в соответствии с требованиями рабочей документации.
11.3. Отклонение от перпендикулярности
11.3.1. Отклонение от перпендикулярности уплотнительной поверхности фланца к оси трубы или детали не должно превышать величин, приведенных в таблице 11.1.
Таблица 11.1
Отклонение от перпендикулярности к оси уплотнительной
поверхности фланца
В миллиметрах
Диаметр трубы (детали) | Отклонение |
От 25 до 60 | 0,15 |
От 60 до 160 | 0,25 |
От 160 до 400 | 0,35 |
От 400 до 750 | 0,5 |
Св. 750 | 0,6 |
11.3.2. Несоосность уплотнительных поверхностей сопрягаемых фланцев не должна превышать удвоенного отклонения, указанного в таблице; при этом зазор должен быть одинаковым по всей окружности и соответствовать толщине прокладки.
11.3.3. При сборке фланцевых соединений следует выполнять требования 6.2.12.
Не допускается выравнивание перекосов фланцевых соединений натяжением болтов (шпилек), а также применением клиновых прокладок.
11.3.4. Монтаж трубопровода разрешается только после установки и закрепления опорных конструкций и подвесок в соответствии с требованиями проекта. Сборочные единицы и узлы трубопроводов должны быть уложены не менее чем на две опоры (или закреплены на двух подвесках) с защитой их от опрокидывания или разворота.
11.3.5. Расстояние от фланца арматуры или фланца компенсатора до опоры, подвески, стены, перегородки или перекрытия должно быть достаточное для обслуживания фланцевого соединения.
11.3.6. В местах расположения измерительных диафрагм вместо них при монтаже допускается временно устанавливать монтажные кольца в соответствии с НД.
11.3.7. Арматура, имеющая механический или электрический привод, до передачи ее в монтаж должна проходить проверку работоспособности привода.
11.3.8. Положение корпуса арматуры в пространстве относительно направления потока среды и расположение осей штурвалов определяются проектом.
11.3.9. Трубопроводную арматуру следует монтировать в закрытом состоянии. Разъемные и сварные соединения арматуры должны быть выполнены без натяжения трубопровода. Во время сварки приварной арматуры ее затвор необходимо полностью открыть, чтобы предотвратить заклинивание его при нагревании корпуса. Если сварка производится без подкладных колец, арматуру по окончании сварки можно закрыть только после очистки ее внутренних полостей.
11.3.10. Холодный натяг трубопроводов можно проводить после выполнения всех сварных соединений (за исключением замыкающего), окончательного закрепления неподвижных опор на концах участка, подлежащего холодному натягу, а также после термической обработки (при необходимости ее проведения) и контроля качества сварных соединений, расположенных на всей длине участка, на котором необходимо произвести холодный натяг.
11.3.11. Осевые компенсаторы следует устанавливать соосно с трубопроводами.
Допускаемые отклонения от проектного положения присоединительных патрубков компенсаторов при их установке и сварке должны соответствовать документации на компенсаторы.
11.3.12. При установке компенсаторов направление стрелки на корпусе должно совпадать с направлением движения вещества в трубопроводе.
11.3.13. При монтаже компенсаторов должны исключаться скручивающие нагрузки относительно продольной оси и провисание их под действием собственной массы и массы примыкающих трубопроводов, а также должна обеспечиваться защита гибкого элемента от механических повреждений и от попадания искр при сварке.
11.3.14. Монтажную длину сильфонных, линзовых и сальниковых компенсаторов принимают с учетом поправок на температуру наружного воздуха при монтаже.
11.3.15. Компенсаторы следует растягивать до монтажной длины с помощью приспособлений, предусмотренных конструкцией компенсатора, или натяжными монтажными устройствами. Растяжку (сжатие) компенсаторов оформляют актом.
11.3.16. При монтаже сальниковых компенсаторов обеспечивают свободное перемещение подвижных частей и сохранность набивки.
11.3.17. Сварное соединение, перед сваркой которого следует проводить растяжку компенсатора, должно быть указано в рабочей документации. Во избежание снижения компенсационной способности компенсатора и его перекоса следует использовать соединение, расположенное на расстоянии не менее 20DN от оси симметрии компенсатора.
11.3.18. Линзовые, сильфонные и сальниковые компенсаторы следует устанавливать в сборочных единицах и блоках коммуникаций при их укрупненной сборке, применяя при этом дополнительные жесткости для предохранения компенсаторов от деформации и от повреждения во время транспортировки, подъема и установки. По окончании монтажа временно установленные жесткости удаляют.
11.3.19. Отклонение трубопроводов от вертикали (если нет указаний в проекте) не должно превышать 2 мм на 1 м длины трубопровода.
11.3.20. При монтаже вертикальных участков трубопроводов в рабочей документации должны быть предусмотрены меры, исключающие возможность сжатия компенсаторов под действием массы вертикального участка трубопровода.
11.3.21. Окончательное закрепление трубопроводов в каждом температурном блоке при укладке на эстакадах, в каналах или в лотках должно проводиться, начиная от неподвижных опор.
11.3.22. Трубопроводы, пересекающие железнодорожные пути, автодороги, проезды и другие инженерные сооружения, следует монтировать после согласования прокладки в установленном порядке.
11.3.23. Антикоррозионную защиту и тепловую изоляцию трубопроводов до установки их в проектное положение допускается выполнять с условием обеспечения сохранности защитного покрытия при производстве последующих монтажных работ.
11.4. Особенности монтажа трубопроводов с номинальным давлением свыше 10 МПа (100 кгс/см2)
11.4.1. Сборочные единицы и детали трубопроводов должны соответствовать ГОСТ 22790 и другой НД. При приемке в монтаж трубопроводов и других изделий следует проверять:
- резьбовые присоединительные концы труб, деталей и арматуры - прокручиванием деталей, например фланцев;
- резьбу шпилек - прокручиванием гаек;
- геометрические размеры присоединительных концов труб и соединительных деталей, арматуры, фланцев, муфт, крепежных деталей и прокладок в количестве 2% от каждой партии, но не менее 2 штук;
- соответствие количества труб, соединительных деталей, фланцев, линз, муфт, арматуры, крепежных деталей и прокладок количеству, указанному для этих партий в сопроводительной документации.
Арматура, исполнительные механизмы, применяемые в схеме контроля, управления и противоаварийной защиты технологических процессов, перед установкой должны проходить испытания на прочность и плотность основных деталей и сварных швов, герметичность относительно внешней среды, герметичность затвора и функционирование с оформлением актов или с записью в паспорте, журнале.
Требования к очистке, смазке, сборке, соосности и зазорам в разъемных соединениях трубопроводов устанавливаются в проектной или в нормативно-технической документации.
Не допускается устранять зазоры, непараллельности или несоосности между сборочными единицами или деталями путем натяжения трубопроводов.
11.4.2. Крепежные детали должны быть одной партии и должны быть затянуты с помощью устройств, обеспечивающих контроль усилия натяжения. Порядок сборки соединений и контроля усилий затяжки должен быть принят из нормативной документации.
11.4.3. В собранном фланцевом соединении шпильки должны выступать из гаек не менее чем на один шаг резьбы.
Не допускается установка шайб между фланцами и гайками. При навернутом фланце резьбовая часть присоединительного конца трубы должна выступать от торца фланца на один шаг резьбы.
11.4.4. Расстояние между фланцевыми, резьбовыми соединениями и отверстиями в стенах, перегородках, перекрытиях и других строительных конструкциях следует принимать с учетом возможности сборки и разборки соединения с применением механизированного инструмента, при этом для трубопроводов с номинальным диаметром DN <= 65 указанное расстояние принимают не менее 300 мм и не менее 600 мм - для трубопровода диаметра.
11.5. Документация и маркировка трубопроводов или сборочных единиц, поставляемых заводами-изготовителями
11.5.1. Каждый трубопровод или сборочная единица поставляется заказчику со следующей документацией:
- сборочный чертеж трубопровода или сборочной единицы в двух экземплярах;
- паспорт на сборочные единицы стальных трубопроводов комплектных трубопроводных линий (1 экз.);
- паспорта на арматуру и детали трубопровода, крепежные детали и уплотнения (1 экз.);
- сведения о подтверждении соответствия (при необходимости) (1 экз.);
- ведомость на упаковку (комплектовочная ведомость) в одном экземпляре;
- упаковочный лист в трех экземплярах, из которых один экземпляр отправляется почтой, один экземпляр помещают в упаковочном ящике, один экземпляр - на упаковочном ящике.
11.5.2. Сборочные единицы из нержавеющих сталей и стали 20ЮЧ маркируются яркой несмываемой краской.
11.5.3. Сборочные единицы из сталей, кроме нержавеющей и стали 20ЮЧ, маркируют клеймением.
11.5.4. Маркировку следует наносить на расстоянии не менее 200 мм от одного из присоединительных концов трубы, с указанием в числителе шифра технологической установки, в знаменателе - шифра линии трубопровода. Маркировать надлежит шрифтом в соответствии с НД.
11.5.5. Схема маркировки сборочных единиц должна быть единой для всех трубопроводов в технологической схеме или проекте.
Места маркировки обводят яркой несмываемой краской и покрывают бесцветным лаком.
11.5.6. Детали и арматура, не вошедшие в сборочные единицы, маркируют несмываемой краской номером трубопроводной линии по монтажной спецификации.
11.5.7. Каждое упаковочное место труб, поставляемых метражом и входящих в поставочный блок, маркируют с указанием номера технологической установки, номера поставочного блока, номера трубопроводной линии и буквы "Т". Бирки с маркировкой, нанесенной ударным способом, крепят с обоих концов упаковки.
11.5.8. На каждом грузовом месте маркировку наносят на ярлыках или непосредственно на торцевых и боковых стенках ящиков яркой несмываемой краской с указанием номера грузового места, числа грузовых мест в данной трубопроводной линии, получателя и его адреса, отправителя и его адреса, массы (нетто, брутто), габаритных размеров грузового места, манипуляционных знаков ("верх", "не кантовать", "место строповки", "центр масс").
11.5.9. С каждой трубопроводной линией потребителю направляется следующая техническая документация:
- паспорт трубопровода;
- сведения о трубах и деталях трубопровода;
- сведения о сварных соединениях;
- перечень арматуры, входящей в сборочные единицы стальных комплектных технологических линий;
- акт гидравлического испытания сборочных единиц;
- акт ревизии и испытания арматуры;
- спецификация;
- заключение.
Формы документации приведены в Приложениях М и Н.
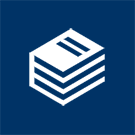